Also, download this story from the electronic issue here
Composites use is growing in Asia, particularly in China. The industry is also marked by a flurry of activities, including tie-ups for advancements and replacement of metals by thermoplastic composites.
GRP composites growing in Asia
The glass fibre reinforced plastic (GRP) composites market is expected to be worth US$45.12 billion by 2019, with China showing the highest growth rates, according to a report from MarketsandMarkets.
Glass fibre accounts for about 90% of the reinforcements used in composites consumption globally. China is the leading consumer of GRP products globally, and the largest supplier, estimated to grow at a CAGR above the global average, to 2019. China and India have enormous potential whereas the US and European countries are leading in R&D of high performance glass fibre products.
GRP composites are widely used in the transportation and infrastructure as well as construction sectors. The demand for renewable energy in the form of wind turbines, and for lightweight fuel efficient aircraft and cars, plus the demand for GRP pipe, tanks and other corrosion-resistant equipment, are major drivers for their increased use in the coming years.
The transportation and aerospace/defence sectors accounted for 49% (by value) of the GRP composites market in 2013. The highest growth is expected from the wind energy and the aerospace/defence markets in the near future.
China composites market outpaces the US
The American composites market represents 36% of the global composites industry in value (EUR22 billion) and 35% in volume (2.7 million tonnes) of 9 million tonnes of the total composites sector, according to the JEC Group that recently staged the JEC Americas show in Atlanta. But the US is still lagging behind China’s consumption of 2.9 million tonnes, with Europe and Asia, excluding China, both accounting for 1.5 million tonnes in 2013.
The increased GDP in the US has also raised the volume of composites per capita around 8-9 kg, whereas it is only 1-2 kg per capita in China, for instance, said the Parisbased composites association.
JEC predicts that the global composites sector will grow by 6% a year by volume from 2013-2018. China will account for 45% of that growth rate over the five-year period, nearly twice as much as North America (23%).
The composites trade group will hold another JEC Americas in Boston, from 28-29 October, and JEC Asia in Singapore from 17-19 November.
Partners tie-up for wood-carbon fibre and mass production processes of FRPs
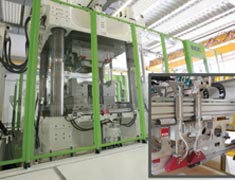
Carbon fibre is strong and light and has many applications but its usage is mainly limited by its high cost. As a result, the material is primarily used in products where performance is more important than price.
As such, Swedish research institutes Innventia and Swerea SICOMP are working on carbon fibre from lignin, a wood raw material, with the target of launching it by 2025 for use primarily in advanced composite materials. The firms are planning a joint demonstration facility with a capacity of 50 tonnes/year.
Another tie-up comes from Austrian companies Engel and Fill to work together to produce tailored turnkey solutions for the industrial manufacturing of fibrereinforced plastic (FRP) components for automotive lightweight construction. At the moment, the biggest challenge is developing economic processes for the mass production of composite parts.
Injection moulding machine manufacturer Engel will provide its system and automation expertise while Fill will provide experience in preform manufacturing and processing. The two partners have already completed their first projects for international automotive groups successfully.
Engel has in 2012 set up its own technology centre for lightweight composites at its large-scale machine factory in St. Valentin, Austria.
Composites replacing metals
With composites use growing in the transportation sector, the National Composites Centre (NCC) in the UK is investigating FRP use in the new highspeed railway (HS2) network. Working in partnership with Composites UK, the trade association for the UK composites industry, the partners will look at composite overhead line gantries, composite noise barriers, composite architectural roofing and station fittings; and composite bridges for further development.
Professor Andrew McNaughton, HS2 Technical Director said, "HS2 has the opportunity to generate significant cost savings through exploring the use of advanced composite materials. Composites are extremely low maintenance and as such can drastically reduce the whole life cost of components. Also being extremely light they can be significantly cheaper to install."
The UK government gave the go ahead for HS2 in 2012. It will be a Y-shaped rail network providing direct rail links between London and Birmingham and onto Manchester and Leeds.
In other news, US supplier Celanese and wire and cable producer Southwire have developed overhead electric transmission lines made from thermoplastic composites, to replace the traditional aluminium conductor and steel-reinforced lines.
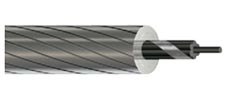
Called the C-7 Overhead Conductor, the power line uses a bundled strand composite core of Celstran long fibre-reinforced thermoplastics combined with heatresistant Fortron polyphenylene sulphide, and capped with a layer of PEEK (polyetherether ketone). The bundle of cables is encased in jacketing made of an aluminium-zirconium alloy.
Benefits include a minimal increase in line sag under high power transfer, thanks to minimised thermal expansion. The so-called stranded core design means there is no single point of possible failure, which can happen with monolithic cable constructions. The life expectancy of the composite wire is also more than 40 years.
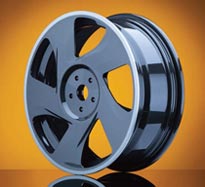
Another use of thermoplastic composite comes from Sabic and Kringlan Composites’s plans to develop the world’s first thermoplastic composite wheel.
The new project uses Sabic’s Ultem resin system and Kringlan’s three-dimensional (3D) composite design processes to create a solution that can be used to replace metal and aluminium.
The significant weight savings made possible through Kringlan’s wheel design, coupled with the ground-breaking material technology employed, can improve fuel economy. The concept also offers a more sustainable solution as emissions can be reduced and the wheel can be manufactured with less environmental impact.
The design of the part also provides the flexibility for the wheel to be mounted with traditional metal spokes, or spokes with carbon fibre-reinforced composites, enabling weight savings.
The full composite wheel prototype complies with current standards set for metal wheels by the German testing institute TüV, increasing the opportunity to work with other automotive manufacturers for the prototyping of lightweight wheels according to their specific design and specifications.
While both companies have been working on a prototype for a German automotive manufacturer, its potential reach extends to multiple industries where weight reduction is a key driver.
With this carbon fibre composite, appliance OEMs can replace metal with a lighter and equally strong technology. In washing machines, for example, this new 3D carbon fibre composite technology can reduce the inertia compared to current metal alternatives, saving costs by reducing the number of secondary operations required to develop key parts.
(PRA)