The future of package printing lies in fast, flexible and smart technologies. Today’s manufacturers are striving to meet growing consumer demand for products tailored to the needs and preferences of different market segments split by region, gender, age and a multitude of demographics. As the mass manufacturing of one-size-fits-all products gives way to small, diverse batch production, companies must equip themselves with package printing technologies that maximise flexibility, speed and control.
For brand managers, this year’s Pack Expo International 2014 (Nov. 2-5, 2014; McCormick Place, Chicago, US) will offer an array of new technologies, enhancements and educational insights for package printing, labelling, and coding and marking. Co-located with Pharma Expo, a new show co-produced by PMMI, The Association for Packaging and Processing Technologies, and the International Society for Pharmaceutical Engineering (ISPE), the two shows will feature 2,000 exhibitors and attract roughly 50,000 attendees.
High-speed and flexibility
One of the biggest names in laser and continuous inkjet printing technologies Domino Amjet will exhibit new, high-speed equipment for beverage labelling.
“Manufacturers are demanding solutions for applications, like beverage labelling, that require high-speed and flexibility,” says Bill Bonaccorsi, Domino Amjet’s Director of Marketing. “A company needs the versatility to do a run of 12-oz bottles and then switch to different bottle sizes using the same line. Through our product evolution, we are able to do print runs at twice the speed of earlier technologies.”
Bonaccorsi adds that the company’s recent market additions have come with a more intuitive common interface that simplifies use and reduces training times.
Domino Amjet recently introduced the A520i continuous inkjet printer, which offers high speeds and a 316-stainless steel outer casing, designed for harsh production environments and washdowns for various food, beverage and dairy applications. It also has IP66 protection for dust and water. The company also plans to feature the new D-series laser iTech 15 scanhead, which Bonaccorsi says has the largest laser print area on the market. Also on exhibit will be the V230i thermal transfer overprinter, which requires no plant air and is designed for lower cost of ownership.
Digital revolution

Hewlett-Packard will demonstrate some of the new technologies from its digital printing portfolio, including Indigo and Scitex presses for labels, shrink sleeves and flexible packaging applications. The technologies are also suited to corrugated retail-ready packaging. HP recently launched its Indigo 20000 Digital Press for continuous-fed packaging applications, and Indigo 30000 Digital Press for sheet-fed packaging applications, which accommodate 30-in. wide film rolls, with up to 44-in. repeat length.
According to Simon Lewis, Director of Strategic Marketing for HP’s Indigo division, the new presses represent an “industrial revolution” for the package printing industry.
“This brings digital printing into areas that were previously analogue, and with this comes benefits such as reducing waste to nearly zero and speeding time-to-market,” he says. “Marketing campaigns can be far more nimble, and they can include regional variations. It moves us from mass production to mass customisation.”
“Retail-ready packaging, versioning due to SKU proliferation and localization, and shortened campaign durations pose significant challenges for traditional print,” says Ken VanHorn, Category Manager for HP Scitex. “Digital print technology with minimal make-ready time, substrate versatility and high quality makes it possible to not only produce profitable short runs and same-day prototyping, but also frees up capacity for longer runs more suitable for traditional printing presses.”
Customised integration
Also at the show, labelling equipment maker LabelPack Automation will be showcasing its integrated services for package printing as well as a new electric print-and-apply tamp label applicator. According to Robert Marasco, Vice-President of Sales, the new applicator can be used for sensitive applications with no air pressure. He says most printing systems require 80 psi of air or more for labelLing.
“We’re working with customers and our partners to develop printing solutions that run at four to five times the speed of standard digital printing, which allows our customers to be more competitive,” Marasco says. “These digital systems require no plate changes, and everything can be done ‘on the fly,’ from the copy to barcodes to variable imprinting.”
Remote control
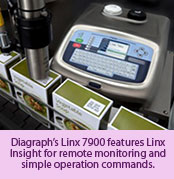
Package printing and labelling operations that can be remotely monitored enable faster troubleshooting, giving users 24/7 access to operations from a smart phone, tablet, or PC, offering the potential for greater control. To help lines run more efficiently, Diagraph, an ITW company, is offering the new Linx 7900 continuous inkjet (CIJ) printer with Linx Insight remote web control software to monitor production lines remotely and make commands to connected printers.
“Customers are demanding ease of use and connectivity in addition to best in class products,” says Chris Pangallo, Product Manager for Diagraph. “Linx Insight software allows you to download or upload messages from a PC to the Linx 7900, and even monitor it from your smart phone.”
In-mould labelling innovation
Nypro customises differentiated plastics packaging, from conceptualisation to design, for leading consumer product brands. Joe Stodola, Nypro’s Vice-President for Business Development, says many consumer brands are moving away from round and to differently-shaped packages that utilise in-mould labelling (IML) and some with special barrier protections. Dairy is one example, he notes, where there’s a move to non-round IML packaging.
Nypro’s Radius and internal development groups have worked with brand managers to engineer packaging, and Stodola says that a number of brand owners are leveraging decorative IML capabilities with high-end graphics to help brands stand out on the store shelf.
Nypro is developing another type of packaging that uses co-injection moulding technology to incorporate an EVOH-barrier package to protect the food or beverage while on shelf.
“This will extend the freshness of food products without a secondary bag seal, and it works better than standard propylene,” Stodola says. “Barrier packaging is nothing new, whether it’s glass or tin, but this is the first time we’re able to create barrier packaging in a high-volume, in a thinwall injection moulded format.”
For label and flexible packaging company Precision Press, laminated IML labels offer unique benefits of barrier properties, scratch-resistance, and FDA compliance for food contact. According to Tim Goserud, Director, Sales and Marketing for the company’s packaging division, there is a growing need for IML solutions developed with unique materials that offer specific barrier properties.
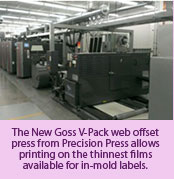
At the show, Precision Press will be discussing new in-house moulding prototyping technologies. Goserud says these new capabilities will offer proof of concept with minimal investment, helping brand managers get new IML packaging to market more quickly.
New serialisation and adhesives technology
For the global pharmaceutical industry, serialisation will continue to be a major line upgrade challenge for the coming years. Weiler Labeling Systems has developed two solutions for the high-speed printing of serialised codes on labels prior to application, including the SPS-200 print stand for existing labelling equipment, and the new X-4S labelling head for new WLS labelers.

At the show, WLS will be introducing the new RL-840N rotary labeller which utilises patented activatable adhesive technology developed by NuLabel Technologies. This labeller applies cut-and-stack labels that have a dry adhesive pre-coated onto the label. The labels are activated by a clean, water-based, glue-free spray just prior to application.
“This is done using our continuous-motion rotary platforms, and the technology eliminates the use of cold glue and the associated problems typically seen with cut and stack labellers,” says Philippe Maraval, Vice-President of Sales and Marketing. “It minimiSes the need for cleaning and reduces downtime. We feel that this technology will transform the cut-and-stack labelling approach in the future as users experience higher overall equipment effectiveness,” he added.
More information on Pack Expo 2014 is available here: packexpo.com
(PRA)