Also, download this story from the electronic issue here
The energy crisis is a modern-day phantom that stalks and threatens global economies and industries. The good news is that energy shortages may be controlled. And thanks to modern photovoltaic technology that enables for a widely accessed and, in the long run, cheaper solar energy, says Angelica Buan in this report.
In the face of the surmounting energy crisis, photovoltaics (PVs) technology seems to provide the panacea to energy woes. PVs are solar cells that convert energy from the sun to usable electricity. The current technology utilises a semiconductor to absorb the radiation from the sun and when this happens, the radiation emits electrons, which are harnessed as electricity.
Solar energy is a renewable energy of choice because of the persisting problem on climate change plus solar energy is clean energy with an edge over price volatility of fossil fuels. Moreover, it emits no greenhouse gas or other toxic pollutants such as sulphur and nitrogen, and requires slight amount or no water, compared to thermal power plants, which need fresh water for cooling.
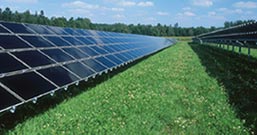
Expensive price tag an issue
But while potential energy from the sun is free, the use of PVs to harness it is expensive and not cost-competitive with readily available utility power, according to the Florida Solar Energy Centre. The agency says that until such time that the cost per peak watt (the amount of electricity produced by a PV cell when bright sunlight is available), is competitively low can the technology be used more widely. In this purview, manufacturing and applications are two key areas of development in PV technology.
The International Energy Agency (IEA), meanwhile, notes that costs are decreasing, forecasting that by 2050 solar energy could be the top source of electricity generating up to 16% of the world's use.
US-based financial firm Lazard also echoes the view of decreasing costs saying that costs have dropped by nearly 20% in the past year, and nearly 80% in the last five years. China's entry into the solar panel business has helped push down the costs, says the firm.
New York-based Transparency Market Research (TMR), in its PV market report from 2012-2018, says that current technologies still utilise semiconductor materials such as the costly silicon. Yet, innovations are being undertaken to bring down costs as well as improving efficiency, it says.
Developments are taking place as pointed out by the National Renewable Energy Laboratory (NREL) of the US Department of Energy. It explains that second-generation thin-film solar cells are developed from amorphous silicon or non-silicon materials such as cadmium telluride. Thin film solar cells use layers of semiconductor materials only a few micrometers thick and can double as rooftop shingles and tiles, building facades, or glazing for skylights.
There are also third-generation solar cells made from new materials such as solar inks using conventional printing press technologies, solar dyes, and conductive plastics that concentrate sunlight onto a minute piece of high efficiency PV material, albeit at a higher cost.
Currently, the US-based University of Cincinnati is working on making less expensive, yet more flexible and efficient, solar-powered panels in lights, calculators and roofs. Researchers are looking at adding nanoflakes of graphene to polymer-blend bulk-heterojunction (BHJ) solar cells as a substitute to silicon solar cells. The graphene increases the plastic solar cells’ efficiency threefold. Yet for now, it is comparatively below the highest efficiency achieved in organic PV devices.
Scale of use growing in Asia
Energy market analysts observe that solar PV end-market demand is spreading and shifting from Europe towards Asia. TMR reported that the three fastest growing PV markets in 2013 were China, Japan, and Thailand.
The market has two leading manufactured solar PV technologies that are implemented in the commercial use: thin-film PV and crystalline silicon PV. The latter currently dominates the market growth with around 80% of the market share. TMR also reports that major countries seen as active in thin-film PV technologies include China (12%), Asia, Europe, Japan, Germany (19%) and South Korea.
Meanwhile, IEA assessed that solar PV expansion would be led by China, followed by the US.
In India, solar PV is also gaining ground. L&T Construction, the nation’s largest solar EPC company, has recently commissioned what it claims as the world's largest solar PV plant of 7.52 MW capacity on a single roof in Amritsar, Punjab. The energy generated from this plant is being fed to the local grid through a power purchase agreement signed with the state distribution company under the New and Renewable Sources of Energy Policy.
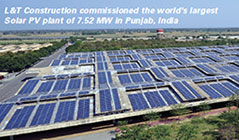
To optimise efficiency, L&T employed multi-crystalline module technology and central inverters. More than 30,000 panels were erected on the 94,000 sq m roof.
Considering that the rooftop modules had to be erected on fragile asbestos roof sheets, L&T designed a system whereby the entire load of the PV modules was transferred to the space frame of the top and middle chords of the roof. Lightweight aluminium structures were used for mounting the modules and the roof is waterproofed to avoid leakages.
US chemicals firm DuPont has also come up with PV solutions for India’s Tata Power Solar. DuPont says its Solamet metallisation pastes help increase the conversion efficiency of solar cells, boosting the power output of solar panels. Meanwhile, its ionomer encapsulants surround and protect solar cells and panel circuitry; and its Tedlar PVF film-based backsheets are said to to ensure a 25-year lifetime, even in extreme climates such as in many parts of India.
Tata has recently collaborated with Aditya Birla Solar to set up a 20-MW power plant near Jodhpur in Rajasthan, which will deliver solar energy to an estimated 300,000 rural households in India.
In Japan, the first PV plant has just been completed. The project is built by the Spanish-Japanese conglomerate Europe Clean Energies (ECE). The Tsukuba district-sited plant, which began construction early this year after ECE acquired a feed-in-tariff of US$0.39 per KW transferred to the regional electrical grid, has a capacity to generate 2 MW of electricity. It uses two ABB 1 MW stations and 7,950 modules of 255 W each from Ontario-based Canadian Solar. ECE will be constructing two other PV power stations in the Ibaraki prefecture.
Meanwhile, in Australia, the University of Queensland (UQ) is building a 3.275-MW solar PV research facility at its Gatton campus. The plant will cover 10 ha of the Gatton campus and will produce enough electricity annually to power more than 450 average Australian homes, equivalent to displacing more than 5,600 tonnes of carbon dioxide. PV solar systems provider First Solar will install about 40,000 thin-film PV panels in ground-mounted arrays. The project is scheduled to be commissioned early next year and will provide 30% of the UQ Gatton campus’ energy.
Ripe time for new technologies
NanoGram, a Teijin company, has developed what is said to be the world’s first printable electronics material, NanoGram Si paste, for the local back surface field (L-BSF) PV cell, with an insultion or passivation layer. An impuritydiffused layer is attached to the back of the electrode and partially underneath the electrode to diffuse impurities such as boron, phosphorus and aluminium by furnacing or lasering. The paste, which contains approximately 20 nm-diameter silicon nanoparticles, is said to enable the highly efficient collection of solar energy in silicon wafers. A high-performance impurity-diffused layer can be formed when NanoGram Si paste is printed and heated on a silicon wafer.
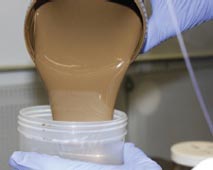
Teijin has also developed its own technology for screen printing and lasering process of the paste on a silicon wafer, resulting in a further 0.5% increase in the L-BSF PV cell’s conversion efficiency. This effect has been verified using a 6 in. PV cell developed together with the German Fraunhofer ISE research institute.
In Canada, Canadian Solar has developed a new solar PV module, which it expects to launch in 2015. The Diamond module, or the double PV module, utilises heatstrengthened glass instead of the traditional polymer backsheet. It is Potential Induced Degradation (PID)- free with anti-PID cells, encapsulated material and no metal module frame. Other benefits include its ability to withstand harsh environmental conditions, including high humidity, temperature and ultraviolet (UV) conditions. Its increased resistance to salt corrosion translates into a robust solution for seaside/waterside PV system installation, says the company.
Canadian Solar explained that in the first year, annual power degradation is 2.5% and 0.5% each year onwards. With that, module output at the 25th year is maintained at 85%, versus the current 80%.
Meanwhile, France-based Schneider Electric is launching a new PV Skid, an optimised plug-and-play power conversion system designed for North American solar PV power plants. Based on the successful Conext Core XC-NA UL 1741 1000 VDC inverter platform, it is available in configurations from 1 MW to 2 MW AC with several optional features, such as extended temperature range from - 35 to + 55°C, load centre for tracker systems, and a canopy for sun protection.
(PRA)