Thailand, moving past the growth crossroads
Also, download this story from the electronic issue here
Navigating through economic languor, Thailand is steering towards recovery through its growth industries, says Angelica Buan, based on interviews with exhibitors at the recently concluded T-Plas show in Thailand.
The oft-mentioned bombing incident in mid-August at Bangkok’s major business district was the last string that snapped off Thailand’s stability. Other factors have also added on to the declining economic situation, such as the weakening currency projected to slide further to nearly THB37 per US$ dollar by year end, low domestic demand and exports estimated to contract by 3.5%.
Early in July, the Asian Development Bank (ADB) had already cut back on its growth forecast for Thailand to 6.1% from 6.3% on an underperforming GDP. With the recent developments, the country has recently devolved its 2015 economic growth forecast from 3% to 2.7%. China’s slowdown is weighing down the Asian economies and particularly, Thailand. The yuan depreciation (by nearly 2% in August) has hit the already weak exports in the country.
Nevertheless, Thailand’s resolve against political, economic or even catastrophic havoc is its fighting spirit.
Still a manufacturing ghetto
The 17th largest manufacturer in the world, Thailand’s manufacturing sector is sitting on a ledge. As of July, Thailand’s manufacturing production index reportedly slid 5.3%, compared to the previous year, based on low production and exports of most key industrial goods, according to the Office of Industrial Economics. This is except for the automotive sector, which showed an increase of exports of more than 14% over the same period.
Hope springs eternal. By the time the ASEAN Economic Community (AEC) integration takes effect by the end of the year, Thailand is expected to rein in its spot as a manufacturing powerhouse in the region.
“Manufacturing in Thailand is the most important sector and accounts for 34% of our GDP,” stated Dr Atchaka Sibunruang, Minister of Industry, during the opening of the recent Pack Print International and T-Plas show held from 26-29 August in Bangkok. Organised by Singapore-headquartered Messe Düsseldorf Asia, the show gathered together international industry players in plastics and rubber products; as well as printing and processing machineries.
Sibunruang summed up the current state of the relevant sectors. “The Thai printing, packaging, and the plastics and rubber sectors face immense price pressures, overcapacity in the industry and competition from cheaper regional manufacturers.
Rising costs of operations are further eroding their declining profit margins,” she said.

Scoring strong points
Exhibitors at the Bangkok-held show had mixed opinions about Thailand’s market positioning and its manufacturing industry.
“The Thai market is really starting to grow and develop and become of high quality,” Michael Parrington, Partner at Italy-headquartered auxiliary equipment firm Moretto Asia Pacific, told PRA in an interview during the exhibition. “I see the quality of equipment used by local manufacturers and the quality of their products improving. Thailand is in a very good position in Asia to grow and become one of the prominent plastic production countries in the region,” Parrington said.
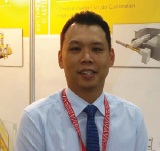
“The recent events that happened in the country are not deterring our plans. We are still forging ahead,” affirmed Raymond Wong, Sales Manager Asia Pacific for Austria-headquartered recycling machine maker NGR (Next Generation Recycling).
“Regardless of the economic situation, the market is continuing to go up. The Thai market is big if we look at the overall Southeast Asia market for Dr Collin, which has been here for over ten years now via our agent LMS,” said Corné Verstraten, Sales Director and Joint Partner of Dr Collin, a German maker of pilot and laboratory lines.
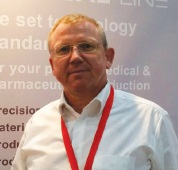
“For this reason, we decided to open a service centre here. We will formally open it by the first quarter of 2016. Thailand will be the main service point for the region for the machines we will be selling directly from Germany. From Bangkok, we can easily go to China and South Korea, for example,” said Verstraten. He also added that Malaysia and Singapore are “very good markets”.
Focusing on the medical sector
Germany-based co-rotating twin-screw extruder manufacturer Liestritz Extrusionstechnik is focusing on the pharmaceutical segment for its extruders.
“There is so much in the pharmaceutical industry that is extruded,” said Alf Hofstetter, General Manager Business Unit Extrusion, adding that the company’s strength is masterbatch and compounding.
He also added that Thailand is a good market for Liestritz as it was one of the first markets in Asia that the company entered. “Our machines have been used by chemical companies in the Map Ta Phut area, as early as in the 1990s,” Hofstetter said.
At T-Plas, Liestritz was promoting its turnkey solution, the ZSE MAXX series, through which, Liestritz could offer the ideal combination of high specific torque (15 Nm/cm3) and high volume (DD/ID=1.66), according to Hofstetter.
“The medical industry is a focus area for us, especially here in Southeast Asia, and likewise in Thailand. This industry is quite strong, with the growing population and therefore increasing support for medical care,” said Collin’s Verstraten.
The company introduced its T-filter, which is used for automated quality control in the extrusion and recycling process. “These are very small extruders with the same functionality of big extruders; very simple, lightweight and compact, which can be placed on a table.”
Collin supplies laboratory, pilot and medical lines for testing, product development and quality control.
Verstraten explained how these technologies can benefit the Thai market. “There are many big polymer producers here in Thailand that can support their customers in the packaging industry by doing R&D using our lines.”
Specific to the Thai market, US extrusion machinery specialist Davis-Standard offers multiple equipment solutions for medical tubing and cast film applications. The company‘s subsidiary in Suzhou, China, also has an in-house laboratory that features a high-speed FPVC extrusion system and multi-purpose microbore tubing line to support process development.
The Pawcatuck-based firm has a strong foothold in Asia, particularly with its converting systems.

“Davis- Standard has always played a significant role in Southeast Asia’s cast lamination film market as the first company to supply five-layer systems and machines over 5 m wide. The market continues to evolve as demands for improved physical/barrier properties and lower operating costs drive structures to more and more layers. Davis-Standard is addressing that need with a new extrusion complex that allows converters to produce CPE and CPP while having the capability to process films with as many as six or seven layers,” said Adrian Gomez, Business Manager Asia Pacific at Davis-Standard.
Taste of new breakthroughs
Meanwhile, T-Plas also offered a plethora of new products and technologies, which exhibitors said would enhance the products and production quality of the local industry.
Wong of NGR said that the manufacturing sector, particularly the plastics sector, can take advantage of what NGR has to offer. “We have manufacturing equipment for recycling for three main markets: post-industrial, postconsumer and PET recycling. In Thailand, we are pushing our main machine, the S-Gran, for post-industrial recycling. It can accept any form of recycled material, which could be in the form of film, sheet or bulk. We are also promoting the P: React system (based on Liquid State Polycondensation or LSP), which is able to increase the IV or viscosity level of PET.”
The three-year old technology (launched at K2013) is a process that is said to considerably enhance the material properties of PET for PET converters as well as end-of-life PET recyclers seeking production scrap, such as fibres, fabrics, wovens and non-wovens, preforms, strapping tapes and films, to be re-processed into quality resin.
Moretto presented its Original Thermal Exchange (OTX). Parrington said, “We are investing a lot in R&D to develop new technology especially to save energy and to ensure that there are minimal defects.”
“With the help of our in-house “super computer”, which Moretto has (via the Leonardo project) and is one of the very few of such computers in Europe (being able to perform 22,000 billion operations/second), we have developed a hopper that allows materials to flow through with the perfect mass flow. This has been a problem of the industry for many years, and one that Moretto has finally solved,” he claimed.
The OTX addresses the issue of flow problems of the granule and permits more uniform ppm moisture in less time, said Parrington.
“Our technology, which is targeted for PET preform bottle manufacturing, can benefit the local industry in terms of giving manufacturers the chance to be world-class producers as well as export to markets that expect high quality products and at the same time allow savings on manufacturing costs,” said Parrington.
Demand in the bag
Indian extrusion machinery manufacturer Rajoo Engineers has supplied blown film lines for a wide range of applications from shopping bags to flexible packaging, food packaging and barrier packaging, according to Jinesh Shah, Deputy General Manager-Sales.
“I see a huge demand for film and sheet lines for flexible packaging and lamination film, since there are a number of converters who are making flexible packaging and pouches. Meanwhile, shrink film for holding canned drinks, bottled water or small cosmetic items is also popular,” Shah commented. He also said that there is a growing market potential for disposable drinking cups. The Gujarat-sited Rajoo has had a sales representative in Thailand for seven years.
BSW Machinery, the Austrian conversion machinery subsidiary of Windmöller & Hölscher (W&H), introduced its newest extrusion technology for indexed perforation. Rene Winkler, Area Sales Manager at BSW, told PRA that with the nanoTex cyclo unit (in line with the converTex valve bag conversion line) the bag’s weight can be lowered significantly through indexed micro perforation, without jeopardising strength.
“At the filling stage with the automated filling equipment, these bags are perforated with small holes. The micro perforation has been the industry standard for woven PP bags. This process has been integrated in the converTex bag conversion machine series for many years to create smaller holes than micro perforation for ventilation. The benefit is significant reduction of dust escaping through the vent holes. However, each hole weakens the tapes that define the strength of the bag. Especially the feather edges are vulnerable when handling or dropping the bags.”
He also explained that the new technology will allow producers of cement bags to reduce their material usage as well as overall thickness and weight of the bag.
Another new technology is the tiraTex tape extrusion line for highly oriented PP tapes for woven PP bags. The newly developed extruder E105P for tiraTex allows for increased tape tenacity at high elasticity, said Winkler. Furthermore, the optionally available direct torque drives of the tiraTex extruder lower energy use of the extruders by up to 5%.
Malaysia-based Limax Industries, a manufacturer of bag converting machines, presented its new offering, Limax Gapa 1100 machine, which is “the fastest clamp stack bottom seal machine in the market”, according to Director Dr KS Teo. With a mechanical speed of up to 200 cycles/minute and a line speed of 120 m/minute, this machine can convert onelayer 5-micron bags up to four-layer 150-micron bags, with a unique flying knife system.
“We have already sold a machine of this type in Thailand,” said Teo. Besides the fast cycle, another feature of the machine is that the components are mainly imported from Europe and the US.
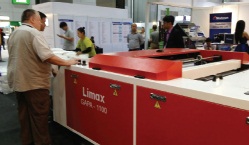
Healthy neighbourly competition
The lingering situation on the economic front has sent some large companies packing up. Investments are also starting to flow to regional neighbours. The Bank of America Merill Lynch cited that in 2013, FDI growths made a jump in Indonesia at 17% and Malaysia at 19%.
Meanwhile, Vietnam, although found to achieve a relatively modest FDI increase, is garnering strength as a likely production route for major manufacturers.
According to Vietnam’s Foreign Investment Agency of the Ministry of Planning and Investment, the country has seen a fresh influx of FDIs over the January to August period, where disbursed capital climbed 7.6% to US$8.5 billion, compared to the same period a year ago. Further, processingmanufacturing accounts for nearly 78% of the newly licenced and additional FDI capital routed to Vietnam over the eightmonth period.
Contributing to its appeal, Vietnam has relatively low wages placed at an average US$197/month in 2013, against the US$391/month for Thailand and US$613/month for China, according to the International Labour Organisation.
Engel, which has sales representatives and subsidiaries in 85 countries worldwide, will soon be branching out to Vietnam, initially with an office set up in Ho Chi Minh, Robert Bodingbauer, President of Austria-headquartered injection moulding machine manufacturer Engel Korea told PRA.
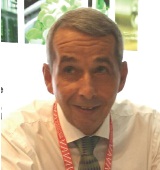
The company picked Vietnam on grounds that several large companies are briskly exporting to Vietnam and production has shifted from China and Thailand to Vietnam. Nonetheless, Bodingbauer opines that the latter’s pace is moderate while Thailand and Indonesia are “a little bit down”; and the situation in Malaysia, Singapore and the Philippines remains unchanged.
Meanwhile, Myanmar, Cambodia and Laos, he observes, are not yet ripe for broader market penetration. “By far, China is dominating our Asian operations,” he said, further adding that with the currency and market situation under the weather, “we have to be careful with our money management.”
Another company eyeing other countries apart from Thailand is Davis-Standard, according to Gomez, who said that the company is looking to promote its machinery in Myanmar and Vietnam, in the medium to long term.
As well, Gomez views India as taking the reins over as China slows down. “Region-wise, India, being part of Asia, will emerge to take over as the fastest growing economy in the world. Southeast Asia is still developing while China has probably reached its saturation point. Its growth seems to be in a plateau, which is expected as it can only develop so much. Although some of its industries are still growing,” he said.
Meanwhile, Germany’s Liestritz, which has a regional office in Singapore, sees greener pastures outside Thailand. “In the region, other growth areas are South Korea and Taiwan, since in other Southeast Asian countries the trend is to buy cheaper Chinese machines. Malaysian and Indonesian markets are price-sensitive. We cannot be competitive in markets that have this ‘mentality’ because German products are expensive,” according to Hofstetter, who takes care of the Southeast Asian markets.
Another European company that has positioned itself in Vietnam is Italian extrusion machinery specialist Amut. A second-time exhibitor at the Thai show, it maintains a technical service centre each in Thailand and Indonesia, and has operated an office in Vietnam for seven years.
“Currently, Vietnam is the best market in Southeast Asia, even overtaking the Indonesian market. Currency-wise, Vietnam is resilient, if compared to Indonesia and Malaysia and Thailand. The market is bolstered by a majority of investments from the likes of Japanese and South Korean companies that are shifting from China to Vietnam. Hence, we are pushing our machinery here,” said Andrea Peretto, Sales Area Engineer & Service Engineer of Amut.
He further said that Thailand seems to be inching off the growth grid. “The Thai market has a lot of potential, however investors are apprehensive about investing now that there is an uncertainty in the political situation,” he said.
Nonetheless, Peretto sees continued growth in many other sectors. “Rigid packaging, construction and automotive will continue to go up in Thailand. At the rate things are going, we need to seize the opportunities as they come and always hope for the best.”
Attractive market prospects in Thailand
Meanwhile, a Vietnamese company is seeking to corner a niche market in Thailand. Vietnam Lime, part of the Quang Ninh-headquartered Huong Hai Group, is a manufacturer of quicklime with technology from the G7 in limestone processing that improves plastics manufacturing with higher quality results.
According to Ngo Thanh Hai, Sales and Marketing Director, “We are a new company in Vietnam and at the moment, the only firm in Vietnam that can produce precipitated calcium carbonate (PCC) and nano-PCC. These products not only help to reduce the porosity in plastics like HDPE, but also generate high integrity surfaces to resist ageing and deterioration from natural elements in the environment.”
And for the company to meet the demands of customers for high quality calcium carbonate products Huong Hai has invested heavily in R&D for its Vietnam plants, according to Ngo. The effort has paid off, reflecting from the increasing production capacities.
“This year, our production capacity is 600 tonnes/day. By 2016, we are projecting to triple our production capacity,” says Ngo, adding that with a total reserve of 360 million tonnes of limestone, Huong Hai will continue to produce high quality calcium carbonate products at competitive pricing.
Not put off by the foggy economic climate in Thailand, Ngo said, “Whatever the situation in Thailand right now, we are looking at building up our market over the longer term. We have potential customers here and our competitors in Thailand also want to cooperate with us in terms of production, since our company has access to raw materials for the production of PCC and nanoPCC.”
He said that the company is also targeting markets involved in the ongoing Trans-Pacific Partnership (TPP), of which Thailand is also a part of.
“In the future we are looking at the possibility of going into joint ventures in the respective local markets.”
Meanwhile, the participation of Davis-Standard at the T-Plas indicates its intent to sink its teeth into the opportunities offered by the automotive industry, amongst others.
“Historically, our company has had a strong presence in converting systems in Southeast Asia, but we’re also engaged in serving the automotive segment. For instance, we specialise in providing solutions for hoses, and door and window seals,” remarked Gomez.
The prevailing declining automotive sales do not rub off the lustre of Thailand’s competence as Asia’s automotive hub.
Gomez opined, “More than a local market, Thailand exports a sizeable volume of automotive components and also assembles vehicles for export across the globe. As it is an important automotive hub within Southeast Asia, it will enhance its positioning and its economy is going to be a double playing field when the AEC comes.”
Certainly, Vietnam Lime and Davis-Standard’s participation at T-Plas indicates Thailand’s untarnished market strength, barring the current slack.
(PRA)Copyright (c) 2015 www.plasticsandrubberasia.com. All rights reserved.