At the recent German Rubber Conference DKT 2015/International Rubber Conference 2015, Switzerland-headquartered rubber/plastics materials company Trinseo was awarded the DKG Product Award 2015 for its multi-functionalised oil-extended solution styrene butadiene rubber (S-SBR). It was presented by the German Rubber Society (Deutsche Kautschuk-Gesellschaft - DKG), a leading advocate for rubber and elastomeric material knowledge-sharing. Used in high performance tyres, the S-SBR is manufactured by Trinseo in Schkopau, Germany, and offers rolling resistance, wet grip and abrasion resistance for more balanced tyre properties that better meet stringent tyre-labelling requirements and consumer demands.
Trinseo, formerly known as Styron, was carved out from Dow Chemical Company and purchased by Bain Capital Partners in 2010. It celebrates its fifth year in business as a stand alone company.
DuPont’s new AEM for high heat applications

Meanwhile, DuPont Performance Polymers (DPP) introduced Vamac VMX5000, a new and commercially available family of ethylene acrylic elastomer (AEM) pre-compounds that extend the upper temperature limit for AEM applications by 15 to 20°C – offering heat resistance said to be as yet unmatched in AEM, coupled with a long-term improvement in static heat ageing.
Currently under evaluation by major auto OEMs and Tier 1 suppliers for seals and gaskets, air management system applications and high-temperature coolant hose covers, the new polymers are expected to offer a viable alternative to fluoroelastomers (FKM) at significantly lower cost and lower specific weight, in a temperature range between 160°C to 190°C – especially where standard acrylic, ethylene vinyl acetate or AEM elastomers are no longer considered.
Vamac VMX5000 is designed to meet new challenges to automotive hoses and seals imposed by new industry trends such as high-pressure turbo charging, exhaust gas recirculation and other technologies requiring resistance to higher temperatures and aggressive fluids. The compounds also exhibit improved acid and base resistance compared to bisphenol cured FKM compounds, a feature of increasing importance for parts in contact with new oils containing aggressive additive packages or Blow-By.
Additionally, products in the Vamac VMX5000 Series incorporate a new filler system enabling much easier production of coloured non-black parts, leading to better optical colour control combined with superior compression set resistance.
DPP also launched Vamac VMX2122 AEM, a new dipolymer for wire and cable applications offering better physical properties and processing performance than current AEM DP dipolymers, combined with enhanced colour stability. It also meets existing sealing and hose specifications for AEM terpolymers, and thus can be used in applications where diamine cured terpolymers cannot be used.
Lanxess offers a new EVM for reduced mixing times
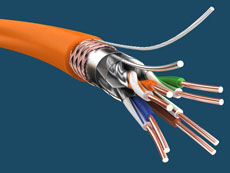
Another new launch was from speciality chemicals company Lanxess and its new family of pre-crosslinked EVM rubbers, in the form of the ethylene-vinyl acetate copolymers of the Levapren PXL series. These have been developed specifically for rapid processing in particularly cost-effective, continuous mixing processes – using Buss co-kneaders, for instance, or twin-screw extruders. Among other things, the free-flowing granules are ideal for reducing mixing times when producing particularly high-quality hoses or cable sheathings. Samples of the new ethylene vinyl acetate rubbers have already been made available to the first customers. The first grades to be available are 500 PXL, 600 PXL, 700 PXL and 800 PXL, with vinyl acetate contents of between 50 and 80%. The properties of vulcanisates produced using Levapren PXL are similar to those made using conventional EVM rubbers from Lanxess.
“Standard Levapren grades have a much lower Mooney viscosity than many other synthetic rubbers,” says EVM specialist Jörg Stumbaum from the High Performance Elastomers business unit at Lanxess. “This brings several advantages – for instance, fewer plasticizers or even none at all are needed for EVM processing. However, some users require EVM rubbers with somewhat higher viscosity. For some time now, we have been able to offer these customers our pre-crosslinked Levapren XL grades.”
However, the technical conditions of the radiation crosslinking process used in the production of these grades mean they have to be mixed very well if the surface of the extrudates has to meet particularly high quality standards. “We have therefore long been looking for an alternative crosslinking technology, and have now found the solution in reactive extrusion,” says Stumbaum.
In this process, the polymer is pre-crosslinked with very small amounts of peroxide – although it is ensured that the product does not contain any traces of the crosslinking agent at a later stage. The process ensures that all Levapren PXL granules have the same crosslinking density. The result is free-flowing EVM granules that are quick and easy to process in an internal mixer or in continuous mixing processes and deliver exceptional flow properties – this is reflected, for example, in the particularly high surface quality of the extrudates. The rubbers in the Levapren PXL series also provide much higher green strength than standard and XL grades. “This can increase process reliability in the production of feeding strips for the extruder, for instance,” says Stumbaum. “And the increased creeping strength can also have benefits for hose and profile extrusion.” What’s more, the new Levapren PXL grades from Lanxess are much less susceptible to blocking even after long-term storage, which keeps the material free-flowing.
“Levapren PXL is a pre-crosslinked EVM grade that we have developed specifically for quick and cost-effective processing in continuous production. This technology is set to become increasingly important – and not just for SMEs in the rubber processing industry,” says Stumbaum. “We are also aiming to extend the user group to processors of rubber and plastics who have not been able to work with Levapren until now. Thanks to Levapren PXL, versatile EVM rubber has now become even more flexible.”
(PRA)