Blow Moulding: Emergence of new technology
Also, download this story from the electronic issue here
Against the backdrop of the growth of the beverage market, with the shift from developed to emerging countries, continued investment in development of innovative drinks and value-added propositions that respond to changing consumer lifestyles and demographic changes, are driving the blow moulding machinery sector.
By 2021 Asia is predicted to contribute two-thirds of global incremental beverage consumption, with China alone responsible for one-third of the additional volume, according to research firm Canadean’s most recent Global Beverage Forecasts report.
In terms of the top ten incremental volume providers by 2021, China and India will dominate, followed by Brazil. With the exceptions of the US, Saudi Arabia and Mexico in sixth, eighth and ninth positions respectively, all other markets in this group (Indonesia, Pakistan, Thailand and Vietnam) are Asian.
Soft drinks, particularly packaged water and bulk/ home and office delivery (HOD) water, will be the primary driver of incremental volume growth across all these markets, underscoring not only the growing global health trend, but also the opportunities offered by the lack of good quality tap water in many emerging markets.
Meanwhile, French maker of blow moulding machinery Sidel says the beverage market in Thailand has remained strong over the past few years, with juices, nectars, soft drinks, isotonics and teas (JNSDIT) and liquid dairy products (LDP) performing particularly well, achieving sales of 7 billion units and 8 billion units respectively in 2015. Growth forecasts for the country in these two categories are also the biggest, with a CAGR of 6% for JNSDIT and 4% for LDP from 2015-2019.
New packaging designs
In terms of new packaging designs, Canadian company Nova Chemicals and Switzerland-headquartered Tetra Pak collaborated to produce the world’s first aseptic carton bottle for ambient white milk in 2011. They have now developed the latest generation Tetra Evero Aseptic utilising Nova’s Surpass HPs667-AB PE resin, with oxygen barrier properties, making it possible for Tetra Pak to expand beyond ambient white milk to enriched dairy alternatives, flavoured milk, toddler and baby milk in the award-winning carton bottle.

Produced with Nova’s Advanced Sclairtech dual-reactor process and single-site catalyst, HPs667-AB is a bimodal homopolymer, six-melt index, 0.967 g/cc PE resin. The material reportedly offers excellent barrier and stiffness performance, which helps converters and brand owners improve the sustainability of packaged goods in a wide variety of applications, including cereal, crackers, dairy and other liquids.
Meanwhile, the aseptic packaging structure combines the body of a liquid carton made of a paperboard sleeve, with the handling and pouring advantages that come with an injection-moulded top and cap. The patented filling system for aseptic carton bottles developed by Tetra Pak, the A6, takes up 50% less space than a PET packaging line. The package is sterilised in the aseptic chamber through pre-heating, then treated with hydrogen peroxide gas, and finally ventilated with sterile air to eliminate all the gas in preparation for product filling.
In other news, Sidel worked with Brazilian packaging provider Algar Agro to reduce the weight of a bottle by 22%, from 18 to 14 g. Sidel says it put together proposals for the bottle's packaging optimisation and carried out feasibility tests for the new design at its Packaging & Tooling Centre in Guadalajara, Mexico.
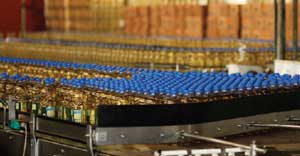
With the acquisition of two Sidel Matrix blowers - one at each of its production plants - Algar Agro believes it is the first oil producer in Brazil with integrated injection and blowing in its PET production process. The Sidel machines were installed in bottling lines producing 25,000 PET bottles/hour for vegetable oil.
Blowing with liquid instead of air
In 2014, partners Sidel and Australia’s packaging giant Amcor, collaborated on LiquiForm, a breakthrough blow moulding and filling manufacturing technology that uses consumable, pressurised liquid instead of compressed air to form plastic containers.
The LiquiForm Group has since then signed agreements with Yoshino Kogyosho, Japan’s largest plastic bottle manufacturer, to further develop the technology, and with Nestlé Waters, one of the world’s leading bottle water companies, to acquire the intellectual property.
Benefits include a significant reduction in the energy for bottling achieved by eliminating the need for compressed air. For standard blow moulding, the air compression cycle is only 35% to 40% efficient and consumes approximately 70% of the total amount of electricity used in the blow moulding process. The LiquiForm process requires a smaller footprint, compared to standard bottle making and filling operations that are typically performed by two separate pieces of equipment. Furthermore, the process optimises PET bottle design both in terms of lightweighting and potentially sharper bottle definition (because better pressure control and material distribution is possible with liquid instead of air which allows for minimum wall thicknesses).

The technology has been validated with a significant range of packaging substrates, products and conditions using the same LiquiForm machine for cold, ambient, and hot-fill PET containers. It is expected that more equipment manufacturers and FMCG companies will soon be able to purchase “developer kits” to accelerate their own product development, says the company.
Machinery makers target automotive sector
With the global demand for plastic ducts for the automotive sector rising, since the use of special materials such as PA6.6 or PPS has enabled the production of highly heat-resistant exhaust ducts, it is no surprise that machine makers are targeting this sector.
Germany-based Kautex Maschinenbau presented its third generation KCC series, which has been produced at its plant in Shunde, China, since 1997, at the recent Chinaplas show in Shanghai. The model has been completely re-designed and also features 50% less space. Moulds can now also be changed from the side, for example, and products are discharged from the rear of the machine. A standardisation of modules and components has reduced the investment costs of the new machine and shortened future delivery times, says Kautex.

Compatriot Bekum, which has to date delivered 16,000 blow moulding machines worldwide, has reorganised its plants in Germany and Austria. It invested EUR5 million to move its production division, which includes machine assembly, shipping, procurement, work preparation and warehousing, to Traismauer (Austria), about 60 km from Vienna. The aim was to consolidate the European manufacturing of extrusion blow moulding machines at a single site. While previously only large machines were built at Traismauer (established since 1968), now smaller packaging machines will be built in the 16,000-sq m space.
The company also says it received new orders in Eastern Europe and the Middle East for mostly small and medium-sized machines for the packaging industry.
In the automotive segment, where the company says it serves most major car manufacturers in Europe, large orders for VW in Wolfsburg (Germany), as well as for production facilities of Fiat in Italy and Brazil, “were gained against the competition, underscoring Bekum’s high level of expertise in this market segment.” For this it says, several single-station and double-station tank blow moulding machines for producing coextruded six-layer or seven-layer fuel tanks with IMD (in-mould deflashing) and SIB (ship-in-the-bottle) technology are involved.
(PRA)Copyright (c) 2016 www.plasticsandrubberasia.com. All rights reserved.