Auxiliaries for powering processing
Auxiliary equipment manufacturers will have a lot to shout about, given that the K2010 show, from 27 October to 3 November, is held once in three years. Below are highlights from some major equipment suppliers like Wittmann, K-Tron, ACS Group, Maguire and Agr.
Austrian company Wittmann, which also has another subsidiary Wittmann Battenfeld that will exhibit moulding machines and robots will display a host of products including its latest WFC 100 water flow measuring unit, which is a regulator and flow measuring gauge. In drying, it will show the Drymax Aton that unites the advantages of a constant dewpoint with high energy efficiency by using a new structure of the wheel as well as by a patented operating mode known as EcoMode. Wittmann will also have several new conveying products like the centralised control eMax24, the central filter station XM/B and the Feedmax B105 compact vacuum loader.
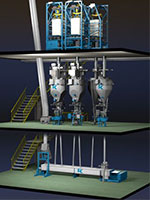 |
/
US supplier K-Tron will showcase various stations including its 2415 Premier vacuum receiver on top of a KT35 twin-screw feeder completed with an ActiFlow bulk solids activator. Another station will feature a FB130 loss-in-weight belt feeder with a P10 vacuum receiver. Other elements of the system include a bag dump station, PD vacuum blower with housing and 2400 Series filter group.
ACS Group company AEC, meanwhile, will showcase the VacTrac Series 24/128 controller with enhanced graphics and control of up to 24 vacuum conveying pumps, 128 loading stations and 128 purge valves. The 24/128 controller utilises a DeviceNet distributed I/O network, with standard features that include an Allen-Bradley CompactLogix controller with 10" color touch-screen operator interface.
AEC will be showcasing what it says is one of its most versatile blenders, the BD 500 that can process materials at a rate of 0.5-68 kg/hour. It will also have its first green portable chiller, the GP series, which is said to be one of the first in the industry to offer R410a refrigerant designed to meet the new regulatory requirements that took effect in January 2010. An electronic modulating capacity control maintains leaving fluid temperature to within 0.1°F and electronic sensors with digital readout include leaving and entering fluid temperatures, compressor suction pressure, compressor discharge pressure, condenser inlet temperature, superheat, sub-cool, pump pressure and tank level.
Another US company Maguire will put forth its upgraded MGF gravimetric feeder, said to provide more than double the throughput of the original system (36 kg/hour) but with the same compact size and 40% lower price over competing gravimetric units. Used for feeding colourants and additives, the new MGF system is driven by a motor that is smaller than the one in the earlier feeder. Also new is a networking option that has been deployed by users of Maguire's Weigh Scale Blenders. Controllers for the MGF feeders can now be networked with the Gravimetric Gateway or G2 software.
The accuracy of the MGF feeder is said to stem from the use of load cells to monitor the loss in weight of colorant in a hopper (mounted on the load cell) as the material is fed into the processing machine by an auger. Software in the feeder control scans data on colour consumption every half-second and automatically adjusts dispensing when a predetermined amount of accumulated error is detected.
Agr International, which provides equipment for management and testing of plastic containers will introduce a Process Pilot closed-loop control system. It is a real-time, process management programme that works in conjunction with Agr's PETWall Profiler system to automate the management of blow moulding production.
In addition, it will showcase its PETWall Profiler that offers in-the-blow moulder process and quality control for PET containers as well as critical process management tools; the OptiCheck system that features a new level of vision-based quality management for rigid plastic containers and the PPT3000 packaging pressure tester for high-precision, temperature compensated pressure and volume expansion testing of plastic bottles.
|