Also, download this story from the electronic issue here
China is still a leading market for made-in-Germany machinery, even with its slower growth. Meanwhile, domestic-based machinery supplier Jinming is expanding its innovation level, to up its ante in the technology sector.
VDMA anticipates lower sales in 2014
Germany’s plastics and rubber machinery manufacturers expect sales to increase by 3% in the current year, meaning that output will hit the EUR7 billion mark for the first time. But this is lower than the 6% growth pointed out by Ulrich Reifenhäuser, Chairman of the Plastics and Rubber Machinery Association (VDMA), at the K2013 show last year.
In 2013, output growth amounted to 3.9%, while exports were up by 4.3%. Both figures set new records for the industry, while in 2015, sales are set to rise by 4% to just under EUR7.3 billion.
Sales to foreign customers are set to record small increases in both 2014 and 2015. “The outlook for the industry’s two most important markets, China and the US, continues to be positive, even though the very high recent growth rates will level off,” confirms Thorsten Kühmann, Managing Director of the Association.
“However, the trend in deliveries to Russia, Brazil, Turkey and India is markedly negative. In Russia, the third largest sales market of the past few years, the potential effects of the political crisis surrounding Ukraine are not yet reflected in the figures at all.”
Meanwhile, the order intake from Germany has been gaining momentum again for several months now with growth rates well ahead of those recorded for foreign orders.
Even with the lower sales growth expected, German foreign deliveries of plastics and rubber machinery have achieved a small increase in their share of global exports. Almost a quarter of all machines exported (24.5%) was manufactured in Germany; China ranks second, a long way behind, with a share of 12.3%, Japan is third with 9.9% and Italy fourth with a 9.1% share.
Large machinery for producing washing machine tubs
One company that is adding on to the increase in sales of the German sector is injection moulding machine maker KraussMaffei, which recently inaugurated the second phase of its Chinese plant in Haiyan.
The German machine maker is supplying four injection moulding machines, manufactured in China, to BSH Bosch and Siemens Hausgeräte (BSH)’s facility in China.
The large MX series machines will be delivered to the BSH facility in Nanjing where they will be used to produce washing-machine tubs. BSH Nanjing has already been using linear robots from KraussMaffei since 2008.
BSH manufactures these tubs in three large plants in Russia, Turkey and China. Two of the four new large machines from the MX series were put into operation back in February 2014. The other two MX850-8100 machines will be installed soon.
The BSH laundry experts decided to use the fully automated injection moulding solutions with LRX linear robots. Once the metal bushings required for the tub have been checked, the LRX500 is used to place them into the mould and remove the finished parts. Bushings of varying diameters are needed depending on the size of the tub being made, and the robots provide these bushings. Getting this right is especially important because the accuracy of the bushing/bearing unit design is a decisive factor in the longevity of the washing machines.

From its production plant in Haiyan, KraussMaffei says it supplies production solutions that are specially tailored to the needs of Asian customers and meet the company's globally applicable quality standards. The MX series of large machines, which are manufactured and assembled locally in China, are designed for use in the automotive, electronics, packaging and transport industries.
Jinming takes on technology role in China
Established in 1987, Chinese extrusion machinery maker Guangdong Jinming Machinery has taken the well-travelled path. One of the leading providers of blown film lines, cast film lines and blow moulding machines in China, it now has a clear view of its market, said Alu Wyen Chan, Overseas Sales Director.
“We now know where we are placed in the industry. We are competing not only with European machine makers but also with the American, Indian, Taiwanese and other Chinese equipment makers,” said Chan, speaking at the April-held Chinaplas show.
Chan claimed that Jinming had positioned itself as close to the top in the extrusion machinery market, “near to Italian extrusion machine makers.”
With this positioning, it has a commitment to its customers, which is to continuously focus on new technology. One of its newest innovations is the five-layer dedicated polyolefin (POD) blown film line.
Last year, at the K2013 show in Germany, it collaborated with US materials supplier ExxonMobil Chemical on a POD machine run, purported to lower costs and save on materials.
Jinming’s blown film machine was running a fivelayer POD structure for collation shrink multipack display film with ExxonMobil’s Exceed and Enable metallocene PE (mPE) resins. The shrink multipack display film included Enable mPE resin-based sub-skin sandwich layers and Exceed mPE resin-based outer layers.
“It has nice distribution layers: with a big core layer, which is not small, and skin layers,” explained Chan.
Though the five-layer technology is not totally new in the industry since barrier resins have been used before, now Jinming’s five-layer die has been optimised for dedicated POD film structures.
Chan said that Jinming was the first Chinese extrusion machinery maker to introduce the five-layer POD line in China.
“Over the last six months, we have received an encouraging number of orders from Chinese customers,” he said, though not disclosing how many orders it had received.
“Packaging film for the food and household goods sectors is a big trend in China now. Plus, the POD line allows for downgauging and offers the ability to adjust material distribution to lower costs. The average formulation cost will be lower and this is a big advantage for processors.”
Jinming also has a three-layer line for a 170-micron liquid packaging film. “It uses 13% less material,” claimed Chan.
The CE, ISO9001 and ISO14001-certified company, which exports almost 50% of its output, with a value of up to US$10 million, is also launching a new technology this year, according to Chan.
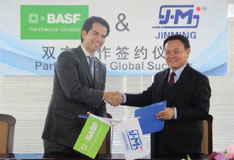
“The POD line was the first step for us. Now, we are developing a new formulation for a five-layer line, specifically targeting the packaging industry. It will be paired with a 500-mm die and the expected output will be 900-1,000 kg/hour,” claimed Chan.
“Our aim is to sell not just machinery but applications,” said Chan.
In line with its technology focus, and in parallel to its cooperation with ExxonMobil Chemical, Jinming recently tied up with German chemicals firm BASF to jointly develop solutions for the co-extrusion film industry. The partnership will offer flexible film manufacturers a complete solution including BASF’s Ultramid polyamide combined with the Chinese supplier’s extrusion machinery technology.
Marcelo Lu, Vice President , Polyamides and Precursors Asia Pacific, BASF, said that with the cooperation, BASF expects its solutions to come faster into the market, as well as “enhance film functionality, optimise production process, and reduce waste and cost during trials.”
Both companies will carry out a wide range of tests and trials to provide customised Ultramid formulation for each multi-layer film type and equipment to flexible film producers.
“We are dedicated to developing our enterprise through science and technological advancement. We see technical know-how and expertise as game changers in the co-extrusion film market,” said Ma Zhenxin, Chairman of Jinming. “By working closely with BASF, it will not only greatly enhance our international competitiveness and improve our technical skills along the value chain, but also add value to the domestic flexible packaging industry.”
This cooperation will also include a joint marketing campaign, the development of new applications in food and industrial packaging, comprehensive testing of film structures and material and equipment matching.
(PRA)