Also, download this story from the electronic issue here
China continues to play a prominent role in the global flame retardant chemical market in terms of production, domestic consumption as well as direct exports, and is expected to lead in global market growth.
Locally produced phosphorus flame retardant (FR) chemical is gradually replacing previously popular halogen-containing chemicals in a broad range of applications, particularly in the plastics and rubber sector. Consumption of inorganic FR is also on the rise.
Currently, there are five key product types being used in China: phosphorous, brominated, inorganic, chloride and other types of FR chemicals. The majority of fire retardant chemicals used in the plastics and rubber industries act as important additives to PP, PE, PU, engineering plastics for automobile and electronics, as well as flexible PVC. This is closely followed by the electrical & electronics, chemical (mostly coatings), and electric wire manufacturing industries. Other key applications of consideration include chemical, textile, wood processing, paper and more, though the size of demand is relatively low in these sectors.
Market overview
GCiS China Strategic Research estimates that the domestic market for FR chemicals in China is valued at nearly RMB6.8 billion or roughly US$1.1 billion, as of the year end of 2014, up by 5.9% over 2013. Roughly 700,000 tonnes of FR chemicals were produced in China in 2014 and roughly 400,000 tonnes were consumed domestically.
GCiS observed a tremendous increase in production over the years, especially for phosphorous FR. The largest two domestic companies – who manufacture exclusively phosphorous FR – have listed themselves on the stock market to acquire sufficient financial support needed for capacity expansion.
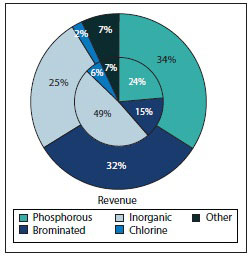
China is a net exporter of FRs, and of the estimated 700,000 tonnes of FRs produced domestically, it is estimated that nearly 30% was shipped abroad/exported.
For both phosphorous and brominated FRs (such as DBDPE and TBBPA which are still permitted), the largest export markets are the US, EU, South Korea and Japan. In addition to the raw export of FR, significant amounts of FRs are exported via the sales of domestically manufactured final products, such as cable, wire, plastic products, and electronics.
Of the approximately 400 suppliers active in the domestic market for the target products, 16 can be classified as “large” suppliers, with revenues in 2014 of over RMB100 million (excluding exports). The vast majority of suppliers (around 300) are defined as “very small” companies, with FR revenues in 2014 that were less than RMB5 million. These companies typically manufacture inorganic FR as their main product.
Top suppliers in the China market include: Albemarle Corporation, Jiangsu Yoke Technology, Shouguang Weidong Chemical, Zhejiang Wansheng, Clariant, Hsikwangshan Twinkling Star (Hts), Jinan Taixing Fine Chemicals, Chemtura and Sino-Brom Compound (ICL).
Environmental concerns
Both domestic and overseas fire retardant standards and environmental regulations are the driving forces behind this trend. However, notwithstanding the optimistic expectations of industry participants, weak law enforcement and supervision in China may hinder this transition.
Halogen-based FRs have the best polymer compatibility and are considered to be the most effective type of FR. However, this types of FR poses certain environmental and health concerns. In some end-user industries where FR requirements are more rigid than others, such as cable wire and electronics, it is difficult to completely substitute halogen-based FR for other types of FR.
While phosphorus FR is not superior to halogen-based FR in terms of fire-resistance efficiency, considering trending concern for environmentally friendly products, the scope and quality of non-halogen products available in China (phosphorus, inorganic-zinc compounds, aluminium hydroxide, magnesium hydroxide), its product technology maturity, as well as its availability and pricing, it is anticipated that phosphorus FR has the strongest potential for growth.
Raw material resources are more available in China for phosphorus FR, and technology for this type of FR has been mastered by the domestic companies. Most of the Chinese end-user industries are not yet ready to accept the much more expensive but better performance inorganic FR offered by foreign suppliers, and presently there are no domestic suppliers capable of producing FR that can match foreign quality. To compensate for this, large amounts of low quality inorganic FR manufactured by domestic suppliers are needed to be added to the plastics in order to achieve the same results as other types of FR. However, this can worsen the mechanical and electrical properties of the plastics.
Biobased FRs
In relation to environmental concerns, developments are underway for biobased flame retardants, which are both renewable and non-halogenated, in developed markets.
In China, biobased FR is still at the research stage. Institute of Chemical Industry of Forest Products has recently developed and tested biobased flame retardant polyester polyols in which the content of renewable raw materials ranges from 40-50%. This being said, for the market in China, it is still a long way to go for biobased FRs to have any substantial and commercial deployment.
In China, phosphorus FR is considered a superior option to replace halogen-based FR, and leading domestic suppliers R&D remains in the area of increasing phosphate content and providing customised FRs for engineering plastics, PCB, and PU foams.
Recent regulation development in China still focuses on mandating flame retardant standards to be implemented by different downstream products, like insulation materials. Areas such as foam cushions in furniture are still void of inflammability standards.
There is virtually no regulation in China with regards to FR’s impact on the environment and human health, with the exception of banning PBB and PBDE usage in electronics products sold in China.
Non-halogenated FRs are mostly adopted by multinational companies in China following global production and safety standards or manufacturers that export, following regulations such as RoSH and REACH in the EU and California proposition 65 in the US.
This explains the slow progress of non-halogenated products substitution but also indicates a large, as yet untapped potential in the Chinese FR market to be exploited in the future. With government starting to tackle environment issues on all fronts, we are optimistic about forthcoming standards and legislations to drive the market towards an eco-friendly direction.
Going forward
The domestic market will grow from RMB6.8 billion in 2014 to around RMB9.1 billion by 2019, with more evident trend of phosphorous FRs replacing brominated FRs to become the largest product segment by value.
The market for FRs as a whole is growing at a rate slightly lower than GDP and GCiS expects that the plastics and rubber industry will remain the largest consumer of FRs in upcoming years.
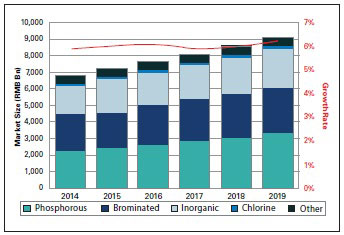
Pointing to an increasing demand for more advanced engineering plastic products as well as plastic products as a whole, experts from inside the plastics industry are highly optimistic about industry growth.
The proportion of flame retardant added to plastic products in China is significantly lower than that of other mature markets, which presents another potential for growth, provided regulations are tightened.
Going forward, phosphorous FR will be used more frequently, especially in the manufacturing of PU, flexible PVC, PP, PE and other plastic products. Note that compared to phosphorous FR, brominated FRs are still used more frequently for the manufacturing of general purpose plastics such as PVC and PP, which are intended to be sold domestically given the Chinese government’s lower requirements on fire retardant standards.
Brominated FR is still preferred because of its high fire retardant capability per unit count. But, in terms of performance, advancements to the production and product technology of phosphorous FR will gradually solve this problem.
On the other hand, downward pressure is being placed on the industry coming mainly from the rubber industry, where due to anti-dumping policies, the export of rubber has been prohibited. Additionally, shrinking profit margins caused by increasing manufacturing costs will also slightly compromise demands for FRs in this downstream vertical segment of the market.
(PRA)