EPS Panels: Closing the gap in much needed housing
Also, download this story from the electronic issue here
Billions of people across the globe are either homeless or living in sub-standard housing due to rising construction and material costs. With Airpop, aka EPS, affordability may soon be a reality to close the low-cost housing gap.
Housing, a basic human need, is not merely a structure with a roof and walls but one that is decent, safe, and affordable. In many areas, this criterion for housing is not met. UK’s Habitat for Humanity cited a 2005 finding that globally about 1.6 billion people lived in sub-standard housing, while 100 million people, who mostly migrated to urban areas, were homeless.
In the McKinsey Global Institute (MGI) 2014 report, A Blueprint for Addressing the Global Affordable Housing Challenge, affordability is highlighted as a deterrent for access to housing. It is defined as “the difference between the cost of an acceptable standard housing unit (which varies by location) and what households can afford to pay using no more than 30% of income”.
The report suggests that the disparity in cost to affordability and the rate of urbanisation could force some 440 million urban households to contend with substandard housing by 2025. Globally, the affordable housing gap, pegged at US$650 billion/year at the time of the study, would affect one in every three urban dwellers to total 1.6 billion people. It would require spending on construction of homes to as much as US$11 trillion to address the housing shortage by 2025, MGI reported.
Meanwhile, reducing housing costs by as much as 50% lies on four key areas, namely, financing, land, construction, and operations and maintenance. Lowering construction costs (and completion time) could come about by using prefabricated components and engineering materials.
Cost-effective alternative material
Costs for traditional construction materials such as bricks, steel, concrete, and wood have all gone up. This has spurred new concepts to make use of materials that can provide the durability and strength needed for a decent, safe home.
Regarded as an environmental nuisance, the usefulness of polyurethane (PU), polystyrene (PS) and expanded polystyrene (EPS), are eclipsed by the controversy surrounding these plastic-derived foam materials.
Of the three, EPS is much lighter and of late has broadened its applications in key industries. A rigid cellular plastic with good thermal insulation and high impact resistance, EPS is utilised for building affordable yet sustainable housing.
A 2014 study published in Kenya’s University of Nairobi, Department of Civil & Construction Engineering, says that EPS as an alternative housing material has offered a low-cost viable solution for the housing deficit in the East African country of more than 44 million people.
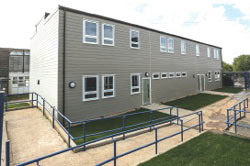
The case study evaluated EPS panels from Nairobi-based National Housing and Corporation (NHC), and found them to “have minimal compressive and flexural strength, hence mainly acting as a filler material in the structural system, offering high bending stiffness for low density members”. As for the cost, the study found that building with EPS technology was more expensive than using quarried stones. However, labour costs for the conventional method involving masonry work was found to be higher than when EPS technology was used.
Rebranding EPS; with benefits
Giving EPS a new, catchy name seems to be a novel idea, especially when housing shortages are imminent. Now known as Airpop in Europe, the new name attempts to describe what EPS is made up of, that is 98% air and only 2% synthetic material.
Airpop has a serious side to it too. Firstly, it embraces EPS’s light weight, rigidity, insulation, high acoustic performance and good fire protection. EPS is also a sustainable product that is recyclable (can be recycled up to seven times without deteriorating) and environmentally sound.
The British Plastics Federation (BPF) also points out that Airpop is non-toxic, chemically inert, nonirritant and rot-proof. Fungi and bacteria cannot grow on Airpop as it is insoluble and non-hygroscopic – and moisture contact will not lead to product or performance deterioration.
New system enhanced by EPS
Meanwhile, Airpop is seen to be a potential solution to address the low-cost housing gap. An innovative modular building system hatched by AcerMetric, a British applied engineering design and development firm, the Acermetric building system incorporates Airpop at the centre of its design.
The Acermetric system is patent-protected in 20 countries worldwide with another 40 countries recognising patent conformance. It comprises a range of interlocking panels each of which is effectively a sandwich of grey EPS with the option of the outer board material specified according to the building needs.
Together with window and door cassettes, the full range of elements extends to around 40 shape options which, when locked together and linked to patented roof support beams and columns, allow more than a million combinations of high-strength, three-dimensionally stable structures – a ‘Lego-like’ system capable of creating a building of virtually any shape, size or design.
According to the company’s calculations, the system could easily accommodate buildings up to ten storeys high, is suited to areas prone to ground movement and even to earthquake risk, and has undergone stringent UKAS testing covering strength, fire resistance, acoustic protection, thermal insulation and longevity.
In its most recent project, the Acermetric building system has lowered costs and build-time at a London primary school where a two-storey multi-purpose 466 sq m “Centre of Excellence” was assembled. It took four builders around 13 weeks on-site to lift panels by hand and install the elements with a single tool.
AcerMetric’s Founder, engineering design and R&D veteran David Appleford, said that his system owes a great deal to EPS, which forms the core of the panels.
“The grey EPS at the heart of our Acermetric panels gives us many advantages. In fact, thermal insulation is so effective that in the primary school project – the combination of the heat generated by the occupants and high solar gain meant we had to install additional cooling measures,” he said. The thermal performance for grey EPS/Airpop is 0.03 W/mK and, according to Appleford, this helps his Acermetric buildings to achieve 0.1 u-values or better.
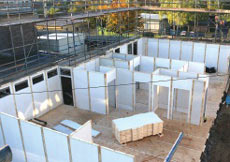
Material of future homes in developing countries
Appleford, convinced the Acermetric system could bring major benefits across the globe, said, “Our success so far allows us to be confident that if we could move to large-scale precision mass production of the panels we would have no problem in plugging the gap of 150,000 low-cost homes desperately needed across the UK. Then we could look at the potential in developing countries – this could represent a massive solution to a global problem in which EPS could play a significant part.”
Other advantages of the Acermetric system include the fact that no expansion joints are needed as the entire construction is post-tensioned through the locking mechanism. All internal walls are pre-finished - avoiding the need for plasterboard - and external walls can be finished to any specification including architectural cladding, weatherboard, slate, tile or brick slips.
David Emes, Chairman of the BPF EPS Group, commented, “There are many building systems which take advantage of Airpop but this is one of the most innovative we have come across. It’s an ideal building material for modular or elemental systems because it can easily be cut or moulded to shape during the manufacturing of the elements and has built-in BBA Approval, BRE Certification, BRE Green Guide A+ rating and many wider industry accreditations. It also comes closest of any modern building material to fulfilling the 60-year performance life target set by the UK Building Regulations.”
A new residential build project for Acermetric is in the pipeline to further prove the system’s integrity. The company says the next step will then be to commission a factory for the mass production of the panels and to license the simple technology to manufacturers, builders and construction companies in the UK and beyond.
(PRA)Copyright (c) 2015 www.plasticsandrubberasia.com. All rights reserved.