New blow moulding technology allows TPEs for medical bags/devices
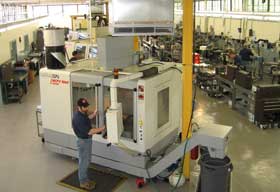
US blow moulding specialist FGH Systems Inc. and materials firm Teknor Apex Company have developed technology for high-volume extrusion blow moulding of thermoplastic elastomers (TPEs) for breather bags and other hollow medical devices, making possible a more efficient and lower-cost alternative to latex and nitrile butadiene rubber (NBR), say the companies.
Breather bags posed a design and processing challenge because they must be pleated to lie flat when not in use yet form a round “balloon” with uniform wall thickness when inflated, noted Eric Hohmann, owner of FGH Systems.
“While TPEs—TPVs in particular—have found use in the injection blow moulding process for parts like automotive rack and pinion boots and ducts, extrusion blow moulding has normally been used with stiff or non-elastomeric resins like HDPE, PP, and PVC,” said Hohmann. “For the breather bag, the challenge was to produce a complex part in a continuous extrusion process with an eight-cavity mould.”
While injection moulding produces solid parts, blow moulding creates hollow parts in core-less moulds in which pressurised air is used to force a molten plastic parison against the wall of the mould to form a finished part.
“In extrusion blow moulding, control of parison wall thickness is critical, and any inconsistencies in the raw material affect parison quality,” noted Ross Van Royen, senior market manager of regulated products for the TPE Division of Teknor Apex. “If viscosity is too high, melt fracture occurs during blowing, but if it is too low, the parison will be unstable.”
FGH Systems supplied the Milacron Uniloy shuttle blow moulding equipment while US-based Teknor Apex produced a standard blow moulding compound, Medalist MD 12445, for replacing latex, NBR, or PVC.
The compound is a 45 Shore A grade, is sterilisable by means of gamma irradiation or ethylene oxide and is said to exhibit a high level of tear resistance. It also boasts high melt strength for good parison formation and consistent flow properties for improved parison stability. At the same time, products made with this compound exhibit the same elasticity as latex and look and feel the same, say the firms.
Breather bags are used during surgery to control the flow of air to a patient under anesthesia. They are single-use, disposable items, capable of being inflated by compressed air. Sizes vary to accommodate patient sizes or ages.
Historically these bags were made of natural-rubber (NR) latex in a process called dip moulding. Though protein allergies forced a move from NR latex to NBR latex, the substitute was more expensive than NR latex and the dipping process more inefficient. TPE bags provide significant cost savings because extrusion blow moulding replaces labour-intensive dip moulding as well thermoplastics have no need for the curing step required for thermoset rubber, and has lower raw material costs. In addition, TPEs avoid concerns about the extractable or leachable remnants of curing agents.
(PRA)Copyright (c) 2016 www.plasticsandrubberasia.com. All rights reserved.