Also, download this story from the electronic issue here
With a global population currently at about 7 billion and expected to expand to 11 billion by the middle of this century, we are going to have a lot of mouths to feed. Hence, there is an urgent need to focus on zero wastage of food. Borouge, provider of polyolefin solutions, is addressing the food challenge through its innovative solutions that are able to reduce food loss and water wastage and improve farming productivity.
According to the Food and Agriculture Organisation of the United Nations (FAO), the world must close a 70% “food gap” between the amount of food produced today (based on crop calories) and that most likely needed by midcentury.
Already today there is unnecessary wastage and significant shortage of food and we need to address these challenges with a sense of urgency if we want to ensure there is sufficient food for the generations to come.
At the same time, agriculture faces challenges due to changing economic and environmental trends including climate change, biofuel expansion, slowing agricultural yields, rising meat demand and ever increasing calorie intake from a growing global middle class. It is estimated that by 2050, about 70% of the global population will be urban, compared to 50% today.
The rapid urbanisation of society away from farms and agricultural heartlands means that we require increased appreciation for the value of food and effective food chain management systems to ensure that food is efficiently transported from where it is grown and produced to where it is consumed, with a focus on zero waste.

Wasted food
The FAO estimates that well over 32% of all food produced in the world was lost or wasted in 2009, based on weight. In developing countries this is as high as 50%. When converted into calories, global food loss and waste amounts to approximately 24% of all food produced, which means that one out of every four food calories intended for human consumption is ultimately lost.
This significant unnecessary wastage is taking place at various stages of the food chain, from the farm to the kitchen table, and needs to be addressed through improved farming techniques, innovative advanced packaging solutions and increased public awareness.
Poor human behaviour as well as the trend towards supermarket bulk-buying in developed societies contribute to an increase of waste, and this post-consumer wasted food, which mainly makes its way to landfills, contributes significantly to greenhouse gas emissions.
Governments should be encouraged to develop food loss and waste measurement protocols and set food loss and waste reduction targets. For example, the European Union has announced a target of reducing food loss and waste by 50% by 2050.
A great deal of food loss in developing countries happens “close to the farm,” so in addition to consumer, retail and supply chain changes, we also need to work hard at researching and implementing actions that minimise post-harvest losses.

Impact of food farming
One of the unseen challenges related to food production and availability in the future is the environmental impact of modern-day agriculture.
Today, we use roughly one-half of the planet’s vegetated land to grow food. The amount of land used for agriculture has grown by more than 10 million ha/year since the 1960s, and expanding croplands and pasture lands are placing increasing pressure on tropical forests, particularly in countries in South America and Southeast Asia.
Agriculture with its hunger for fertilisers now accounts for nearly one-quarter of global greenhouse gas emissions and 70% of all freshwater usage. Failure to address these environmental impacts will hamper food production in the coming decades, through land degradation, water shortages, and adverse effects from climate change.
Meanwhile the livelihood of some 2 billion people, approximately 28% of the world’s population (mostly from the poorest classes), is at risk and sustainable solutions that address the environment as well as societal needs must be optimised.
Food for fuel
There are schools of investors that promote the use of farmlands for the production of biofuels and biomaterials to replace fossil fuels for energy. These goals, while admirable, will have a damning effect on land for food.
Producing 10% of all transport fuels from biofuels by 2050, as planned by some governments, would require some 32% of the total global crop production while only producing 2% of global energy requirements, and increasing the “food gap” by roughly 100%.
Conversely, eliminating the use of crop-based biofuels for transportation would close the “food gap” by roughly 14%.
A major global challenge
Governments and industry need to work hand in hand to address the impact of modern agriculture, changing diets due to urbanisation, food wastage, food for biofuels and other materials, and the cost of food for the poor.
We have one planet with increasing demands on it to support human existence. In addition to access to clean water and proper sanitation, there is nothing that is so important to maintain the personal dignity and health of people and contribute to social, economic and political stability around the world.
Innovative plastics solutions
Borouge and the plastics industry contribute to addressing the food challenge by reducing the loss of food and wastage throughout the food chain, reducing water wastage and improving farming productivity. Sustainable recyclable, flexible and rigid packaging solutions protect food over long distances for longer periods of time.
Plastic packaging is extremely light and contributes to reducing greenhouse gases throughout the food supply chain. Rigid plastic containers improve storage methods, especially close to farms, avoid pests, spoilage, and transportation damage, and are proven to prevent food damage significantly compared to other materials such as hessian sacks.
Plastic film greenhouses increase crop yield and quality thereby improving crop efficiency and farmer’s profitability, while plastic pipe drip-irrigation systems in plantations provide up to 75% water savings versus flood irrigation, and even better results when used within plastic film greenhouses.
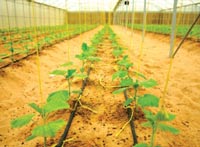
Examples of value-creating, differentiated polyolefin solutions:
- Catching the light! Delivering water efficiency!
Sunlight and water are two of the most important natural resources for a food producer. The agricultural industry may seem to be in decline amidst the rapid urbanisation, but the opposite should be the case. In fact, the global agricultural output must double in the next 20 to 30 years to sustain the expected growth of the world’s population.
Borstar polyethylene (PE) has proven to be exceptional in several agricultural film applications, such as greenhouse tunnels, mulching and silage. For greenhouse films, the matte surface of Borstar enhanced PE prevents crop damage and scatters the light to enhance the yield and quality. Typically 25% higher speeds of growth, from planting to start harvesting, are observed. The unique properties of the Borstar technology keep the film in shape and durable, even in tough weather conditions.
New technologies for precision agriculture help growers and farmers to do more with less. Conventional crop irrigation methods use high volumes of water, a large part of which is often wasted through over-watering, excessive infiltration, run-off or evaporation.
Of the more recent systems developed to improve crop watering, drip irrigation offers the greatest potential in terms of water efficiency and crop yield. Drip irrigation eliminates water wastage by providing a continuous and controllable flow of water droplets, through a series of pipes and drippers, directly to or adjacent to the root zone of each plant or drip row. This precision method significantly reduces the burden on water resources and can also aid substantial improvement in crop yield. Borouge has introduced Borstar Aquility, a family of products intended for drip irrigation applications. Its introduction underlines the important role of modern irrigation systems in conserving water and increasing crop yields, two crucial factors in addressing the global challenges of water shortage and rising food demand. - Lightweight plastics preventing waste and contamination
Borouge’s innovative plastics solutions utilise proprietary technologies such as Borstar and Borstar Nucleation Technology (BNT) to deliver unique property profiles. They provide solutions with economical processing, weight saving potential and enhanced and differentiated properties that focus on applications that benefit from such high performance PE and polypropylene (PP) polymers in plastic film, fibre and moulded products. - Transporting bulk material with Heavy Duty Shipping
Bags
Borstar FB2230/FB2310 offer environmental and economic benefits with 20%-30% downgauging potential resulting in reducing the thickness of 25 kg Heavy Duty Shipping Bags down to 130 microns. Adding it to the formulation has given the film a better bubble stability and film stiffness, with a lower Oxygen Transmission Rate (OTR) and Water Vapour Transmission rate (WVTR).

Polyolefins for advanced flexible packaging
Borouge provides the food value chain with a portfolio of plastics packaging solutions, meeting the international standards of quality and durability for all food and beverage packaging applications.
High performance Borstar-enhanced PE and PP plastics solutions are sustainable alternatives to glass, metal and paper for the entire food value chain processing and packaging industry.

Borouge’s solutions enable packaging suppliers to better manage storage logistics, facilitate transportation and minimise breakage, spillage and spoilage of food – the causes of food waste.
The innovative solutions for advanced food packaging are recognised for their durability, high impact resistance and their capability to protect, thus ensuring the integrity and shelf life of the packed food without compromising its taste, odour or freshness.
Think thin
The trend in flexible packaging film is moving towards multi-layer co-extrusion film structures with enhanced properties and performance features. Flexible packaging converters are continuously sourcing for raw materials that give the best cost/performance balance in order to maintain their market competitiveness.
"Inferior shrink packaging can be damaging not only to goods but also to profit and brand reputation," said Shawn Khoo, Application Marketing Manager, Borouge. "Flimsy shrink film that tears apart and spills its contents doesn't just annoy consumers — it could affect a store's bottom line. No one likes to buy dented canned food or drinks."
Among Borouge's solutions to this challenge is its Borstar range of bimodal polyolefin resins (such as Borstar FB2310 and FB1350), which are said to provide superior characteristics versus unimodal resins found in many collation shrink applications. “They allow converters,“ says Shawn Khoo, “to produce thin-gauge films that are strong and reliable.“
It is vital to balance the quality, cost and performance of collation shrink packaging. As the largest collation shrink film converter in South China, Zhengxin Packaging knows this only too well. It can count beverage giants Pepsi-Cola, Coca-Cola and Master Kong among its customers.
The company used Borstar technology to downgauge its collation shrink films by around 20%.
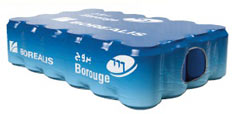
"I believe that we can build up a three-party partnership among brand owners, Zhengxin Packaging and Borouge in the near future," said Bill Huang, President of Zhengxin Packaging.
"Borstar bimodal high crystallinity homo cast polypropylene HD915CF is a cast extrusion PP with 50% higher Flexural Modulus (stiffness) compared to ordinary homopolymer CPP," said Wei Ming Tan, Applications Marketing Manager, Borouge.

"Most importantly, it allows for the downgauging of the overall packaging film structure, often by as much as 30%. These features align well with current downstream packaging film demands on sustainability and pricing focus through optimum cost/performance balances."
High crystalline homo PP is recommended for the core layer of vacuum metallisable cast polypropylene (VMCPP) film applications.
In lamination CPP film, high crystalline homo PP can be applied in either the core or skin layer for co-extrusion with copolymer resin. The combination of excellent mechanical and barrier performance provides new opportunities in FFS (Form-Fill-Seal) packaging. Traditionally, cast PP film will be laminated with BOPP film in secondary processing for higher film stiffness or improved barrier properties. High crystalline homo PP co-extrusion film allows converters to achieve production cost savings as no BOPP lamination step is necessary.
In this area, Borouge's homo PP HD915CF, which is produced using the Borstar BNT, is claimed to optimise the morphology of PP.
Polyolefins for advanced rigid packaging
The increased demands on hygiene, safety and convenience, coupled with changing lifestyles and stringent industry regulations, mean that today more emphasis is placed on quality packaging materials than ever before. This is where Borouge brings value to the industry by offering a wide range of high quality PP and PE grades for injection moulding, blow moulding, ISBM and thermoforming that deliver both quality and performance.
One of the most significant and award-winning packaging solutions from Borouge is RG468MO, a PP random copolymer that is developed with BNT. This high-flow resin boosts 20% productivity gain for the rigid packaging converting industry and achieves shorter cycle times and higher mechanical performance. It also ensures clear transparency and pleasing visual aesthetics required in the packaging value chain. RG468MO imparts no taste or odour, and complies with all food contact regulations.
The grade was crowned in 2012 with the Green Material Award for Innovation Application in China, in recognition of its contribution to the development of the packaging industry.

Borouge RG468MO PP contributes to sustainability in the packaging value chain through reducing material usage, offering production energy savings of up to 10% and a consequent reduction of CO2 emissions. It broadens design freedom by allowing complex design and facilitating improved processing and enhanced economics for the benefits to converters, brand owners and consumers.
Collaborative action needed
In addition to providing value-creating, differentiated solutions, the plastic industry collaborates with the food value chain to minimise waste at farms, during factory processes and the supply chain, and enhances the sharing of best practices, inspiring action and effective collaboration.
There is a need to accelerate initiatives that bring increased awareness to the food challenge and food wastage particularly in developing societies.
Consumer awareness campaigns should reveal how much food society wastes unnecessarily at restaurants, hotels, receptions and supermarkets, and supported by proactive regulation to promote simple and effective solutions.

Awareness of wastage in the home also needs to be brought to the public, as everyone can positively affect the environment in this area. An enormous amount of energy and water used to produce and deliver the food is also being wasted and therefore the concept of zero food waste addresses several major challenges the world faces today.
(PRA)