The triennially-held K2013 exhibition will be staged from 16-23 October in Düsseldorf, Germany. With the Germans (having booked 43% of the overall exhibition area of 170,000 sq m) making up a strong contingent in their home country, some of the highlights to be expected at the exhibition are showcased here.
Materials companies raise the bar
Frankfurt-headquartered Topas Advanced Polymers, a joint venture of Daicel Corporation and Polyplastics, both of Japan that operates the world’s largest cyclic olefin copolymer (COC) plant in Oberhausen, will showcase new grades with HDT nearing 200°C. The clarity and heat resistance of COC is driving use in touch screen and light distribution components of mobile devices while its fluoropolymer-like electrical properties are used to mould antennas. For the healthcare and packaging sectors, Topas will introduce the 7010F-600 film extrusion COC with heat stability and robust extrusion performance. It features a HDT of 100°C for multilayer food packaging in hot fill conditions.
PMMA maker Evonik Industries will exhibit solutions for residential and urban construction, mobility and lifestyle. It will have a customised electro-powered Rinspeed microMax concept car at its booth. It is made of Plexiglas, making it 40-50% lighter than conventional glazing while the Tegomer anti-scratch additive prevents scratching in the interior. For greenhouse films, Evonik offers Sipernat 820A while the new, phthalate-free Elatur CH plasticiser is suitable for sensitive PVC applications.
TPU specialist Huntsman will highlight materials for the wire and cable industry like Irogran A95 P 5003 that combines the mechanical benefits of TPU with fire retardancy. It is ideal for use in confined spaces where cables need to be tightly bunched together or where ventilation may be poor.
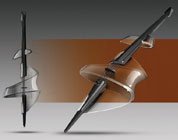
Meanwhile, Bayer MaterialScience and its partners have developed a prototype interactive cello. The body is made of a crystal-clear cast aliphatic PU resin that can easily be moulded into the desired shape. Shortly before casting, the PU is prepared from two liquid, solvent-free components from the company’s Desmodur and Desmophen product lines. Depending on the components selected, the materials can be adapted to the specific requirements in terms of hardness and flexibility. All the technical components required for sound and visualisation are integrated into the neck and fingerboard. A tuning device or surfaces for video jockeying (VJing) can also be installed in the instrument. Bayer MaterialScience's Bayblend PC is already used for making the body and keys of saxophones while the Baydur rigid PU integral skin foam is used in pianos. Corresponding instruments made of transparent Makrolon PC will be introduced to the market soon.
Electric blow moulding machines move up a notch
Uniloy Milacron will be showing the UMS 20E.S all-electric blow moulding machine. It has an accessible clamp system fitted with a direct actuator drive transferring the force simultaneously via two rugged, deflection-free swivel joint arms onto both mould platens into the centre of the pinch-off areas. Once the mould is closed, no power is used. It is also fitted with an integrated post cooling station and flash separation including the handle flash, PWDS system and closed-loop controls for all machine movements. During the show, the machine will be producing 12 l stackable UN containers including a view stripe in a single-cavity mould. It claims power savings of up to 40%, in comparison to hydraulic machines. Additional accessories such as a Delta quality centre, including leak testing and weight control as well as an Eisbär blow air cooling system, are part of the full line set-up.
Following the introduction of Bekum’s patented C-frame clamping unit (used on the 07 series of machines) at the last K show, it will present the Eblow 407D machine, equipped with a triple spiral mandrel extrusion head running a PP cosmetic bottle. Low-friction linear guides allow for efficient use of energy and low-wear operation, says Bekum. “Exact platen parallelism during the closing process and the uniform distribution of forces over the entire mould area promote flawless product weld lines and extended mould life,” it adds.
Thermoformers aim for efficiency
Thermoforming machinery manufacturer Illig will present automatic roll-fed (RDM-K) machines equipped with its new Intelligent Control (IC) technology that includes compatible control modules for optimising processes, with servomotor drives employed in all sections of the machines. One of the modules, ThermoLineControl, calls up and programmes all machine components of the production line centrally on the forming station. It will show the production of APET cups on an IC-RDM 54K machine, with a 520 x 300 sq mm forming area, 18-up tool and capacity of 50,000 cups/hour. PP hinged packs will be produced on an IC-RDKP 72 machine (forming area of 756 x 535 sq mm and six-up tool).
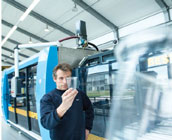
Compatriot Kiefel will present its Best stacking system on its KTR 5 SPEED cup forming machine, with quicker removal and packaging or filling of formed parts. Since the cups are stacked vertically, it creates optimal conditions for the next automated steps such as sleeving and packaging, says the firm. The stacking station has been developed by Kiefel for the food industry. Another stacking system will be showcased with the KMD 78 SPEED pressure forming machine. By means of a 16-up tool, PP biscuit trays will be produced. The horizontal stacking is rounded up with a conveyor belt for transporting the stacks out of the machine.
Auxiliary equipment makers to showcase a wide range
MTI Mischtechnik will present its Uni tec, Eco plus-line and redesigned Vent tec aspiration system. Designed as vertical-type systems, the Uni tec Universal Mixers are suitable for the preparation of plastics, with a single mixer combining multiple process steps. The Eco plus-line is an upgrade of the heating/cooling mixer combinations launched at K2010, to cater to the demand for doublebatch machines capable of mixing PVC-U for the volume production of pipes/profiles at over 10 tonnes/hour. Vent tec has a special emphasis on improved dehumidification performance under constant production conditions. The system adapts automatically to the different process phases in the mixing operation.
Meanwhile, Motan will launch a new range of Luxor CA S small compressed air dryers with hopper volumes of 0.75, 1.5, 3 and 5 litres, for the production of small/ micro parts. The dryers take factory supplied compressed air and expand it to atmospheric pressure. This produces dry process air with a very low dew point, which is then heated to the required drying temperature. No desiccant is required. All models are equipped with a thermostat and low air flow safety switch to prevent overheating of the material in the event of insufficient air throughput. It will also highlight its Ultrablend gravimetric batch dosing and mixing equipment for medical applications. Due to its IntelliBlend technology, this silicone-free system offers high dosing and consistency, says Motan. It is also equipped with filterless conveying and electropolished stainless steel for a hygienic working environment. Meanwhile, the GRAVInet GP control system has been joined by a more compact GRAVInet GP light for up to two dosing modules. It is equipped with a new WEBpanel with a 12.1" TFT touchscreen and Ethernet connection.
Antares is a new line of compact single-shaft shredders made by Lindner reSource, said to deliver up to one-third more throughput than previous machines but at the same price. Available in four design sizes and numerous equipment configurations, the units are suitable for recycling post-consumer materials, films, filaments, start-up lumps and sheets/plates. At the user's option, each machine can be equipped with a point-blade rotor or an energy-saving square blade rotor for hard plastics, with motor ratings from 37-110 kW and outputs of 500-2,500 kg/hour. Another innovation is the optional Skylight maintenance and service hatch, which is operated manually and permits a quick replacement of the blades and counterblades.
ProTec Polymer Processing is focusing on its Somos systems for drying, conveying and dosing pellets and regrind, with a new BB 500 gravimetric batch dosing for up to four components and output of up to 500 kg/hour (at a bulk weight of 0.6 kg/l). The device is mounted directly on the material intake of the injection moulding machine – or on a frame next to the machine – and can be equipped with Somos suction conveyors for automatic filling of the material supply tanks. Up to 50 stored, individual mixture formulas can be called up.

ProTec will also present the OHL process where washed/reclaimed PET bottle flakes can be reprocessed into rPET. It uses a continuous extrusion process and the discontinuous treatment of the extracted pellets in the OHL tumble reactor, which is a rotary reactor that can be heated and evacuated. During the PET reprocessing, the re-pellets are freed of volatile contaminations (decontaminated) and post condensation (increase of intrinsic viscosity IV) is simultaneously undertaken. The process is supported by upstream auxiliaries.
Koch-Technik will present a new Graviko gravimetric dosing device that uses two load cells. Every filling is weighed and the dual weighing unit registers the values and transfers them to the Koch control unit. This in turn compensates for fluctuations until the dosing recipe is reached accurately. Once all the values match, the dosed batch is emptied into the mixer below. Here a horizontal agitator homogenises the mixture before it is processed in the subsequent process. The Mcm-g Touch control unit from Koch-Technik is used to calculate and control the dosage values as stated in the recipe. Once the recipe has been entered, dosing takes place starting with the first cycle without the need for calibration. Because the Graviko devices are structured using Koch-Technik's modular system, the user can move, swivel away or fold up all device components for rapid material changes.
Nordson Kreyenborg will display a hydraulic power unit with two pumps that overcomes resistance during slide plate or diverter valve operation. The volume flow pump draws on a larger volume of oil to provide fast movement when the level of resistances is low while the high-pressure pump uses less oil but generates a pressure build-up that overcomes high levels of resistance. The two pumps are controlled via an automatic switching valve that shuts either the pump on or off as required. The new system is said to eliminate costs associated with maintaining pressurised accumulators and safety inspections (Inspections must be carried out every one to two years in Belgium, for example, and every five years in Luxembourg and Germany.) In addition, the two pumps are supplied from a single oil reservoir and are driven by a single motor, simplifying the design and reducing the initial investment.
In a conventional hydraulic system for slide plate screen changers, a pressurised accumulator is required to overcome the resistance caused by residual degraded or baked-on polymer, which can otherwise impede the movement of slide plate in a screen changer or of the bypass, start-up and switch-over valves used in processing applications.
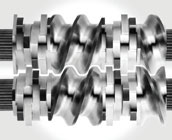
Screw/barrel maker Burgsmüller GmbH, a company of KraussMaffei Berstorff, will exhibit the successful use of nanoparticle layers that give high wear protection for components. The 140-year old company says the development of the new process for the application of hard-coating layers made of closed nanoparticles such as of tungsten carbide extends the life of screws and barrels, giving optimum resistance against corrosive, abrasive or adhesive wear. It says it is not necessary to treat the entire screw or barrel, treating only the zones that are exposed to intensive wear. Nanoparticle layers serve as wear protection when processing abrasive materials like WPC, standard and engineering plastics, biopolymers or substantially contaminated recycled material.
(PRA)