Also, download this story from the electronic issue here
Contributing broadly to society by providing high quality products and services to customers through innovations and the creation of materials, while keeping in harmony with the global environment, have been the aims of Mitsui Chemical Asia Pacific since its inception.
With a focus on the Asian market, Mitsui Chemicals has completed several projects in recent years including the completion of the second TafmerTM plant based in Singapore (2010). Next was the establishment of the Mitsui Chemicals Singapore R&D Centre (2011); Technical Support Centre (2012) and commissioning of Siam Tohcello Co Ltd production in Thailand (2014).
This will be followed by the completion of the new Prime Evolue Singapore Pte Ltd plant in 2015, in an effort to further strengthen the support and presence of the company in the region.
“The number of projects in Asia is directly proportional to our belief of the potential that this region holds,” says the company.
In line with this, Mitsui Chemicals has also embarked on innovations and presents below a portfolio of its current and future innovations and technologies that it will be bringing to the market.
Mitsui Chemicals Singapore R&D Centre (MS-R&D)
Mitsui Chemicals opened its first overseas R&D centre in Singapore in 2011. Mitsui Chemicals Singapore R&D Centre (MS-R&D) works with local partners as a solution provider in the ASEAN region with proprietary technologies in polymeric materials and catalysis science. Since the 1980s, this R&D capability has extended the group’s business opportunities in the region, along with other capabilities for sales, marketing, manufacturing, and technical support. In creating new values with new nanomaterials, MS-R&D is developing unique organic and inorganic nanomaterials (one nanometer is 10-9 m). Examples include:
- Stable polymer nanoparticle dispersion in water
- Hydrophobic polyethylene (PE) and hydrophilic polyethylene glycol (PEG) are combined together as a block copolymer, which is designed to form a micelle-like nanoparticle having a uniform size (10-20 nm) when dispersed in water.
- In contrast to low molecular weight surfactants, this particle is stable towards heat (up to 100˚C), pH (1-13), or its concentration. The nanoparticle can encapsulate functional molecules such as water-insoluble molecules to be dispersed and functional in water [Figure 1]. This material can be used as a material responsive to external stimuli for sensors and probes, smart ink, film and coating, drug delivery and nanoreactor applications.
- Mesoporous silica
- MS-R&D’s mesoporous silica has large and uniform pores with the size of 10-20 nm. These pores are arranged in an ordered manner and connected through a narrow channel. Porosity and surface area of the mesoporous silica can be controlled in a wide range (up to 900 m2/g). This mesoporous silica is available as a fine particle with various sizes in nano and micrometer scale. The particles, which are smaller than 100 nm, are transparent to visible light, and can be applied to optical materials
- Other applications include heat-insulation material, anti-reflection coating and film, low-k material and as a carrier of functional chemicals.
- In addition to these nanomaterials, MS-R&D has developed a process to manufacture telechelic olefin polymers (possessing two reactive functional groups situated at the chain termini). Such telechelic olefin polymers are a useful building block to create block copolymers consisting of polar segments and nonpolar olefin polymer segments. This technology was recently reported in a scientific journal (J. Am. Chem. Soc. 2013, 135, 8177-8180).


Evolue™ – the perfect solution for high value packaging
Prime Polymer Co Ltd (Prime Polymer) was established in April 2005 as part of a comprehensive tie-up with Mitsui Chemicals Inc and Idemitsu Kosan Co Ltd.
Prime Polymer’s global polyolefin business activities for research, production and marketing have been completely integrated to create a synergistic impact within the company and for the stakeholders. As a result, one of Prime Polymer’s strategic and core product is Evolue™, a metallocene catalysed, hexene-based linear low density polyethylene (m-LLDPE) produced by Mitsui Chemicals’s bi-modal technology.
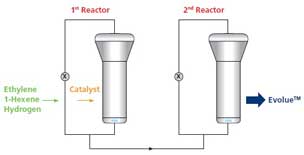
Boasting impressive ease of processing, excellent heat seal-ability, coupled with low odour and low “gel” properties, Evolue™ is said to be the perfect solution in meeting high value packaging requirements. Evolue™ is currently produced only in Ichihara, Japan, by Prime Polymer, with a capacity of 300,000 tonnes/year.
With the escalating need for high value packaging, the usage of Evolue™ has grown simultaneously. To meet this overwhelming demand, Prime Polymer has decided to expand the production of Evolue™ outside of Japan. As a result, Prime Evolue Singapore Pte Ltd, a subsidiary of Prime Polymer, was established in October 2012.

An upcoming new manufacturing facility, dedicated to producing Evolue™, will be located in Jurong Island, Singapore. The new manufacturing facility, which is scheduled to come on stream in mid-2015 with a capacity of 300,000 tonnes/year, will bring Prime Polymer Group’s total capacity of Evolue™ to 600,000 tonnes/year.
Singapore, having a well-established infrastructure and the availability of critical feedstock, an efficient workforce and free trade agreements with many countries, provides an excellent platform for Prime Polymer Group to meet and satisfy the exponentially growing demand of customers’ needs and to discover new business opportunities.
Prime Polymer Group says it aims to congeal its position, especially within the fast growing Asian market, through “providing perfect solutions for high value packaging via Evolue™.”
T.U.X™ - Strengthen Competitiveness with Cost Reduction
With more than 80 years of experience, Mitsui Chemicals Tohcello Inc (MCTI) is a leading manufacturer and supplier of film products to the food packaging industry. As a business sector of Mitsui Chemicals group, MCTI also offers protective films for industrial applications in such areas as the semi-conductor and photovoltaic industries. MCTI strives to offer innovative and competitive products while maintaining its reputation as a stable supplier.
MCTI offers a wide range of food packaging films, from conventional BOPP film to high performance L-LDPE sealant film. It is little wonder that the T.U.X™ L-LDPE sealant film has become the market leader in the Japanese food packaging industry. The company’s goal is to spread this success by sharing its industry knowledge and expertise throughout ASEAN.
T.U.X™ is a 100% metallocene L-LDPE component T-Die cast film. Performing as a sealant film, T.U.X™ has excellent properties:
- Good heat seal strength
- Good hot tack strength
- Good cold resistance
- Good transparency
- Outstanding gloss
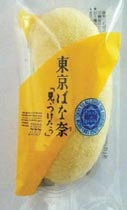
With an already extensive experience in the ASEAN area, MCTI realised that there is an urgent need to resolve leakage issues that are due to poor package sealing or rough handling of products, which causes output losses. By taking advantage of the excellent heat seal strength of T.U.X™, leakage issues can be solved immediately. Thus, T.U.X™ can help to reduce losses and increase profits.
It also serves to solve the problem of transportation to end consumers and food and retail outlets that is full of unpredictable problems, for example rough handling by unskilled employees and poor condition of roads.
Success case when changing to T.U.X™
Premise:
1) Cost of content is 0.4
2) Ratio of loss for conventional film is 1%
3) Quantity of input is 1,000,000

From the above case study, it is clear that T.U.X™ reduces costs and adds to customers’ profits, which becomes even more critical with a high value product.
In order to satisfy increasing demand in the ASEAN market for T.U.X™ high performance L-LDPE sealant film, MCTI has partnered with SCG Chemicals, a leading chemical company in Thailand, to establish a new manufacturer known as Siam Tohcello Co Ltd (STC).

STC has launched mass production of the material from January 2014. STC says it is on a mission to provide reliable quality with a stable supply based on MCTI’s food packaging film expertise. “Combining the expertise and industry knowledge with local production, T.U.X™ can eliminate output losses, thus allowing our customers to increase their profits,” says STC.
TPX for food containers for microwave cooking
TPX is a functional polyolefin, which only Mitsui Chemicals Inc is producing in the world. It is a 4-methyl- 1-pentene-based crystalline olefin copolymer with excellent clarity, heat resistance, chemical resistance, light weight, and non-stick properties.
Taking advantages of its properties, TPX has been widely used for industrial materials, including mandrels and sheaths in the manufacture of high-pressure rubber hoses, mould cups to create Light Emitting Diodes (LEDs), and other applications such as release films for Flexible Printed Circuit (FPC) manufacturing process and release papers in the manufacture of synthetic leather like PVC or PU.
Furthermore, TPX possesses the lowest density among existing thermoplastic polymers leading to lower weight products. This reduces the environmental load during transportation and also total polymer used. It should also be noted that TPX is a halogenfree polymer and denoted as environmentally-friendly material.
The benefits of using TPX as microwavable containers:
Table 1 shows the performance comparison of various materials used for microwavable containers. First of all, being a polyolefin resin, TPX is completely BPA-free and thus environmentally-friendly.
Secondly, TPX shows the best non-stick property among the competitors. This means that a TPX container is easily washable with less use of detergent, even after it is used with curry, meat sauce, and ketchup.
Thirdly, especially compared to PC and co-polyester, TPX shows better steam resistance. This means that TPX can be used in dish washers for much more time, leading to longer shelf life and thus leading to less wastage.
Finally, compared to PP containers, TPX shows much better heat resistance. Hence, TPX containers can be applied especially for oily foods, which require heating up in the microwave oven. Indeed, recently TPX has been an increasingly popular material for food containers for microwave cooking, especially in Japan.
APEL for plastic lenses with excellent quality
APEL is a highly transparent polyolefin suitable for high quality plastic lenses, developed by Mitsui Chemicals. A cyclic olefin copolymer (COC), APEL shows the highest refractive index among existing amorphous polyolefins and also the lowest birefringence resulting in the best optical isotropy, significant in plastic lens application, as proven by a lot of success stories mainly in Asia, including Japan, Korea, Taiwan, and China.
Furthermore, APEL also shows excellent moistureproof properties and chemical resistance and is used as a medical packaging material.
Table 2 shows a comparison of properties with representative competing materials used for plastic lenses. As shown in the Table, APEL shows the lowest birefringence, leading to excellent optical isotropy. This excellent optical isotropy helps to obtain far clearer vision with almost no optical defect.
In addition, as refractive index of APEL is higher than competing amorphous polyolefin (cyclic olefin polymer; COP), by using APEL, thinner lenses can be produced, leading to a certain downgauging.
Compared to PC and PMMA, APEL is a non-polar polyolefin and hence shows low water absorption, leading to far better consistency of optical properties. Thus, APEL definitely helps customers to produce plastic lenses with extremely high quality, compared with existing competitors.
For further enquiries, please contact:
MCAP_enquiries@mitsui-chem.co.jp