With suitable molecular configuration, plastic materials can be used as electrical conductors and semiconductors (albeit with still limited mobility of the charge carriers), to serve as system components of “organic” and “printed” electronics. Innovations will also be on show at the Printed Electronics Products and Solutions Pavilion at K2013, in Düsseldorf, Germany.
Plastics with modifiable material properties, dimensionally stable as thermoplastics, thermosets or elastomers, films or coatings, granular or expanded, are an indispensable part of our everyday lives – in anything from simple items of daily life to intricately designed structural elements in vehicles and buildings.
Plastics’ structural diversity is now being augmented by a further dimension: with suitable molecular configuration, they can also be used as electrical conductors and semiconductors (albeit with still limited mobility of the charge carriers). They thus serve as system components of “organic” and “printed” electronics. “Organic” because their transistors, sensors and LEDS are not based on silicone or gallium arsenide, but on carbon derivatives. And “printed” because two-dimensional circuit patterns can be printed “from the reel” with structural fineness of just a few tens of micrometres onto flexible and also transparent substrates by using conventional mass printing processes (flexo, screen-printing, inkjet).
Integration in objects
This yields electronically or photonically functionalised surfaces, threedimensionally on all conceivable objects and even textiles. They form capacitive touch sensors, large-area luminous fields with OLEDs (organic light-emitting diodes), sensors and detectors for environmentally or medically important data such as temperature and humidity. They operate as organic solar cells. Or as flat, printed batteries for miniaturised devices. This facilitates new, exotic applications in “smart” objects and their networking in the “Internet of Things”.
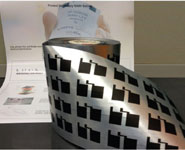
The latest (fifth) edition of the Roadmap of the OE-A (Organic and Printed Electronics Association), a work group of VDMA (German Engineering Federation) with over 220 members worldwide, illustrates the state of progress and trends in organic electronics for a ten-year period.
OLED screens and displays, the first mass market
The small OLED displays in mobile phones and smartphones have already developed into a mass market. As a result, sales with organic electronics came to roughly US$9 billion last year. This has been forecast to develop into a global annual market of US$200 billion by 2025. Colour-intensive and high-contrast OLED screens for 55 in. televisions are already available (e.g., from Samsung and LG), although they currently cost US$10,000.
Flexible displays for e-readers
The e-readers from Amazon and Sony with “electronic paper” from E-Ink enjoy widespread popularity because of the energyefficient, bi-stable principle of their electrophoretic displays. They are essentially ideal for presenting static content such as book pages.
The next development step will bring forth lighter, flexible and maybe even roll-up e-readers and tablets without the heavy cover glass. The most progress here has been made by British company Plastic Logic (founded by researchers from the Cavendish Laboratory at UK’s Cambridge University) that produces backplanes of organic thin film transistors (OTFT), i.e. the active matrix for individual pixel control.

The latest milestone along the way is a thin, easily flexible e-paper display with a 10.7 in. diagonal and with a resolution of 150 dpi (dots per inch) it comprises a matrix of 1280 x 960 TFTs, i.e. a total of 1.2 million pixels.
In the organic sensor field, Plastic Logic in its cooperation with ISORG in France, an enterprise hived off from the large CEA-LITEN research complex in Grenoble, also clearly leads the field. The two of them recently unveiled a 4 x 4 cm image sensor with 8930 pixels on a thin plastics substrate.
What is still hampering the development of organic photovoltaics and display technology is their hermetic encapsulation to provide protection from atmospheric water vapour that corrodes their electrodes and shortens their service life. So far, such encapsulation has only been possible with rigid cover glass.
The solution for freely contourable solar cells and flexible displays is laminated barrier films, for which transparent layers of amorphous silicone dioxide appear to be very well suited.
These are being collaboratively researched and developed at various locations including at the Fraunhofer Polymer Surface Alliance (Polo) and at the Japanese National Institute of Advanced Industrial Science and Technology (AIST).
Application driving forces
The driving forces in the development of applications can be found in the automotive, pharmaceutical, consumer electronics and “smart” packages for foods, medicines and other consumer items. With inexpensive printed, radio-frequency identification (RFID) tags, smart packages are capable of making merchandise management more efficient and, with dynamically updated display fields, of informing the consumer of the best-before date, drawing attention to gaps in the cooling chain for sensitive goods and guaranteeing the authenticity of high-grade articles by establishing links to traceable supply chains.
Another current development includes some premium class cars that are already fitted with printed antennas as well as printed sensors for seat occupancy integrated in the seat covers to trigger the airbags as necessary. They also detect the weight in order to distinguish children from adults. OLED displays for reversing cameras instead of the traditional mirrors are also included in the cars’ equipment, as are the illumination of the instrument clusters on the dashboard and barely visible printed window de-icers.
Next in line are organic displays and touch sensors in premium class cars as replacements for mechanical indicators and switches. Then there are reversing lights with OLEDs, among other things at Audi, so that today’s LED lights can be replaced to save energy.
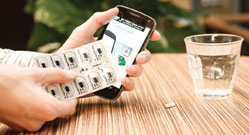
OLED lighting, organic photovoltaics and batteries
Of the four large fields of applications, OLED lighting, organic photovoltaics, electrophoretic (e-paper) and OLED displays, and electronic components as a complement to classical silicone-based microelectronics – the OLED light sources are competing with established LEDs and halogen lamps. They promise dynamically colour-controllable light emitted uniformly over a large area and can be attached in architecturally attractive ways to the surfaces even of familiar objects in the home.
Organic photovoltaics (OPVs), developing in parallel with hybrid alternatives made of titanium oxide and dyesensitised solar cells and with purely organic (polymerbased cells), are already commercially available as local supply sources for mobile data and consumer devices. However, because of their relatively low efficiency, they are not intended for feeding power into the public grids, but as local supply sources (energy harvesting) and charging the batteries of mobile data and consumer devices and measuring stations. The long-term prospects include applications in the envelopes of vehicles and buildings (BIPVs or building-integrated photovoltaics).
Available as system components are printed data memories – in the form of the ferroelectric, non-volatile memory films of Norwegian manufacturer Thinfilm. These can be combined with a transistor logic produced at contract researcher PARC in California to yield softwareaddressable memory modules. With a printed thermistor as a temperature sensor and a display field together with a printed battery, they can be extended into a complete measuring system.
Printed, slim and flexible batteries are also a focus of system integration. At present, the market is dominated by single-use zinc-carbon batteries, while rechargeable, lithiumbased equivalents are still undergoing development.
As an alternative, energy-rich supercapacitors are available for the temporary supply of power to devices. Their discharge behaviour comes close to that of batteries. Such power supplies can be integrated with display and luminous fields, touch sensors and solar cells in packages, textiles and other consumer items, elevating them to new levels of value and functionality.
(PRA)