Also, download this story from the electronic issue here
Since the introduction of thermoplastic elastomers or TPEs in the 1950s, the materials have been continuously transforming. Today, TPEs cover more applications and uses, thus enabling the material to edge out polymers like PVC and rubbers.
New advanced materials replacing traditional ones are becoming the norm for industry sectors that lean towards continuous innovations. The medical, automotive, and consumer goods industries are just a few of the segments that leverage on innovation as demand increases and more applications emerge. As such, conventional thermoplastics and elastomers, for example, are being superseded by thermoplastic elastomers (TPEs).
Consulting firm Frost & Sullivan, in its US TPE market report, found that TPEs have become a viable replacement of thermoset rubber. Since TPEs are easier to process, allow greater design flexibility, and are easier to recycle, they are favoured over thermoset rubber as well as PVCs.
According to research conducted by Markets and Markets, the TPE sector is valued to reach US$23.9 billion by 2018, with the Asia Pacific region in the lead. The growth will be a result of the many advantages of TPEs, such as weather, chemical and oxidation resistance and delivering soft touch feel as well as the ability to cater to a diverse range of applications.
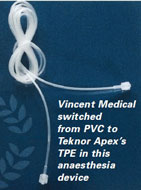
PVC substitutes
TPEs are currently taking over conventional materials, such as PVC, in a variety of applications, says another research company Visiongain.
A significant growth in the medical TPE market is expected in the coming years as demand for non-latex or PVC-free alternatives increases, says Visiongain. TPE, being cost effective, is also becoming a preferred option to silicones.
Meanwhile, Markets and Markets reveals that natural and synthetic rubber will see competition from TPEs owing to the latter’s ability to form various shapes and complex designs, adhering to many conventional and innovative processability techniques.
Moreover, as PVC use is weakened by findings that this material has hazardous chemical traces, TPEs environment-friendly reputation contributes largely to its growth.
US firm Teknor Apex, which also markets medical-grade PVC, supplied its Medalist MD-585 TPE compound in response to the decision of China-based OEM Vincent Medical to find an alternative to PVC for a gas sampling tube. The extruded item is a component of an anesthesia delivery and monitoring assembly through which the desired ratio of gases are sampled, measured, and delivered to the patient.
The challenge in making the switch was to match or exceed PVC performance in extrusion, assembly, and clinical handling, noted Otto To, General Manager of Vincent Medical. Teknor Apex says the switch from PVC to TPE posed a challenge to traditional methods of bonding tubing to connectors, for example, and it collaborated with Vincent Medical at its Dongguan plant to develop a connector solution.
The Medalist MD-585 compound is part of the MD-500 series of elastomers, which Teknor Apex developed to be the first fully practical alternative to PVC in medical tubing.
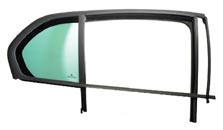
Catering to injection moulding
Italian elastomers producer Softer Group has introduced a TPE suited to extruding tubing for drinking water. Laprene 830.556 is plasticiser-free with high transparency and flexibility, the company says. Its smoothness and slippery surface help purge dirt and impurities that can be present in piped water. It also has antibacterial protection to inhibit growth of biofilms and bacteria.
Softer says the new product is available in an injection moulding grade that could be applied in the production of flexible tubes for appliances such as dishwashers and water dispensers, or in plumbing. The TPE adheres to PP for overmoulding uses.
Teknor Apex says that its new Sarlink ME-2600 series of styrenic thermoplastic elastomer (TPE-S) injection moulding compounds provides automotive manufacturers with processing and end-use properties that are superior to those of TPE-S materials currently used for window encapsulation.
The low specific gravities of 0.93 to 0.94, comparable to those of TPE-S grades now used in window encapsulation, are lower than those of PVC and EPDM, which typically exceed 1.10. Compared to the existing TPE-S materials, the new Sarlink ME-2600 compounds provide higher flow, enhanced surface appearance, improved tensile properties and stability upon heat ageing and UV exposure, adds the company.
Need for soft touch
The Visiongain study on TPEs also finds that various applications, including automotive parts and interiors, packaging, consumer & personal hygiene products, medical clothing, sports & leisure equipment, footwear, and baby care products, are requiring the “soft-touch” feature that TPEs can offer.
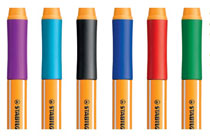
Stabilo writing utensils feature a non-slip gripping surface that is pleasant to the touch. They are manufactured from Thermolast K from Kraiburg TPE. Excellent adhesion to PP and other thermoplastics such as PC/ABS and the fast and easy two-component injection moulding manufacturing process are some of the properties of the materials.
US TPE producer Alliance Polymers & Services (APS) Elastomers also caters to applications requiring soft softtouch and ergonomic feel. The Michigan-based company has introduced a new Viprene P-Series of TPVs, said to be softer and more heat resistant, thus allowing for easy processing with reduced scrap rates.
PolyOne GLS Thermoplastic Elastomers recently worked with one of the largest infant care brands in Japan to develop a new a soft grip feeding set for infants and toddlers. It used its Versaflex TPE material in the bowl, cup and spoon, thus allowing the manufacturer to meet critical food contact regulations, both Japan’s Fatty Food Migration test and China’s Guobiao (GB) Standards test.
Consumer electronics – no fraud and no itch
Recent industry recalls and consumer concerns in the wearable electronics market have heightened the need for materials that do not cause irritation when in contact with the skin.
PolyOne says its latest Versaflex CE 3620 material meets the ISO 10993-10:2010 testing requirements with no signs of irritation. Several Versaflex CE materials have been used in wearable electronics applications without irritation for a number of years, and the recent ISO testing results underscore this track record, says the US firm. Key performance characteristics include: haptics, such as a silky smooth feel; strong chemical and UV light resistance for long-term durability; and vibration-damping qualities to enhance device performance and end-user comfort.
Meanwhile, the company has also introduced Versaflex CE with Percept Authentication Technologies, to help brand owners combat counterfeiting and reduce the risks associated with fraudulent goods such as phone cases, smart watches, headphones, earbuds and other wearable electronics.

According to Charles Page, PolyOne’s Director of Global Marketing, Percept’s anti-counterfeiting ability is combined with the haptics and durability of Versaflex CE TPEs. “In 2013, the US Department of Homeland Security logged US$145 million worth of counterfeit consumer electronics entering the country, and this material was developed to help counteract the trend,” he said.
Percept solutions, developed by PolyOne, enable brand owners to readily identify counterfeit products with easyto- use methods based on additives and unique identifiers called taggants.
Growth market in medical devices
More industrial companies are venturing into the medical devices market to take advantage of its higher growth. US speciality chemicals firm Lubrizol has branched into the medical device market by purchasing Wisconsin-based Vesta, a producer of catheters and tubing based on silicone and thermoplastics.
TPE manufacturers are likewise expanding capacity, in view of the growing medical and consumer markets. Elasto Sweden, a part of the Hexpol TPE production line, is gearing up for a new TPE line at its facility in Sweden. The company says the line, which is expected to come on stream in 2015, will have twin-screw technology, advanced raw material controls, supporting sub systems and analytics equipment. “This investment is part of our on-going commitment to supply leading quality TPE products and the highest levels of support to our growing medical customer base,” says the firm.
US-based Elastocon TPE Technologies, which already has more than five complete lines of speciality TPEs, has added two weighted high-density (HD) grades to its 8055 Series of TPEs for the medical devices sector. The easily colourable TPEs offer Shore A hardness of 55 (1.6 g/cc) and 65 (1.8.9 g/cc), depending on the grade selected.
(PRA)