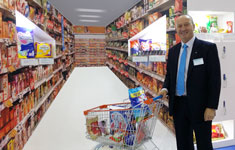
Polyolefins maker Borouge expects its growth in India to come from products that are not made in the country. This is the observation of Laurence Jones, Vice-President for Film and Fibre, who was interviewed at the February Plastindia show in Gandhinagar, Gujarat.
″The GDP growth is higher in India, compared to China, because of the expanding middle classes who have spending power. We have a lots of confidence from the growth of our products, which we expect will grow at a pace higher than the GDP in India,″ according to Jones.
It was promoting solutions for the advanced packaging, baby care and toy markets at Plastindia. New to the Indian market is the BD265MO high impact block copolymer offering impact resistance and no break properties at room temperature, which is also FDA-approved for food and child contact applications. With the Borstar Nucleation Technology (BNT), it allows for property balance, and cycle time reductions of up to 20%.
Meanwhile, the RJ766MO is the latest addition to Borouge‘s high-flow random PP family, which combines transparency and high flows with organoleptic performance, for transparent packaging and houseware applications.
To cater to the industry trend of moving away from the use of PP to PE for caps/closures (carbonated and non-carbonated beverages), due to the non-sealing requirement, Borouge also introduced BorPure MB5568 and MB5569 HDPE grades. ″The heart of this innovation was to support the beverage industry’s adoption of lightweight and short-neck closures (PCO1881) that bring savings for the total packaging,“ said Jones.
Other new products geared towards India include ready-made black PE compounds, Aquility HE3408 and HE3406, targeted at drip irrigation pipes, which are vital for India’s agriculture sector.
A joint venture of the Abu Dhabi National Oil Company and Austria's Borealis, Borougebuilds its products on its Borstar (for PE and PP) and Borlink technologies.
To date, the UAE-headquarteredBorouge has invested more than US$10 billion in a 700% increase in the production capacity of its petrochemical plants in Abu Dhabi from 2 to 4.5 million tonnes/year, since 2010. It is now in the process of phasing up Borouge 3, which in addition to increasing the capacity of PP (480 kilotonnes) and PE(550 kilotonnes) production, will also introduce LDPE to the company’s portfolio, targeting the global wire and cable markets.
“It is nice to be in a rapid growth stage,” said Jones, adding that the first shipment of Borouge 3 material was exported through the container terminal at Khalifa Port last year.
While the plants are located close to feedstocks, Jones adds that logistics is the biggest challenge. Hence, last year the company partially launched its new packaging facility at Khalifa Port that was designed and built by Abu Dhabi Terminals to pack Borouge’s products ready to export to customers.
When asked if Borouge had any new developments in store, Jones added, “We are working on how to bring tougher films to the market, but with less material use.” The company is developing a new three-layer cast PP/PE film together with beverage companies like Pepsi and Coke. “Using our Borstar technology, we will be able todowngauge the film from 80 to 60 or even 40 microns,” said Jones, adding that the company is trialling the combo PP/PE film that will be rolled out next year.
“Processors will be able to realise real material savings while transporters will find less failures and less damage during transportation.“The goal, adds Jones, is to reduce polymer usage while improving the features.
(PRA)