Also, download this story from the electronic issue here
Featured are five extrusion machinery companies: Reifenhäuser that has sold lines in Asia; Macro that has introduced an option of a gas foamed layer; Davis- Standard with a high output air ring; Rajoo with its new competitively priced three-layer line, and Amut featuring a dimpled sheet line.
Reifenhäuser forges ahead in Asia with its lines
Asia is an important focus market for Germany-based extrusion machinery maker Reifenhäuser Group. Its subsdiary Reifenhäuser Cast Sheet Coating alone has been able to install more than 15 lines here over the past 18 months. The group-wide annual growth of the market has been in a double-digit percentage range since 2009. Therefore, Reifenhäuser has strengthened its local sales team in recent months, and has expanded the Reifenhäuser China site to optimise customer support by own sales and service staff.
Recently the company made two significant announcements. Reifenhäuser Cast Sheet Coating is building two five-layer CPP film lines for the production of lamination film and metallisable film to be supplied to Malaysian processor Scientex Great Wall (SGW).
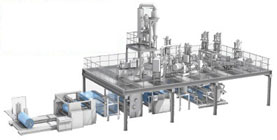
This is a new market for SGW that will use Reifenhäuser’s Midex series, with the Reicofeed 2.1 feedblock, said to improve film qualities and thickness tolerances and the distribution of layer adjustment.
Designed for a maximum net film width of 3,250 mm and an output of up to 1,288 kg/hour, each of the lines will produce about 300 m/minute of film.
Elsewhere in India, Varun Beverages of the RJ Group, the biggest franchisee of PepsiCo India, has installed a three-layer Evolution blown film line from Reifenhäuser Kiefel Extrusion at its plant located in Alwar, Rajasthan. The 2.6-m wide line will produce collation shrink film for packaging of Pepsi bottles and water bottles from PET. It is the first blown film line of the company. With this investment, the Indian MNC completes its vertical diversification.
Reifenhäuser Kiefel Extrusion has equipped the line with the Evolution Ultra extruders and Ultra Cool technology, which is the current blown film cooling system from the German machinery maker, with an output of up to 700 kg/hour based on Varun’s recipes. The line is also provided with the latest generation Evolution WP winder, allowing for fast conversion of the film thanks to straight-edge winding and multi-up rolls. The Evolution C automation system, developed by Reifenhäuser Kiefel, features an intuitive user interface and 24-in touch screen panel for employees to get familiar with the operation of the line, rapidly and without any problem, says the machinery supplier.

Varun Beverages, the flagship company of RJ, holds bottling and distribution franchise rights from PepsiCo not only in India but also in Nepal, Sri Lanka and Africa. In India, it manages nine PepsiCo bottling plants in Haryana, Uttar Pradesh, Rajasthan, Goa and Delhi.
Gas foaming in barrier films for reduced weight
Canadian film and sheet extrusion systems supplier Macro Engineering & Technology has added the option of individual layer gas foaming to its barrier blown film co-extrusion lines.
Macro’s blown film co-extrusion systems are used to produce films with up to 11-layers and up to 3-m wide using a variety of materials, including PA, EVOH and PVdC. The films produced are most typically used in food and medical packaging applications. The individual layer foaming option allows processors to create a wider range of products by manipulating different foamed layer combinations within the co-extruded film structures.
Similar to foaming in injection moulding, foaming in extrusion can reduce weight, leading to raw material savings and can also create favourable properties in the film, such as improving thermal and sound insulation, and opacity can be obtained without using fillers.
Earlier this year, Macro also announced the addition of individual layer foaming technology to its cast barrier film lines along with a seven-layer cast line installation in Europe that produces barrier films with layer foaming in two of the seven layers.
Similar to the cast technology, the blown system features individual layer foaming that is achieved with nitrogen gas injection through a proprietary feedblock. The configuration of the line allows it to be operated with or without foam injection, allowing the film producer to easily switch between foamed films and conventional multilayer film production without changing machinery.
Macro says the addition of individual layer foaming to its blown film co-extrusion systems broadens the possibilities of end-use applications by producing barrier films that are stiffer and thicker without increasing materials costs. The rigidity of the foamed films makes them suitable for stand up pouches and thermoformed trays.
Macro is currently building a nine-layer blown film line with individual layer foam technology that will be delivered to an undisclosed film manufacturer in Europe. The line will produce high barrier films and can foam individual layers or several layers together, depending on the application.

New air ring for higher outputs
US extrusion machinery firm Davis-Standard has introduced the Upjet air ring system for blown film processes, With a stalk configuration, improved IBC and Venturi ring design, the Upjet is said to enhance the cooling efficiency of new blown film lines to increase output while improving thickness tolerance.
It is targeted at commodity markets such as stretch film, can liners and industrial films. The firm says it has seen “impressive results” for processing stretch films and can liners for a variety of applications, including technical agri stretch products and general purpose sheeting.

It is for use on existing and new lines in a manual or auto-profile mode. When used with Davis-Standard’s WesJet TPC automatic profile control and Centrex or Vertex dies, the firm claims an output increase of up to 40%.
Upjet is available in sizes ranging from 180-1,016 mm, in manual or motorised elevation control and passive or automatic thickness profile control configurations.
New blown film line is lighter on the pocket
Indian extrusion machinery manufacturer Rajoo Engineers has introduced the Multifoil Lite two-extruder, three-layer blown film line, a lower-priced version of its Multifoil line that was showcased at the K2013 show in Germany.
According to Rajoo, the new line will provide customers with a cost-competitive option in the highly competitive bag making industry, plagued with increasing costs of raw materials. Likewise, the line will provide other benefits such as minimal downtime, low energy consumption, and flexibility to adapt to varied applications.
The development came about as a result of the company’s interactions with retailers and its objective to better understand their needs, particularly in the manufacturing of shopping bags and other applications that make use of films.
While it is designed to run with an A-B-A configuration, its special cross head design provides the flexibility to run A-B-B and A-A-B configurations, said to be a first of its kind in the industry.
The extruder sizes are 40 mm/50 mm; machine output is 120 kg/hour; an LFW of 400-1,150 mm, with an oscillating haul-off for gauge randomisation.
Rajoo says it is also possible to use up to 50% calcium carbonate or recycled material (in the middle layer) with virgin material in the skin layers. The abrasive materials would normally impact machine parts adversely. However, Rajoo says its screw and barrel are especially designed to handle the high filler content.
Apart from shopping bags, this machine can also be used to produce films (for milk and water packaging) and lamination grade films (with slip on one side and non-slip on the other).
Dimpled sheet line allows for post-consumer flakes
Italian extrusion machine maker Amut has recently manufactured and tested a plant for the production of 4-m wide HDPE dimpled sheet for a Russian customer that is one of the biggest producers of materials for the building sector. The sheet is largely used to protect and provide drainage for underground walls and it is the latest solution for the proper protection and ventilation of the waterproofing mantle between cement foundations and the ground, according to Amut. It adds that its versatility makes it essential for the realisation of buildings in areas where water presence is particularly high.
The line has a capacity higher than 1,700 kg/hour and it offers the possibility to produce a width of 4,000 mm, or by applying a central cutting to obtain two rolls of 2,000 mm each or even four rolls of 1,000 mm each. The linear kinematic speed is equal to 12.5 m/ minute, while the thickness range varies from 350-1,000 g for every sq m.
Based on an EA180 single-screw extruder with L/D 45, which is equipped with a vacuum vent system with closedloop water circuit (for post-consumer material), the line is able to process granules as well as trims/flakes or post-consumer HDPE recyclate. It is composed of a loading system, dosing unit, continuous screen changer, high pressure gear pump and a flat die with melt exit width higher than 4,300 mm, to produce the maximum width even on a low potential thickness of the finished product (< 300 g/sq m).
It has a special calendering/forming unit, which when processing the required width and combined with the linear speed, is said to guarantee an accurate realisation of the two main forming rolls (10 m/minute of finished product). Cooling flows are by means of recirculation/thermoregulation pumps.
Since the line can process 100% post-consumer material, the vacuum unit had to be designed with condensation/ reduction systems for the pollutants in the melt that can cause problems in the vacuum circuit.
Downstream the calendering/ forming unit, an unwinding/lamination station has been installed. It comes complete with a distribution system for hot melt glues used for different material adhesion. The end-of-the-line is composed of an automatic winder complete with a bench for unloading/ stacking the finished rolls.
The plant is also equipped with ancillary equipment, such as bilateral unwinding of the advertising/signalling strap that is directly applied during the forming phase and a grinder for trims, which are conveyed to the loading/ mixing zone.
A proprietary software, developed and tuned specifically for this line, controls and checks all parameters, by storing and monitoring the whole production process.
(PRA)