Also, download this story from the electronic issue here
At the upcoming Chinaplas show in Guangzhou, thermoforming machine makers will showcase a variety of machinery and technology updates.
Meaf Machines claims its sheet extrusion lines for film and sheet reduce energy consumption by up to 50% compared to competitors. Its H-series achieves this through a combination of a screw and barrel design, utilisation of heating and cooling in combination with IE2/3/4-class motors. Another important feature is the low RPM’s required (less than 200) and achieving high outputs with high ratios of regrind.
Coupled with this is the inline KMS600 thermoforming machine. Major advantages for working in-line include the ability to directly feed the hot sheet allowing for constant quality; cycles/minute are higher than with a traditional offline system due to direct feeding. Furthermore, the Dutch machine maker says that continuous production results in less waste material (for example – eliminating the need for side trims) and the closed-loop grinding, filling and dosing system ensures less foreign materials and dust will enter the production process. In human resources, operating in-line requires less operators than producing with two separate lines, thereby saving labour costs.
The KMS600 is equipped with tilting technology and allows the production of cups up to 180 mm across the entire form area. Optional features include a servo driven plug assist, fully automatic lubrication system for all major parts, with individually controlled heating zones in lower heating frames as a standard.
Germany-based Illig Maschinenbau will be presenting its RDK and RV series. Trays and hinged packs, used for protection of food during transport and as sales packs, are produced on these thermoformers from thermoplastic roll stock.
At the show, hinged food packs will be manufactured on an IC-RDK 80 thermoformer out of APET, with a maximum forming area of 756 mm x 565 mm. Equipped with a ten-up mould, the line is able to reach a speed of up to 50 cycles/minute. With the new IC (Intelligent Control Concept), the servo-driven thermoformers can be utilised to the full extent, with RDK machines reaching speeds up to 55 cycles/minute. These machines work in the forming-punching method.
Illig will also show the RV 53d, featuring a forming area of 500 mm x 350 mm and speed of 50 cycles/minute. As a rule, a user can build moulds by using a system of standard parts available from Illig.

Italy-based Amut Group will present in operation the VPK-C84 automatic thermoforming machine for producing rigid packaging, such as trays, punnets and containers.
The 25-tonne VPK-84 is composed by three stations: forming, steel rule die cutting and stacking, with a forming and punching area of 840 x 650 mm and a dry cycle of 45 cycles/minute. It is a fourcolumn forming and cutting press. The upper and/or lower plugs are operated by servomotors; forming is undertaken with compressed air and/or vacuum, while a quick clamp system is used for forming and punching mould, cutting and stacking tools.
Large vacuum former
Swiss company WM Wrapping Machinery has supplied a large vacuum-pressure forming machine to a Brazilian company near Sao Paolo. The FC 1000 IM Speedmaster Plus has a forming area of 1,060 x 750 mm and a clamping force of 130 tonnes. WM has increased by 40% the clamping force in order to reduce at minimum the deflection off the platens and have less wear of the steel rule knife, with consequent better stability of the process.
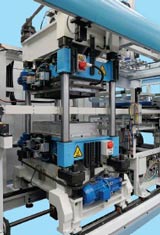
Forming and cutting operations are simultaneously operated in the same mould by an incorporated steel rule cutting blade. The in-mould cutting makes possible a high accuracy of the peripheral size, improving the quality of the final product. Installed on the upper platen of the machine is a third motion servo-driven plug assist unit, and programmed pre-stretching can be performed for better distribution of the material, improving the stiffness and reducing the final weight.
The stacking and counting of the thermoformed products, after forming and cutting, is undertaken by a three-axis robot including the A-B-C stacking possibility. The machine is equipped with latest generation software while a B&R PLC, equipped with a colour touchscreen control keyboard, is fitted on a sliding arm and moves right along the operator side of the machine.
The system includes a cycle self-setting processor. By keying in the type of material processed, the thickness and type of product, as well as the width and pitch of the sheet, the software automatically provides the basic settings for the ideal forming cycle and for the machine operating functions, from heating through stacking. The system can also store all the data and information already set on a USB memory stick and an Ethernet port allows the connection of the machine to one or more computers through the company network as well as to the printer, as standard equipment.
All WM Speedmaster thermoforming machines also use the integrated power regeneration. The kinetic energy generated during braking movements is converted to electrical energy, which is restored into the power system of the machine for energy savings.
Copolymer for transparent PP parts results in benefits
A new study released by CMT Materials, a US-based plugassist materials supplier for the thermoforming industry, reveals that syntactic foam plug assists deliver greater performance benefits than solid polymer plug assists for thermoforming of transparent PP parts.
While measuring the influence of different plugassist materials, CMT says it found statistically significant improvements in haze, material distribution, and crush strength for thermoformed PP parts, which utilised syntactic foam plug assists. Plug surface quality that was affected by machining and polishing techniques was also identified as a critical factor.
CMT’s Hytac C1R is a toughened copolymer thermoset syntactic foam modified to provide high friction. It is said to be easy to machine, durable and easy to modify/polish. Relatively new to the market (introduced in 2012), it was initially used for deep draw or zero draft application areas where high friction was needed. Now, CMT has discovered that C1R offers benefits beyond deep draw.
Thermoforming trials with 1.39 mm-thick PP sheet, clarified with Milliken Chemical’s Millad NX 8000, were run at uVu Technologies to determine if CMT’s C1R copolymer could provide all the benefits of syntactic foam without any loss in optical properties compared to solid polymers such as PEI and acetyl.
The formed part was a 89 mm tall cup with a rim inner diameter of 66 mm and a bottom diameter of 51 mm, resulting in a draw ratio of 3.4. Hytac-C1R resulted in cups with 20% lower haze compared to PEI. Forming cups with C1R instead of PEI also resulted in a 10% increase in cup weight. In addition, cups formed with C1R weighed 3% more than those formed with acetyl, says CMT
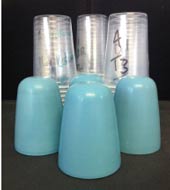
The high-friction copolymer base maximises the ability to pull sheet material into the tool compared to other plug materials, according to CMT that also says it increased the minimum sidewall thickness by 28% compared to PEI and 20% compared to acetyl. For thermoformers, part thickness is related to crush resistance.
The increased cup weight and minimum sidewall thickness obtained with Hytac foam resulted in 31% higher cup crush strength compared to plugs made from PEI. Ultimately, CMT says its copplymer resulted in equivalent or improved optical properties compared to PEI and acetyl while improving material distribution and leading to stronger cups.
(PRA)