Also, download this story from the electronic issue here
Bottled water is forecast to have sales that would exceed that of carbonated drinks, says research company Canadean. The role of packaging in delivering safe water from source to end-user, as well as other beverages cannot be undermined. Provider of PET solutions for liquid packaging Sidel says it matches the requirements of the global beverage industry. The Hünenberg, Switzerlandheadquartered company has 40 years of aseptic packaging expertise, and was one of the first to introduce PET bottles over 30 years ago.
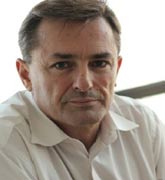
A grail of packaging options
Ensuring safety of beverages requires stringently produced packaging. According to Sidel, it assures compliance with food safety standards, as well as “strong ethical, good corporate governance and the right environmental and sustainability approach”. To date, it has installed around 30,000 machines in 190 countries.
The Asian region is important for Sidel, specifically the Southeast & Asia Pacific (SEAP) geographical zone. Its Asian head office is in Bangkok, Thailand, and it operates in six operational subzones: IND (India, Bangladesh, Bhutan, Maldives, Nepal, Sri Lanka), TCM (Thailand, Cambodia, Myanmar), IMS ( Indonesia, Malaysia, Singapore), JKK (Japan, North Korea, South Korea), VLP (Vietnam, LAO PDR, Philippines), and Oceania (Australia, New Zealand, Papua New Guinea, New Caledonia, Fiji and other Pacific countries).
It also operates through nine locations in the main countries, plus has a blow moulding machinery facility in India.
PRA interviewed Dominique Lipinski, who assumed the post as Zone Vice-President SEAP early this year. The Bangkok-based executive will be celebrating his 22nd year with Sidel.
PRA: What are the latest offerings from Sidel for the Asian market?
Dominique Lipinski: We are continuing to develop and evolve our new Sidel Matrix modular approach to PET bottling equipment. It is a broad, proven and upgradeable system that is our most powerful solution yet in terms of performance, flexibility, cost savings and sustainability. It ensures product safety and quality with a very high standard of hygiene. It features optimally proportioned equipment configured to provide increased production capacity for various beverages, to meet the growing demand in world consumption.
Through our strategy of global experience, backed by local sales and service support, we are constantly looking at how we can invest to further support our customers in their respective markets. We are continuing to focus globally on PET as the most sustainable packaging material of choice. It is strong, shatterproof, lightweight, transparent, safe and, importantly, recyclable, with an inherent barrier, which makes it particularly suited to a wide range of food and beverage applications.
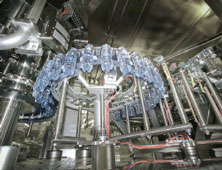
Almost 56% of the world’s population live in the Asia and Pacific region. The continuing importance of China and the Asia Pacific region was reflected in the decision to hold the fourth KNOWLEDGEshare Live series of beverage industry events, hosted by Sidel, in Chengdu, China, in March. Almost 500 participants from all areas of the beverage supply chain attended. As well, KNOWLEDGEshare is also an online forum (www.knowledgeshare.com).
Japan is another important market in our SEAP zone. Sidel Japan has recently celebrated its tenth anniversary. A notable recent project saw Sidel supply a PET bottle blowing line, featuring Sidel Predis, a dry preform decontamination system, to a major Japanese manufacturer of pharmaceutical water. The product is based on scientific research into how drinks containing electrolytes can help supply nutrients, based on the concept of intravenous hydration.
PRA: Are there new trends in PET packaging or new beverage packaging technologies developed for the Asian markets?
Dominique Lipinski: One of our most recent technological innovations is Intelliblower, a significant innovation that brings control and self-regulation to the blow moulding process. The patented technology ensures greater accuracy in distribution of material during the production of individual bottles, with the elimination of inconsistencies resulting in improved quality, regardless of bottle weight.
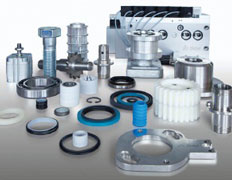
The blow moulding process is becoming increasingly important as the drive for ultimate lightweighting of PET bottles within the industry continues. Poor or irregular material distribution within the production of bottles can adversely affect quality throughout the entire process and can even lead to a total shutdown of the line. Because the appearance and handling of the bottle is what ultimately affects how any brand is perceived, Sidel is continually striving to create quality and performance possible in PET bottles.
PRA: Are there challenges that Sidel has encountered in the Asian markets in the past year?
Dominique Lipinski: One of the characteristics of the Southeast Asia Pacific region is the importance of “sensitive” beverages such as juice and milk products, an importance which is growing as consumers look for healthier beverages. Indonesia is a good example of this, following the current global trend of more healthconscious consumers, a trend that is set to continue, with younger people. Dairy products, such as drinkable yoghurts, are already one area that has been positively influenced by the emerging trend, with single-serve, “on-the-go”, rigid plastic formats performing particularly well.
Sensitive products present particular challenges in terms of ensuring product safety. Our Sidel Predis replaces wet bottle sterilisation. It provides 100% decontamination of all preforms using hydrogen peroxide mist, removing the need for water and requiring only small amounts of chemicals. It protects the integrity and safety of any beverage, either high or low acidity, distributed at ambient temperatures.
With the Sidel Combi Predis FMa, the preform decontamination, blowing, filling and capping functions are housed in a single production enclosure. Predis enhances production flexibility and helps to protect liquid packaging from micro-organisms, preserving sensitive drink integrity and lengthening shelf life.
PRA: What are the growth markets in the coming years?
Dominique Lipinski: There is potential for growth throughout the region, with PET offering excellent opportunities for material substitution.
One of the major contributors to a country’s growth potential in terms of beverage consumption is the size of the population and whether it is increasing or declining. In 2010, India represented 30.8% of the world’s population, a figure that is projected to continue to increase with India anticipated to become the most populous country in Asia, and therefore the world, around 2020. Over half of India’s population are less than 25 years old, which represents opportunities for greater adoption of new trends and developments in packaging, such as the single-serve formats that are becoming increasingly popular.
PRA: What can we expect from Sidel SEAP in the future?
Dominique Lipinski: The focus on our R&D programmes is ongoing to ensure that we continue to meet the needs of customers today and tomorrow, recognising emerging trends and providing the solutions to meet them. For example, there is a shift away from a reactive approach to a much more proactive one, undoubtedly helped by the technology that is increasingly being implemented in bottling lines. One of the characteristics of today’s equipment is that it is much more intelligent, with “black box” devices providing wide ranging data that can be invaluable in helping to automate, for example, some of the maintenance functions. This has led to the adoption of processes such as Total Productive Maintenance (TPM), which combines three elements: autonomous maintenance, in which operators are trained to handle minor repairs and maintenance; preventive maintenance which is about taking proactive measures; and continuous improvement based on hard data analysis.
The data available from today’s modern production lines, including the potential for remote analysis and proactive services from the equipment manufacturers themselves, provides opportunities to optimise the services function. By taking data from multiple sources, it is possible to become predictive about line conditions, quickly forming conclusions about what is happening, what could happen and what actions to take to continue positive or improved performance. This allows for the provision of support, trouble-shooting and analysis in real-time, detecting or preventing errors and optimising performance.
(PRA)