Emphasis on recycling and granulators
From Austrian Erema's recycling system and Maag's screenchangers to Cumberland's granulators, processors will have the latest equipment on hand.
Recycling system specialist Erema will exhibit its TVEplus recycling system for difficult waste materials including full-surface and multi-layer printed packaging films. It includes new and improved downstream components in terms of technology, maintenance and cleaning from the hot die face pelletiser to the drying centrifuge.
It will also showcase other solutions like tailor-made systems for polyolefins and technical plastics, bottle-to-bottle-PET recycling systems, in-line technologies for the direct production of films, fibres and strapping from PET bottle flake with Vacurema technology including automatic melt filters and pelletising systems. A subsidiary, 3S of Roitham, specialists in components such as screws, cylinders and intake parts for extrusion, will also be at the stand to present a new system for measuring the wear on extruder cylinders and, with the now established Lasex process, screws that are resistant to wear.
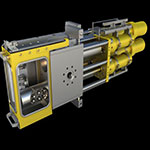 |
Swiss company Maag's screenchangers now also meet the requirements of direct recycling processes, such as the fabrication of food wrapping films from PET bottle flakes in one process step. In the newly developed CSC/BF-PE screenchangers, this has become possible thanks to the fully automatic cleaning of the screens that can be adjusted to any kind of process. The quantity of material needed for backflushing of the screens is collected in a permanently flushed accumulating space and will then clean the dirty screen cloth outside the production process by backflushing. In this way, variations in pressure and volume are to the greatest extent avoided and the effects on the final product are minimized.
The flow channel geometry, which is entirely free from any dead spots as well as the free setting of backflush pressure, quantity and time facilitates the processing of all marketable recycling plastics and thermally sensitive polymers. Upon the introduction of production line specific set points into the control system, the backflush filter changes to the operating mode and starts the fully automatic cleaning of the screens that is controlled by pressure or time and depends on the level of dirt accumulation. These screenchangers are based on the double-piston design that does not require additional seals and ensures a reliable and leak-proof operation.
Under the US-based ACS Group, Cumberland Engineering will show its 1018x series granulator with optional feed roll, its latest CT500 size reduction aimed at the recycling of large containers and blow moulded objects and the 1620x series that will feature an optional blower system.
|