Also, download this story from the electronic issue here
Healthcare needs are becoming more sophisticated. Luckily, R&D in the medical industry has kept pace with advancements to spot new applications for materials, says Angelica Buan in this report.
Provision for healthcare remains the top priority of individuals as well as nations. The Asia Pacific healthcare spending is projected to reach US$2.2 trillion by 2018 at 10.5% CAGR, as stated by Frost & Sullivan. Globally, per capita spending for healthcare is outpacing per capita income. By 2050, healthcare spending would have accounted for 20-30% of the GDPs of many countries.
Industry analysis indicates that the trend is going towards simplified and frugal innovations. Even so, these require ongoing R&D for technologies to simplify healthcare processes and tools, such as the utilisation of polymers to reduce the weight and add on flexibility or a soft-feel coating for accessories, without compromising important features like durability and sterilisability
Medical polymers have a healthy growth
The market for medical polymers is projected to be valued at US$17.13 billion by 2020, reaching a CAGR of 8.3% from 2014, according to Transparency Market Research. Polymers, categorised as plastic resins/fibres and elastomers, are widely used in implants and devices, diagnostic systems, and hospital accessories.
Medical devices and equipment lead in the area of applications, accounting for a share of over 47% of the overall volume in 2013, due to high demand for disposable medical equipment. Rapid growth is also expected in medical packaging, due to increasing demand for lightweight, safe, and easy to transport packaging.
Capable of replacing metals or glass as primary material for a wide range of medical products, polymers’ unprecedented growth in this segment may be impeded by safety regulations becoming more stringent.
Meanwhile, Nanomarkets in its research says that medical polymer manufacturers are required to follow stringent manufacturing technology processes in all stages of production, including storage. They must also control the quantity, quality, molecular characteristics, and leaching properties of all of the materials used to produce the polymers, as well as ensure biocompatibility and compliance with region-specific regulations.
Furthermore, other impediments cited by Transparency Market Research include price fluctuation of raw materials (affected by crude oil prices), which impacts prices of polymers and that could lead to shortages and price increases.
Nevertheless, new breakthroughs in polymers for medical applications continue to outweigh the stumbling blocks to its market growth, considering that polymers’ versatility stretches its applications beyond conventional medical devices.
Exploring biocompatibility use
In medical implants, biocompatibility of polymers is fundamental. A recent innovation on biocompatible polymers will be utilised to render efficiency in medical sensors.
Dr Gang Cheng, Assistant Professor of Chemical Engineering at the University of Akron, has embarked on developing a polymer coating for medical sensors implanted in the body. The research has reportedly attracted a five-year grant amounting to US$499,995 from the National Science Foundation in the US.
Cheng is studying the structure and function of water-soluble polymers that are safe to be put in the body and that also conduct electricity.
The research involves polymer-coated sensors to monitor biomarkers, such as blood sugar, around the clock. The sensor, paired with a drug-delivery system, could trigger doses of medication when needed. The polymer also could be used on pacemakers and other more sophisticated implanted devices that must communicate with the body.
The ongoing research is initially focused on constructing polymer-coated sensors to test in the laboratory. Other applications for biocompatible conducting polymers could include biofuel cells, which turn the sugars in the body into energy, and may be viable to replace batteries to power implanted medical devices.
In a related development, researchers at the Fraunhofer Institute for Interfacial Engineering and Biotechnology IGB in Stuttgart, Germany, have developed a cell-free substrate made of advanced fibres consisting of synthetic and biodegradable polymers such as polylactide (PLA).

Regenerative medicine uses cells harvested from the patient's own body to heal damaged tissue. The cell-free substrate contains proteins to which, autologous cells bind and grow only after implantation.
This development is an important milestone in regenerative medicine. Usually, the only treatment option for patients who have damaged internal organs or body tissue is either rely on donor organs or synthetic implants. However, the body is likely to reject this transplant, while implants based on autologous cells are more likely to be accepted.
The Fraunhofer researchers are working on a project to develop suitable substrates – known as scaffolds – in collaboration with the university hospital in Tübingen and the University of California (UCLA), in Los Angeles. Their solution is based on electrospinning, a process in which synthetic and biodegradable polymers such as PLAs are spun into fibres using an electrical charge to create a three-dimensional nonwoven fabric.
Proteins are added to the polymeric material during the electrospinning process. The material serves as a substrate to which the patient's own cells will bind after it has been implanted. The polymeric fibres during this process will gradually degrade in the human organism over a period of approximately 48 months.
The hybrid materials composed of polymeric and protein fibres can be produced and stored in large quantities. The IGB team is working to bring the novel substrate to market as a rapidly implementable alternative to conventional heart valve replacements.
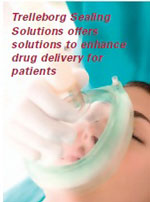
Efficient drug delivery systems
Optimising efficacy of medications starts with getting the drugs to their targets in a controlled manner.
Trelleborg Sealing Solutions, a manufacturer of precision seals and bearings, introduced its engineered innovations to address what it observes as today’s demand for smaller and more discreet devices.
Showcasing its range of products at the recent International Pharmaceutical Expo held in New York, Trelleborg zeroed in on drug delivery, such as insulin inhalers, prefilled syringes, infusion pumps, intrauterine devices, single-use bio process bags and other drug-device combination products.
The firm said that drug delivery devices complement the influx of new drugs being granted patents and new pharmaceutical companies entering the market. Accuracy of drug delivery and user experience are top considerations of pharmaceutical companies for these devices, it said. Lowfriction material combinations play an important role in addressing this requirement.
Trelleborg says that it can help customers reduce overall component size and weight of their drug delivery systems and leverage efficient disposable devices. With thinner sections and fewer components, mechanical demands on individual components have heightened, resulting in greater use of high-performance engineered polymers.
Life-saving injectables
Researchers at the University of Washington have developed an engineered hemostatic polymer (PolySTAT) that circulates innocuously in the blood, identifies sites of vascular injury, and promotes clot formation to stop bleeding.

Promoting blood clotting often involves the use of human platelets. This option is expensive, not to mention that the platelets have a short shelf life and may not be readily available in some cases.
PolySTAT is administered via a simple injection and is being eyed for its potential to treat injured soldiers on the battlefield. After successful clinic trials on small animals have been carried out, the injection could be ready for clinical trials on humans in five years, according to the researchers.
Why PolySTAT is suited for treating combat casualties is because most patients die from uncontrolled bleeding. A natural protein found in the body called Factor XIII, responsible for binding fibrin strands together, helps strengthen blood clots. PolySTAT works in the same way but additionally safeguards degradation of blood clots, since the natural enzymes that cut fibrin and dissolves blood clots do not target the PolySTAT bonds.
The study further showed that he polymer strengthened the clots even when the levels of fibrin were critically low. Moreover, PolySTAT does not form clots in the body that can result in a stroke or embolism as it only binds to fibrin at the site of a wound.
(PRA)