
Chinese extrusion machinery maker Jinming says it has successfully completed Phase 1 of its technical centre. The Shantou-based firm says it has been playing a leading role in technical innovation in the domestic industry and in realising advanced film making techniques. Thus, the Jinming Technical Centre was completed in April at its headquarters in Shantou, after over a decade of planning to build it. The company says it has invested “millions of RMB” in its first integrated platform in the Asia Pacific region.
According to Li Hao, Director of the R&D Department, key activities that will be held in the technical centre include (but are not limited to) product R&D, formulation experiments, training of process engineers and undertaking machine test runs and production simulations for customers.
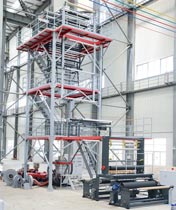
The workshop covers an area of 1,500 sq m and is equipped with a water-quenched high-barrier blown film line and a five-layer blown film line (1,700-2,800 mm). Others include a single-screw extruder and a multi-layer co-extrusion blown film line (900-1,700 mm).
Various tests have already been conducted at the centre, says Jinming, citing a few, such as a test carried out in August for a M5B-900QA heavy-duty blown film line with a capacity of 350 kg/hour; development of PVDC high barrier lamination broad-width blown film line, as well as a nine-layer co-extrusion barrier lamination broad-width (2,000-mm) blown film line.
It has also successfully tested a forced-feeding single-screw extruder (extruder of 150 mm diameter) to render a capacity of 900 kg/hour; and special equipment for self-adhesive protective film for the electronics industry.
The company says that it intends to develop world-class film making technology to resolve customers' concerns in respect of formulations and production processes and also conduct operation training involved in the field of blown film technology.
Recognising loyalty of customers
Meanwhile, Jinming says that high quality need not come at a high price. Recently, it offered to valued customers 30 classic models of the Valuex three-layer co-extrusion blown film lines at what it said was an “unprecedented cost price”. The promotion, which was to commemorate the company’s third anniversary listing on the Shenzhen stock market in 2011, lasted from August to October.
The modular Valuex three-layer co-extrusion blown film lines, EM3B-2000QE and EM3B-2300QE, were developed for general domestic customers. Features include stable performance and ability to produce universal products, especially food packaging bags, heat shrink film and lamination film.
The lines use a lot of Jinming’s classic technologies, in which the main configurations include centre feeding spiral distribution three-layer co-extrusion head, RD-I double-outlet air ring, horizontal rotating traction device, WSD-I fully-automatic duplex surface-friction winder, and siding display closed-loop control inner-cooling technology.
Jinming also says the screws for the lines are designed by experts from top material companies globally,and cater to a broad applicable range of raw materials as well as LLDPE. Another feature is that production efficiency is 20%-30% higher than other equipment of the same type. A central touch screen control is also employed.
Developing new controller to break the hold of foreign companies
Further embarking in advancing its blown film line line-up and to break the hold the foreign blown film line manufacturers have on the industry sector, Jinming is developing a control system with Xi’an Jiaotong University. It is expected to begin trial production and come into effect in 2016.
Jinming explained that this project, based on the SOC (System-on-a-Chip) control system, is one of the core technologies in the plastic machinery industry at present. “Currently, only a few developed countries have a good grasp of this technology, “ it said, adding, “The successful R&D will break the monopoly of the high-end blown film lines of foreign countries, changing the present situation in the industry, that is, powerful in machinery but weak in electronics, and increasing the profit margins for domestic equipment.”
The company describes the multi-layer co-extrusion blown film lines as having intelligent algorithms, including evolutionary computation and fuzzy control to precisely gain control over physical quantities, such as location, speed, temperature, pressure, etc., in the feedback control systems by integrating the characteristics of controlling the machines.
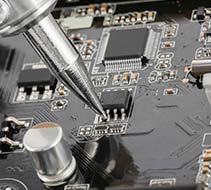
Algorithms are “engraved” into the specialised chips using SOC techniques, such as parallel, real-time and minimum resource processing. The specialised SOC chips with technology for the blown film equipment from independent research will finally be able to be obtained, says Jinming.
According to statistics presented by Jinming, China is the biggest market for mechanical equipment in the world. It says that a large number of plastic machinery equipment is still imported by China due to the lack of core technologies, including control systems. Almost 10,052 plastic machines were imported in 2013 at a cost of US$1.82 billion while 135,213 machines, with a value of US$1.72 million, were exported.
Hence, Jinming says it is working towards bridging the technology gap with its R&D centre and tie-up with the university to develop new technologies in China.
(PRA)