Also, download this story from the electronic issue here
Capping its 50th year of business in the plastics industry this year, Italian auxiliary machine manufacturer Piovan looks towards reaching into more markets and broadening its client base with an ever-fresh dedication to innovative technology.
Piovan’s roots are steeped in history, starting from 1934 when Costante Piovan & Figli was founded in Padua as a metalworking shop and took its name from its founder. It was among the many firms that shaped the modern world starting from the period of industrialisation in the 1950s.
As it celebrates its 50 years of leadership in auxiliary machinery for the plastics industry, Piovan’s business strategy is far from being archaic. The firm has come a long way since 1964 when it launched its first equipment, a granulator and a material loader, in Italy.
Founder Constante Piovan’s legacy of customer orientation has also filtered down to the three generations that have run the company since. Constante’s son, Luigi Piovan, joined the company in 1960. And in 2000, Nicola Piovan took the helm as Piovan’s President, and made a strong move into international markets.
It is now a multinational company with five production facilities in Italy, Germany, Brazil, China and the US, 21 subsidiaries, agents in more than 70 countries and 900 employees, of which 140 are customer assistance engineers.
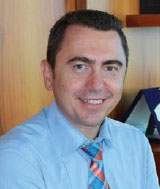
“Piovan's model of business has one main prerogative, and that is of constant growth,” Giorgio Santella, Chief Marketing Officer of Piovan told PRA. This growth is hemmed in the firm’s continuous expansion, capacity build-ups and broad product offering, he said.
It has also been on an acquisition trail and bought US-based Universal Dynamics (UNA-DYN) in 2008 and a majority stake in FDM, a German company specialising in extrusion technology, in 2010.
“Structural expansions are already undergoing, with the just completed increase of production capacity of Piovan do Brasil in São Paulo (Brazil), the planned expansion for Universal Dynamics in Woodbridge (Washington) in the US, and FDM’s move to a larger facility in Cologne, Germany,” Santella added.
Innovation a criteria
Today, Piovan provides the plastics industry a complete range of products and services, including feeding, blending, drying and recycling systems. It also produces industrial chillers and temperature controllers. It integrates its wide array of equipment with proprietary production monitoring and control software.
Hinging on its endurance to innovation, Piovan says it takes pride in its R&D capabilities, naming it as one of its “very strategic asset.”
This is further reinforced by Nicola Piovan. “During our long history of growth and challenges, values and individual skills have become the Piovan corporate culture. However, one key factor has always stayed the same as a guideline for our way of doing business: maximum commitment to innovation for the success of our clients.”
Santella explains, “Our R&D activity is becoming more important. Innovation is one of the three pillars that has in all the 50 years of our business in the plastics industry supported our growth, along with customers and people. Piovan has always had the ability of keeping a constant attentive eye on any technological development, taking place in the industry, and applying that to the equipment we manufacture.”
Of bottles, cars and medical devices
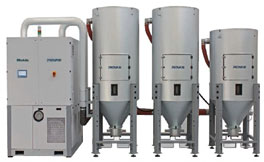
At the heart of Piovan’s machinery line is the Modula multiple hopper drying system, featuring an automatic dual dryer operation, inverter controlled process blowers, IE2 and IE3 class motors, new PLC control with proprietary software, regeneration heat recovery, and system configurations.
For the reason that Modula is the only autoadaptive system available in the market, the system has been installed by German automotive maker BMW at its plants.
“We have obtained the status of preferred supplier of BMW for resin conveying, blending and drying equipment. Particularly in drying, Modula has allowed us to win a very tough confrontation when BMW itself selected a supplier for its new production plants,” says Santella.
Besides breaking into the automotive segment, Piovan’s hold in the PET production segment is as strong as ever. The company started its specialisation in PET as early as the 1980s.
“One out of two PET bottles in the world is produced with our equipment and this is an incredible achievement on its own,” claims Santella.
Along with packaging and automotive, medical is the other sector showing great potential for Piovan.

One of its latest product launches is Quantum, the new generation of gravimetric batch blenders that is proving to be “the most adequate when accuracy, flexibility and safety is an absolute must.”
Machinery made in Asia
Branching out to the various markets, since it made its initial offering on the Italian market five decades ago, Piovan has also planted its seed in Asia. It has branches located in China, India, Thailand, Indonesia and Vietnam. It has two main headquarters in the region: in China, where it has a manufacturing facility in Suzhou, and in Bangkok, Thailand, (Piovan Asia Pacific).
“Spanning 10,000 sq m of assembly area, our facility in Suzhou is expanding further the range of Piovan equipment produced, while Piovan Asia Pacific covers sales for the entire territory of Southeast Asia,” said Santella.
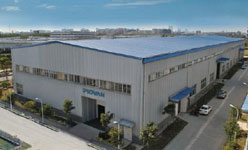
The region’s budding plastics industry has become a growth area for a number of European companies specialising in plastics machinery. Of particular interest is China, given that the country is indeed a huge market.
“Yes, China is a strategic market,” agrees Santella, adding, “The rate of growth here is exceptional and to keep up with it companies must expand their set ups and product range. We have recently started the production of large-size chillers in our factory in China that has been producing small and medium-size chillers for quite some time.”
Chinese processors are also making inroads in manufacturing equipment that more or less have similar functions as the European made ones, but are lower priced.
Having said this, Piovan has also been producing its equipment in China in accordance to similar standards as its equipment produced in Europe, in Italy and Germany, as well as the US and Brazil, according to Santella.
When asked how Piovan differentiates its market sectors and pricing of its equipment, Santella explained, “Our Chinese production is targeting Asian markets, our Italian and German productions are targeting European, African and Middle Eastern markets, and our American productions target the North and South American markets.”
People-centred strategy
Over the years, Piovan has honed its experience in polymer processing, techniques, which the company says it has its quality staff to thank for, owing to their “enthusiasm, concrete ability and vision.”
The firmly crafted expertise backing Piovan’s innovations is shared with its customers, with the firm adding that it strives to be like a partner to them, working alongside them, and sharing their challenges.
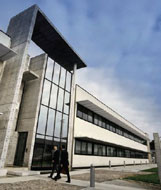
What is next for Piovan, now that it has hit its golden year? Santella says the company will continue gearing for growth.
Nonetheless, there is one thing that will remain unchanged. “Piovan’s business philosophy has been constant through its 50 years of existence. This philosophy is well expressed by our mission statement, and that is: customers, the core of our innovation,” adds Santella.
This is echoed by Piovan’s President, Nicola Piovan. “Our international presence worldwide means closeness to the customers is no empty promise,” he said.
(PRA)