DuPont Performance Polymers: helping customers create differentiated products
Also, download this story from the electronic issue here
From nylon for stockings and car parts to advanced materials for aerospace components, US materials innovator DuPont Performance Polymers (DPP) has rewritten history with advanced materials and application development.

Advanced materials: the building blocks of differentiated products
Just 80 years ago, DuPont defined the high-performance plastics market with the invention of nylon. Today, it is used all over the world in a variety of automotive components, such as air ducts, engine covers, charged air coolers, transmission components and radiator end tanks. In electrical and electronic systems, Zytel nylon is widely used in enclosures, sockets, terminal blocks, circuit breakers, switches and relays.
Over the years, DuPont has built on that strong foundation and offers the industry’s widest range of nylons, polyesters, elastomers and bio-based polymers. DuPont continues to focus on strengthening and growing its leading position in high-value advanced materials, as it is one of the three areas of strategic priority for the company.
What to make of them?
“As important as materials are in product development, the understanding of how to work with them to get the greatest performance and benefit is imperative,” said Yasuhiko Ohashi, Automotive Marketing Manager of DPP Asia Pacific.
“To help our global customers get the most from DuPont materials, we have over the years, established a network of development experts with tools and networks to help support a customer from the concept all the way through to production.”
Application development: innovating with confidence
Woong Chung, Technical Service Manager of DPP Asia Pacific, shared with PRA how DuPont is enabling its Advanced Materials Application Development.
“Our application development process is how we support our customers’ product development cycle,” said Chung.
“It can start with imagining a new product and engaging us in the design brief and material selection. It can include design support through CAD, CAE predictive engineering, and testing as we move through the product-development cycle. And we can also support customers during the manufacturing stage as we help improve production yield.”
To summarise, Chung said: “What we do is to help customers make informed decisions as they imagine, design and develop a new application or improve an existing application.”
Putting application development to work in the automotive sector
One of the critical objectives in the automotive industry is light weighting to improve fuel efficiency. But when redesigning parts with plastics, the light weighting design may bring noise, vibration and harshness (NVH) issues due to differences in mass, stiffness and damping. Yet it’s imperative that today’s efficient vehicles are comfortable and deliver on performance.
To address this challenge, DuPont has developed the full-spectrum of NVH capabilities to support material development, design and simulation and part validation.
For this purpose, DPP offers a new grade of Zytel nylon, a proprietary class of polyamide that is especially designed to improve the damping of the material and reduce noise and vibration.
“In addition to its ability to absorb NVH, this optimised grade of Zytel offers the right blend of strength, stiffness and resistance to creep, deformation and fatigue to stand up to load and stress,” said Chung.
“We’ve worked with several automotive makers and found that adoption of the new grade of Zytel, together with the DuPont NVH design solution, can help attenuate the vehicle noise effectively compared with the conventional plastic engine cover. The new Zytel grade serves as an example of how we can optimise the resin’s performance to meet customer’s needs.”
The offering in material and design will bring more metal replacement opportunities, such as timing belt covers, oil pans, engine mounts, air ducts and other components.
Seamless technology-assisted design
The air duct market is growing rapidly due to global demand for turbo-charged engines, which also improves fuel economy without sacrificing performance. To cater to this, DPP has invested in a 3D suction blow moulding machine at the Utsunomiya Technical Centre in Japan. DuPont has also developed in-house simulation tools to predict the 3D suction process and tube twist in the mould to help ensure uniform wall thickness. This investment and the company's unique 3D suction blow moulding simulation software will help customers optimise air duct design without physical prototyping.
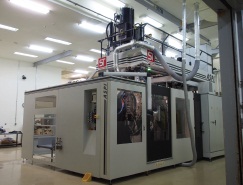
The need for seamless technology-assisted design extends beyond the automotive industry. In the handheld and consumer electronics market, the need for design flexibility is driving designers to high-performance plastics so they can continue to refresh the look, feel and upgrade performance.
Thus, to cater to further development in this market, DuPont added a 450-tonne injection moulding machine at the China R&D Centre, which is co-located with the 3,800 sq-ft DuPont Shanghai Innovation Centre.
Chung said, “Our emphasis on design, materials and processing solutions reflects our holistic approach to collaborate with customers. The new injection moulding machine expands the tools and resources available to customers in China and Asia Pacific as we quickly develop and commercialise new components and systems. At the same time, the drive to improve collaboration is changing how we work together and we are seeing strong results as we have taken time, cost and risk out of the product development cycle.”

Importance of virtual modelling
Today, product development needs to move efficiently and accurately. To help customers shorten the distance between the concept and the commercial launch, DPP has invested in people and technology to support test tooling, optimise processing technology, develop prototypes and access advanced CAE (computer-aided-engineering) on anisotropic properties characterisation.
DuPont technical experts in Europe recently demonstrated how close its advanced CAE modelling capabilities can predict the performance of automotive parts with a series of engine brackets made of Zytel. The structural engine brackets or mounts, which stabilise and align the engine, were developed in collaboration with global powertrain system and component supplier ElringKlinger and German car maker Daimler on an accelerated timeline, enabling a shorter development cycle compared to standard die-cast aluminium, and at a reduced cost.
DuPont uses Digimat, the advanced micromechanical material modelling software, to optimise the FEA modelling of glass-reinforced materials, analyse local changes in material properties and identify any structural weaknesses in the design.
“Predictive capabilities around the world have become a critical part of our core competency in application development,” said Chung. “We have to be able to help validate design solutions to reduce cost and time to market.”
As a result, and as predicted by the shared data ahead of real part testing, the plastic engine brackets validated by Daimler can fully replace metal, offering improved noise damping, and positive effects on fuel efficiency, driving comfort and safety, says DuPont.
Advanced materials application development
“In the 80 years since we invented the engineeringplastics market segment, we’ve found our customers get the greatest weight, cost and performance benefits from using plastics and polymers when they engage us as a trusted advisor early in the product development cycle,” said Ohashi.
“We are the source of balanced materials information because we offer such a broad base of materials solutions. And we have the global reach and experienced developers to help customers innovate with confidence,” he concluded.
(PRA)Copyright (c) 2015 www.plasticsandrubberasia.com. All rights reserved.