Italian firm Piovan says the engineering of a system for the use of rPET as a main raw material in the processing of car interior parts represents one of the latest challenges since it requires specific technical competences as rPET is amorphous, dusty and comes in variable granule sizes.
With this in mind, Piovan has developed a solution with features such as a crystallising, dehumidifying and dosing with a capacity of up to 1,200 kg/hour postconsumer PET flakes and up to 1,600 kg/hour in the case PET granules are used.
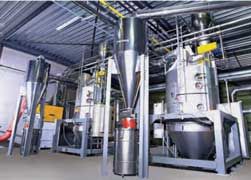
Such large capacities do not facilitate the management of production changes or small production lots. In order to avoid material waste and long machine down-times, Piovan developed a solution characterised by a double dosing process and two separate parallel columns for crystallisation and drying. This allows the user to switch from processing rPET flakes to PET granules and to vary the percentage of the recycled material to a large quantity of PCR flakes without altering the overall efficiency of the system.
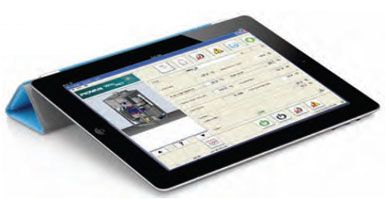
The firm’s patented gas chambers heat up process air for the crystallising and drying systems, said to be convenient in applications in the installation site where the price of natural gas is much lower than that of electricity. The entire production process can be managed via Piovan’s supervising software WinPET. From a remote PC workstation, it is possible to adapt the production automatically to the different types of materials, depending on densities and capacities, thus, optimising energy usage and avoiding any waste, according to Piovan. The firm also adds that reduction of the raw material and running costs equates to consequent reduction of the production costs.
Producing finer granules and no breaks in strand
pelletising
By streamlining the operation of its Purging Recovery
System (PRS), US-based Maguire Products says it has
increased output by 20% and production of finer and
more uniform granulate with less dust.
In the PRS, material undergoes two stages of size
reduction. First, a rotor planer slices or planes the rocklike
purging into small chips. Second, a granulator
reduces the chips to regrind. Maguire says the knives
in the rotor planer are now 40% smaller and it has
added on four more knives to total 12. As a result, the
planer produces smaller chips that are more easily
size-reduced by the second-stage granulator. The
cutting chamber of the second-stage granulator has
been redesigned to increase the flow of air generated by a blower. The material in the granulator, thus, is
cooled more effectively, preventing melting, and it is
evacuated from the cutting chamber more rapidly, says
the supplier.
Finer granulate is also produced, with minimum hole sizes in the screen of the second-stage granulator reduced from 9.52 mm to 6.35 mm. Plus, Maguire has replaced the previous one-piece screen with a three-piece screen that is easier and less expensive to replace.
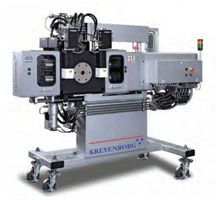
Three years ago, Germany-based Kreyenborg installed its V-type screen changer in a recycling plant with strand pelletising. The processor mainly processes PS and PP film remnants, which contain a high level of contamination. Despite the high mechanical demands on the system technology, there are no signs of fatigue after more than 51,000 backflush cycles, says Kreyenborg.
One cycle comprises the flushing of all four screen cavities, of which there are three in production (patented 75% technology). An overhaul due to rework or wear of the seals is not necessary when using a piston screen changer because there is no leakage. The screen changer makes more than 100 backflush cycles with the same screen pack. Then the screens are changed for security reasons in order to avoid fatigue of the mesh. The purpose of these preventive measures is to prevent the bypass of dirt particles around the boundary edge of the screen packs. If and when the screens need to be changed, the replacement of the screen packs is very simple. Kreyenborg also says that strand breaks are things of the past when using the V-type, due to the constant pressure of the machine.
New line for recycling high moisture-content waste
Italy-based Union has a new line for the recycling of
waste. The 2,000 kg/hour- line has a simple operating
principle: the heterogeneous material, with a moisture
content of up to 30%, is fed, via a conveyor belt
equipped with a special comb, which regulates its
flow, into an agglomerating machine. This has a large
plasticisation unit with large-diameter rotating screws.
The speed of the conveyor belt, and thus the flow rate,
are kept constant by a control system located on the
engine.
Inside the plasticising unit, the material is submitted to mechanical friction and heating, which reduces its high moisture content and increases its density. Once molten, the material flows directly into a special extruder; from there it flows through the continuous, self-cleaning screen changer before being sent, finally, to the die-face pelletiser to be turned into pellets.
(PRA)