K2016 Machinery Review
Also, download this story from the electronic issue here
W&H’s Turboclean launched; cost savings for material changeovers
During the K2016 show, at scheduled times of the day, Germany-based extrusion machinery maker Windmöller & Hölscher (W&H) was running and changing two five-layer POD (polyolefin-dedicated) films on a Varex II blown film line. The live show, coupled with an audiovisual display, in a fanfare of lights and sound, put to launch its latest Turboclean resin changeover system.
The entire concept served as an example of the company’s theme of “Packaging 4.0 – intelligent, integrated, intuitive”. Martin Backmann, R&D Manager, said, “The Varex II is an intelligent machine because the Turboclean can manage a resin change on its own and it is done in a matter of minutes, compared to the 40 minutes usually taken, because machine operators don’t have to clean each equipment component manually and reconnect the equipment again.”
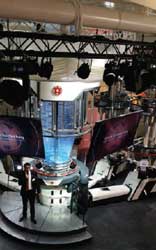
Backmann said that the new system is in line with two distinct mega-trends the company has noticed: increasing demand for quality and cost-effective production.
“We did a customer survey to find out what is lacking in productivity. We found out that 9% of downtime happens as a result of material changeovers. This works out to a huge amount on a yearly basis. Hence, we concluded that customers require a system that could allow for a short time to change the material.”
Though Turboclean is just a huge white box with hoses, and all an operator did at the show was to pull out hoses from one connection to link to another connection to change the material, there is more to Turboclean than meets the eye.
It cleans all the system components simultaneously rather than one by one. When a changeover is required, it stops the material from being fed, draining it at a high speed into bins under the gravimetric hoppers. Thus, it ensures that virgin materials are not mixed with the purged ones. Pressurised air is then blown through the system to remove residual pellets and new material introduced into the blown film line.
During the live demonstration at the show, the
machine was producing a blue food packaging film using
ExxonMobil’s Exceed XP polymer and it would then change to a red-colour collation shrink film, produced
using ExxonMobil’s Enable 4002 polymer. All this would
be done in 12 minutes, shaving 28 minutes off the entire
changeover time.
“We are keeping close to our theme of intelligent, integrated, intuitive. By integrating all processes of the machine and the intuitive touch screen user panel, resin changes can be completed in just a few minutes and uptime is increased by 6%. This is possible thanks to the combination of an intelligent algorithm with the automatic cleaning of gravimetric and vacuum conveyers,” said Backmann.
Meanwhile, materials firm ExxonMobil was collaborating with W&H to demonstrate how the combination of its new Exceed XP polymers and machine technology intelligence can enable five-layer film solutions.
“The Exceed XP exhibits extreme toughness and excellent seal performance, helping producers and brand owners protect and preserve food longer while the Enable 4002 offers high holding force and high transverse direction (TD) shrink for tight bundling to keep products secure,” said Olivier Lorge, Global Performance PE Marketing Manager at ExxonMobil.
He also said these new performance polymers allow for a step-up performance with cost advantages. “We are working with machinery makers to help customers achieve sustained business growth and differentiated solutions for applications, when extreme performance matters,” he added.
Erema's push on closing the loop in recycling
At K2016, Austrian recycling machinery maker Erema had a special outdoor pavilion housing its Careformance Recycling Centre, where it was recycling over 30 tonnes of plastic waste on its Intarema TVEplus 1108 recycling system during the show.
At the opening of the centre, Manfred Hackl, CEO of Erema, said that the image of plastics was bad and needed to be changed. “The presence of companies from different areas of the industry (today) is a strong message for the need to work together to close the loop,” he added.
Thus, Erema collaborated with materials maker Borealis and machine suppliers Hosokawa Alpine, Bobst and GEA to allow for the first time to produce stand-up pouches based exclusively on PE, for easy recycling.
Alfred Stern, Executive Vice-President Polyolefins and Innovation & Technology, Borealis, reinforced Hackl’s words. “Borealis is not just a polyolefins producer. We are now into recycling having bought recycling company mtm earlier this year.” He also emphasised the need for plastic material to be made more recyclable. “More attention needs to be paid to designing of products for recyclability. For example, laminated flexible packaging is extremely beneficial for food preservation, but consists of different materials that make it impossible to recycle.”
He also pointed out the collaboration on the 100% mono-material stand-up pouch showed how the closed loop system can work. The pouches produced on site, including any production waste, were shown recycled live and the recyclates processed directly on an OCS extruder to make blown film.
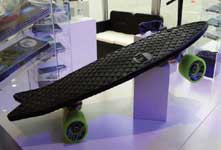
Erema also used the opportunity to present the first Industry 4.0 package in the field of plastics recycling. "Building on the Smart Start package presented at K2013 and the Intarema systems' high degree of automation connected with it, Erema has developed a Smart Factory package for producers and recyclers. On one hand, the process data of the individual machines is analysed and, on the other, the production and recycling facilities are interconnected with the entire process chain," explained Hackl.
The machine, quality and process data of the recycling process was being relayed in real time directly from the Recycling Centre to Erema's booth during the show.
Hackl said that he is confident that this digital quality proof will further increase the amount of recyclate used in the production of plastics.
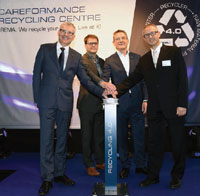
Meanwhile, compounding equipment maker KraussMaffei Berstorff will utilise Erema’s Intarema solution in its new re-compounding extruder, known as Edelweiss Compounding. With this solution, a first extruder is used for melting the reclaimed material before it is compounded on a second extruder. Owing to the integrated process on a single line of tandem configuration, the material processed need not be heated repeatedly, which saves energy, minimises the shear stress produced during plasticising and allows for improved material quality. In addition, re-compounding allows processors to use cost-effective reclaimed material, say the companies.
WM adds a twist to its new machine model
Switzerland-based WM Thermoforming Machines premiered its brand new Twist 700, a larger machine that succeeds its smaller Twist 300 model. According to Luca Oliverio, WM’s Sales and Marketing Director, “The Twist 700 is one step higher. It uses a similar motion concept that was used on the Twist 300, but the latter was only for very small production. Twist 700 is not only bigger, but is also fully equipped with all the latest technology, including our MSv7 stacker.”
He went on to explain, “The new stacking concept offers great flexibility, by allowing customers to automatically count, stack and pack products of various shapes that are difficult to stack, from standard cups, and round or square dairy containers, to shallow products such as lids or coffee capsules.”
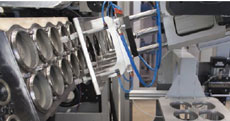
Oliverio also added that the machine runs on moveable mechanical cams allowing for the faster speed of up to 50 cycles/minute, without any vibrations. Featuring tilting mould technology, the machine also incorporates MLS (Machine Learning System) that helps technicians to optimise process parameters, synchronise the machine and stacking system, and rationalise material consumption.
As for the company’s business prospects, Oliverio said sales were 25% higher compared to 2015. “We saw growth come mainly from Europe, Middle East, Asia and South America.”
The Twist 700 was shown producing small clear bowls, with an outside diameter of 115 mm for dairy products, from 630-micron-thick UltraClear PP sheet that has Milliken’s Millad NX 8000 additive. The clarifying agent has removed the transparency obstacle for PP, clearing the way for PP to potentially replace other materials such as amorphous PET and PS in various packaging applications, says the US firm.
Using the mono-material concept of NX UltraClear PP in thermoformed applications also helps to facilitate end-of-life recycling of the resulting products. As well, it delivers significant weight savings. For example, Milliken notes, UltraClear PP trays typically are 15-20% lighter than comparable PET-based food trays.
Davis-Standard focuses on packaging machinery
US-headquartered extrusion/converting machinery maker
Davis-Standard expects favourable winds of change this
year. “Business is improving in Europe and the US and we
see an improvement in sales in Asia, with good activity
expected in the fourth quarter,” said President Jim Murphy.
With packaging machinery occupying nearly half its equipment portfolio, the company was showcasing its popular dsX systems for extrusion coating, cast film and blown film processes. “We have had positive industry response due to the competitive advantage in price, performance and delivery,” said Jim. He also added that the 450 m/minute-dsX flex-pack (extrusion coating) provides converters and printers an adaptable configuration for a variety of emerging applications.
Meanwhile, dsX s-tretch (cast film) is the first all-inone system of its kind for in-line, pre-stretch cast film processing, with integrated technology that eliminates the need for traditional pre-stretching methods, resulting in thinner films, faster line speeds and improved film strength. Films as thin as 6 microns at speeds from 550- 1,000 m/minute can be run in three, five and seven-layer configurations.
According to Sekaran Murugaiah, Vice-President Business Development Asia-Pacific, “We have orders for a number of extrusion coating and cast lines in Thailand, while the Indian and South Korean markets are looking exciting. The Korean Institute of Industrial Technology has invested in one of our lines to demonstrate and conduct further research.”
When asked about expansion plans, Jim said the firm will add on more product ranges to its Suzhou facility in China in the future. “It already offers wire/cable and medical tubing line capabilities as well as extruders; and we have added on 60 staff over four years.”
Rajoo runs five-layer mono-material line
India’s Rajoo Engineers, which makes blown film, sheet extrusion lines and thermoformers, was the only Asian company to demonstrate live its Pentafoil five-layer all-PE blown film line, in a throwback to K2013 where a five-layer barrier film line was running.
Its latest line incorporates advancements in technology such as cylindrical spiral die (CSD); internal bubble cooling; circumferential profile control with elevated air ring and triple lip; fully automatic winder and touchscreen-based supervisory control panel.
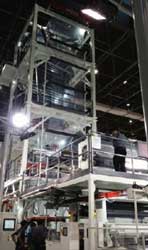
“It is packaged with an affordable price and energy consumption is only 0.3kWh/kg,” said Sunil Jain, President. Besides the lower energy consumption, Sunil contended that the five-layer line allows processors to get more out of less by downgauging.
With a maximum output of 650 kg/hour, the line can produce PE film in a thickness range of 30-250 microns.
“The line has been configured to produce films that comply with difficult industry demands and specifications that provide a competitive edge to customers’ businesses, in terms of both diverse film properties and costs,” explained Sunil, adding that response had been encouraging.
The company also commemorated its 30th anniversary in business at the show.
(PRA)Copyright (c) 2016 www.plasticsandrubberasia.com. All rights reserved.