Borouge Innovation Centre to further UAE’s impact on global plastics industry
Also, download this story from the electronic issue here
Borouge, the polyolefins giant, has opened the doors of its state-of-theart Innovation Centre in Abu Dhabi, UAE. The new Innovation Centre serves as the focal point of innovation activity in the field of polymer development and application technology.
“With the drive for sustainable innovation supported by proprietary Borstar technology and our advanced research capabilities, Borouge is committed to add value to life by shaping the plastic materials of the future," says Balakantha Rao Kona, Product Development Manager, Borouge Pte Ltd
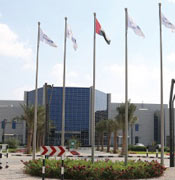
With more than 70 professionals and technicians from 20 different nations, the Centre provides value-added plastics solutions for customers worldwide, focusing on the infrastructure, automotive, and advanced packaging industries.
The investment includes extensive laboratory and application pilot resources, supporting Borouge’s unique capability in providing expertise in polymer analysis, processing, and application testing.
Innovation plays a vital role in the Borouge strategy and its value creation through innovation’s mission.
Product development focuses on high-performance, costeffective, and differentiated polymer solutions that ensure the success of Borouge customers throughout the value chain while simultaneously helping to address some of the major global sustainability challenges.
The Borouge Innovation Centre also collaborates with the European innovation centres of Borealis, local and international educational institutions, and many key industry players.
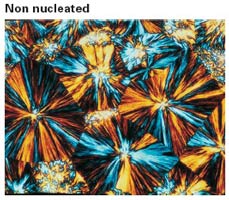
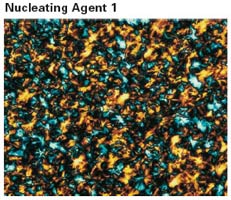
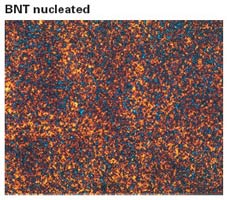
BNT technology
A great example of innovation is the Borstar Nucleation Technology (BNT). The nucleating effect of BNT is obtained in the polymerisation reactor (in situ) during the manufacture of polypropylene (PP).
This is in contrast to the standard approach of adding a nucleating agent during pelletisation. Borstar Nucleation Technology has a number of advantages compared with conventional nucleation:
- Strong and consistent nucleation effect
- Rapid crystallisation and higher crystallisation temperature
- Inertness and no effect on taste and odour
- No impact of colours on shrinkage of the polymer
- Full compliance with food contact regulations

BNT advantages translate into benefits for converters and enable sustainability
- Improved stiffness allowing for lower wall thicknesses and enables down-gauging of end product without compromising other properties
- 10-20% cycle time reduction (mainly through reduced cooling time and easier demoulding due to faster crystallisation)
- Up to 10% energy savings through the possibility of reducing extruder temperature
- Lower carbon and water footprint achieved by cycle time and energy reduction
- Good dimensional stability (limited impact of colouring on shrinkage, which allows fast colour change during production without the need to change process parameters).
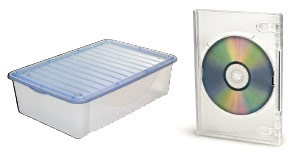
RJ766MO is a material based on BNT developed by Borouge, it is a clear example of value creation through innovation with delivery of significant benefits from the converter to the end user. RJ766MO is suited for very thin walls and long flow paths and can be used for applications such as large storage boxes, transparent food packaging, media packaging and in-mould labelled packaging.
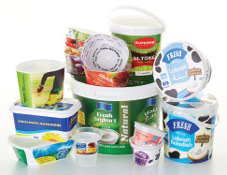
Proven benefits of RJ766MO versus a market reference
- Excellent processability
- >10% reduction in cycle time, leading to higher productivity or lower machine time
- Reduction in processing temperatures leading to lower energy consumption
- Optimal stiffness and impact balance
- Excellent organoleptics
- Overall lower carbon footprint
Copyright (c) 2015 www.plasticsandrubberasia.com. All rights reserved.