Also, download this story from the electronic issue here

Sometimes environmental sustainability and business don’t always go hand in hand, especially when it comes to packaging of products. But multi-national companies hoping to woo sustainability-minded customers are beginning to make a concerted effort in building more sustainable businesses and reducing their environmental footprints.
Unilever and DPS using less plastic
One of the world’s leading suppliers of food, home and personal care products Unilever has introduced a bottle that contains at a minimum 15% less plastic as a result of a newly developed packaging technology. The Dove Body Wash bottles are produced using the MuCell technology for extrusion blow moulding (EBM), which was created in close collaboration with two of Unilever’s global packaging suppliers, ALPLA and MuCell Extrusion.
It represents a breakthrough in bottle technology: by using gas-injection to create gas bubbles in the middle layer of the bottle wall, it reduces the density of the bottle and the amount of plastic required.
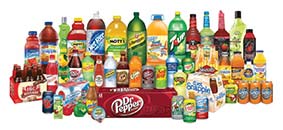
Unilever says it intends to widen the availability of this technology to be used more broadly across the industry.
With up to 33 million Dove Body Wash bottles sold across Europe in 2013, the new technology stands to save up to 275 tonnes/ year of plastic; whereas a full roll-out across every Unilever product and packaging format could save up to 27,000 tonnes of plastic and contribute significantly to the target set out in the Unilever Sustainable Living Plan to halve its waste footprint by 2020.
Unilever says it will waive specific exclusivity rights by January 2015 so that other manufacturers can start to use the technology across their brands and products.
In its recent environmental report, Unilever says its total footprint from packaging waste to landfill has reduced (-11%) as a result of efficient packaging designs and the disposal of sauce brands with large waste footprints. All packaging with this technology will remain 100% recyclable.
Meanwhile, in its 2014 Corporate Social Responsibility Report, US beverage maker Dr Pepper Snapple Group (DPS) says that it conserved around 28,000 tonnes of PET through lightweighting and packaging redesigns since 2007 (the company says it offers the lightest 2-l bottle in the industry) — the goal was 28,000 tonnes by 2015.
The report also says since DPS achieved its original goal of an 80% packaging recycling rate in 2011, it has revised its goal to achieve a 90% recycling rate of its solid manufacturing waste by 2015.
Retailers in the UK to push for recycling
In the UK, Sainsbury's and Marks and Spencer (M&S) are leading a consortium of organisations from the UK packaging, retail and recycling industries to launch a market trial aimed at recycling as much as 1.3 billion plastic food trays each year.
The campaign focuses on reducing waste from black CPET trays, which are commonly used in supermarket ready meals. The trays are recyclable, but the black colour of the trays makes them undetectable with Near Infra- Red optical sorting equipment used at plastic sorting and recycling facilities.
To address this, resource efficiency group WRAP has worked with industry experts (like packaging manufacturer Faerch Plast) to develop a new type of black CPET tray, which sorting trials have shown can be detected and separated for recycling. Market trials have commenced with 2 million new trays being rolled out across the M&S and Sainsbury's ready meals range -- these will examine sorting efficiency and carbon footprint reduction.

Waste collector Biffa Waste Management will take a lead in using detection technology reprogrammed to sort the trays and plastic recycling expert Nextek will assist with the automatic sorting, as well as supervising the recycling and decontamination of the material. Then Faerch Plast will get involved again with assessing the recycled material to see if it can be manufactured back into black CPET trays.
The project team consists of WRAP, M&S, Sainsbury’s, Faerch Plast, the Kent Resource Partnership, Biffa, Recoup (RECycling Of Used Plastics Limited), and Nextek.
The effort comes as part of WRAP’s mission to reduce overall waste in the UK. Last year, WRAP found that UK households wasted US$11 billion worth of food and drink, or 7% of overall sales, with the grocery retail supply chain producing roughly 6.5 million tonnes of annual waste. Of this, 3.9 million tonnes was derived from food and drink manufacturers, with the majority being food.
A separate 2013 WRAP study analysed 50 grocery products with the biggest environmental impact and found that together they contribute between 21 and 33% of household greenhouse gas (GHG) emissions. Some of the products include such staples as bread, potatoes, bananas and milk. This compelled companies such as the Co-operative Group, Nestlé and Sainsbury’s to commit to improving the sustainability performance of some of their products.
Expanding biobased thermoformed packaging
Elsewhere, a research project to develop a new biobased thermoformable barrier coating solution for the packaging sector, known as ThermoWhey, has been launched in Europe. This 28-month R&D project is funded by EC’s Seventh Framework Programme (under the Manunet programme) and will deliver whey protein coating with improved thermoformability independently from storage time while maintaining excellent barrier properties to produce packaging for food, pharmaceutical and cosmetic applications.
Thermoforming is one of a dominant and growing technology in the packaging market and although biobased trays have existed on the market for years, they do not meet the barrier properties required for sensitive food products that the ThermoWhey product will have.
Overall, biobased plastics still represent a niche but, thanks to technical innovations and with a 25% annual growth, have increasing potential to replace synthetic counterparts. In contrast with certain controversial biopolymers that compete with food resources, ThermoWhey will represent a unique market offering that is derived from agrofood by-product, and that delivers sufficient barrier properties for products packed in modified atmosphere (MAP).
The project by Spanish research institute IRIS will develop a complete set up of the manufacturing capacity and optimised process for Whey powder (WPC), agglomeration process for whey protein-based barrier coatings as well as of a coating process for films, and manufacturing of thermoformed packaging (blisters and trays).
To improve the long-term thermoformability of whey protein-coated packaging, ThermoWhey will perform different modifications of the whey proteins, derived formulations as well as study any influence on subsequent stages of the process.
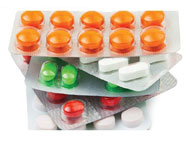
Besides IRIS, the consortium includes German manufacturer of thermoforming tools Geba, German cheese and whey producer MLANG; Spanish manufacturer of thermoformed packaging (blisters and trays) Serviplast and German research institute Fraunhofer.
Previously, the researchers worked on Wheylayer, a patented whey-based technology that is currently on the fast track to commercialisation and is capable of replacing expensive synthetic oxygen barrier layers, such as EVOH, currently used in food packaging.
(PRA)