Also, download this story from the electronic issue here
Highlighted in this report are an initiative to put to rest the oxo debate; sustainable technology to create chemicals using photosynthesis; and partnerships to create biobased plastics.
Putting to rest the oxo debate
Biodegradable plastics (made from renewable resources such as PLA, PHA and TPS or from petroleum such as PBAT, PBS) can offer benefits for certain applications. Such applications can be in agriculture (mulch film), household (biowaste collection bags) and much more. Whether such biodegradable plastics are a solution against littering is a different discussion.
However, there is a big discussion going on worldwide about so-called oxo-degradable plastics. These products are traditional (non-degradable) plastics such as PE, PP and PET, mixed with a small percentage of an additive. Companies bringing such products to market claim that they are biodegradable, although not everyone agrees.
Currently the European Commission is considering a possible ban on oxo-degradable carrier bags. Also in France, a group of MPs in the French National Assembly has called for a similar ban. Predictably, the oxodegradable plastics industry has reacted furiously.
Experts complain about missing scientifically based evidence from neutral, independent laboratories or certification bodies. As long as such evidence is missing, critics doubt the complete biodegradation and call these products oxo-fragmentable.
Now OWS (Organic Waste Systems, Gent, Belgium) and IKT (Institute of Polymer Technology, University Stuttgart, Germany) are planning a multi-client study on the oxo-degradable plastics. Building on a desk research by OWS for Plastics Europe (2013), a comprehensive laboratory testing programme is planned. The laboratory tests shall ultimately proof or disproof if such products are biodegradable or not.
In a first phase, a number of oxo-degradable plastic products available in the market will be abiotically treated. In a second phase, the fragmented parts will be used for further biodegradation testing according to internationally accepted ISO and ASTM standards. The contribution for this study is estimated at EUR10,000 to 20,000 per partner, depending on the number of interested companies. The partners are aiming at a broad participation including government agencies, consumer goods producers, NGO’s, oxo-degradable producers and the bioplastics industry.
Power of the sun to create chemicals
AkzoNobel and cleantech company Photanol have teamed up to develop a process for harnessing the power of the sun to make chemicals. The two companies will work on creating sustainable technology that mimics the way plants use photosynthesis. The aim is to produce "green" chemical building blocks that will eventually replace raw materials AkzoNobel currently obtains from fossil-based production.
The collaboration is focused on Photanol's existing proprietary technology, which uses light to directly convert CO2 from the air into predetermined raw materials such as acetic acid and butanol. The only by-product is oxygen. The two companies will start by developing a number of specific chemicals that are currently used by AkzoNobel's Specialty Chemicals Business Area. The partnership is intended to be a stepping stone for potential commercial production of fourth generation biobased chemicals.
Carbon fibre from biomass
The US Department of Energy (DOE) has given out a funding of US$5.9 million for development of biobased carbon fibres to the Southern Research Institute (SRI). The DOE award will fund development of a multi-step catalytic process for conversion of sugars from nonfood biomass to acrylonitrile – a key precursor in the production of carbon fibre.
Industrial demand for carbon fibre continues to grow due to its high strength and light weight in a number of fields including defense, space, aviation, automotive, wind turbine production, and sporting goods manufacturing. SRI is exploring novel methods of producing acrylonitrile and other biobased chemicals and fuels using renewable, non-food-based biomass feedstocks.
Team members included in SRI’s original application to DOE are Cytec Carbon Fibers LLC and New Jersey Institute of Technology (NJIT). The biobased acrylonitrile produced by SRI’s process will be validated by Cytec, a major carbon fibre manufacturer, and compared with petroleum-based acrylonitrile as a potential direct substitute. NJIT will assist with catalyst characterisation for optimising catalyst performance.
Furthermore, the National Renewable Energy Laboratory (NREL), which is the DOE’s primary national laboratory for renewable energy and energy efficiency R&D, will also receive funding to investigate and optimise multiple pathways to bio-acrylonitrile.
Other recipients of the DOE funding to develop lowcost carbon fibre process include Dow Chemical, Oak Ridge National Laboratory (ORNL) and vehicle maker Ford Motor. ORNL has also been exploring the use of lignin extracted as a by-product of cellulosic ethanol fuel production as a raw material for carbon fibre production.
Partnerships to launch biomaterials
UK-based paper and technical fibres manufacturer James Cropper has joined forces with Swedish forestry giant Södra to establish the degradable DuraPulp paper product that is said to be able to carry the weight of an adult and be composted within 100 days.

The bio-composite material is targeted at the premium products market, such as luxury fashion, cosmetics, automotive and interior design sectors.
The material is a blend of wood fibres and renewable, non-fossil based biopolymer (including recycled plastics and paper products) that can be heat pressed to take on any rigid form, or used as a sheet where there is a requirement for high tearing and bend tolerance or air permeability. Unlike other composite products, DuraPulp is believed to be the only one available where the primary content is pulp fibre and draws on 100% renewable resources, while remaining completely biodegradable.
Initially a result of research by the Swedish scientific research institute, Innventia, Södra has explored DuraPulp’s adaptability in a series of design-led commissions, including a paper-thin, waterproof chair; moulded packaging to cradle delicate objects in transit; and an electric desk lamp. Its biodegradability has been embraced as a feature, being made into a seed pod from which plants will grow after the fibre has degraded.
Elsewhere, Croatia-based packaging producer EcoCortec has developed the EcoOcean biobased film and bags that are designed for use by the marine market. The film and bags contain 77% content of biobased PHA material and are designed to biodegrade in marine environments, anaerobic digestion, natural soil and water environments, backyard composting systems, and municipal composting facilities (in areas where these facilities are available).
Although the firm says it does not promote marine disposal (but says the films were developed to fight the increasing problem of marine debris), in the event that its product should reach the waterways, it will “biodegrade in months instead of remaining in the ocean for hundreds of years like ordinary plastic films.” EcoOcean can help reduce the increasing and persistent problem of marine litter, adds the firm.
It also says that EcoOcean is heat, moisture, and chemical resistant making it an ideal film for compostable bags and many flexible film packaging applications.
The firm has also launched its EUR3 million phase three expansion of its Beli Manastir, Croatia plant, to double its manufacturing and warehousing capacities. EcoCortec also specialises in manufacturing US-based Cortec Corporation’s Vapor phase Corrosion Inhibitor (VpCI) films.
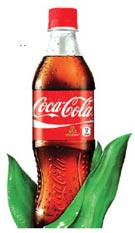
Some of the targeted markets for the marine degradable packaging are cruise liners, hotels and resorts in the coastal areas of Europe as well as ecologically sensitive regions along rivers and lakes.
Meanwhile, US bioplastics maker Virent is expanding its operat ions as a result of an additional investment by beverage maker Coca-Cola in the company’s development and commercial isat ion of its biobased paraxylene, BioFormPX. This investment will enable Virent to scale up separation and purification of BioFormPX material at its demonstration plant in Madison.
Virent says it is advancing on a path to a full-scale commercial solution for Coca-Cola’s 100% plant-based PET plastic bottle known as PlantBottle.
Virent and Coca-Cola have been working together since 2011, when they first announced a joint agreement on the development of bio-based PX technology.
Virent says it has progressed its PX technology to commercial readiness, improved the process economics and produced biobased PX, which has been converted by Coca-Cola into 100% biobased PET bottles. This new investment will allow production of larger quantities of BioFormPX material.
Virent has also run its demonstration system to fulfill a number of fuel and chemical orders since it started operations in 2010. This added capability to produce larger quantities of purified PX will be combined with additional system enhancements to increase production capabilities, including larger volumes of bio-fuel and other biomaterials.
Virent is one of three bioplastics materials companies targeted by Coca-Cola and includes Dutch firm Avantium Research and Technology that is using its YXY chemical technology to make a new biobased plastic known as PEF; as well as US firm Gevo that is producing a 100%-renewable isobutanol, a paraxylene building block.
Coca-Cola is working with the firms to speed up development of its PlantBottle and reach its goal of doubling its usage of bioplastic bottles to 3 billion by 2020.
(PRA)