Also, download this story from the electronic issue here
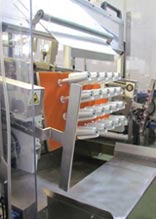
European suppliers are racking up machinery sales in Asia; with Amut having sold two machines to Vietnam and Malaysia and Battenfeld-Cincinnati delivering its Multi-Touch roll stack technology to China. Meanwhile, WM Wrapping Machinery highlights a line for the production of two-colour disposable cups made of multi-layer PP.
Amut scores in Asia
Amut Comi, a member of the Amut Group, says its sales are increasing in Asia. Andrea Peretto, Sales Manager for the Southeast Asian market, says the company has recently delivered an AMP 630-GP second generation extrusion and thermoforming plant, to South Vietnam.
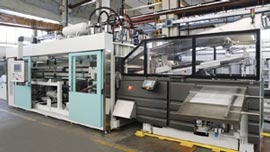
“It is equipped with an in-line automatic pickup stacker and an EA100 extruder. The plant is able to produce 95 mm-diameter PP disposable cups,” he explained. Peretto also stated that the machine has a capability of high volumes of 33,000 cups/hour for 500 ml size cups and 35,000 cups/hour for 450 ml size cups. The system comes complete with a three-station volumetric dosing unit, with a capacity up to 600 kg/hour, a static mixer and an in-line mill to grind the thermoformed scraps, placed after the thermoforming machine.
Another thermoforming plant for PP cups, model AMP 850-GP, will be delivered in the next few months to a customer in Malaysia. The machine has a 32-cavity mould and 40 dry cycles/minute.
The production realised from this machine is 55,000 cups/hour for 360 ml cups, 50,000 cups/hour for 500 ml sizes and 46,000 cups/ hour for the 700 ml ones. Peretto also says that the sheet used comprises 67% of PP and 33% of regrind.
A feature of this machine is the fully automated pick-up stacker: the cups are picked up by vacuum ejection with the usage of mandrels, which are mounted on a suction plate. The suction plate turns 180 degrees and pushes the cups, with bottoms first, into a stacking mask.
Amut Comi, a 100% Italian company operating since 2002, manufactures thermoforming machines that are said to be sturdy and modular and that run at high performances at low energy consumption. The machines boast durability and are able to cut tough materials like PET and PP at high cycles. The EA100 extruder (100 mm) permits a production output of 600 kg/hour and allows for up to 38% of recycled material in the sheet.
Multi-Touch goes to China
Chinese company Guangdong Huasheng Plastics in Shantou has purchased a thermoforming sheet extrusion line with a high-speed extruder and a Multi-Touch roll stack from the Packaging Division of Battenfeld-Cincinnati, Germany. This is the first time that the Multi- Touch has been delivered to a Chinese company, says Battenfeld- Cincinnati, adding that it is its fourth Multi-Touch installation in Asia.
Huasheng, established in 1997, already operates two manufacturing plants, where some 90 tonnes of cups and other types of containers are produced daily in addition to 120 tonnes of PP, PS, PET, EVOH and PLA sheet. These products are used in the packaging industry, both locally and globally. Huasheng exports its products to more than 30 countries.
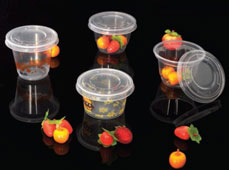
Previously, the company used only locally produced extrusion equipment, and has now decided to acquire a German line for its newly built production hall.
Company owner Wei Yunan comments: “The Chinese packaging market is one of the markets with the highest growth rates worldwide. We have also noticed a rise in the demand for higher standards of quality and efficiency, to which we are responding with this investment. Since its production start-up in March, the Multi-Touch roll stack from Battenfeld-Cincinnati has already contributed substantially to improving our product quality.”
The new line, with the BC-75-40 DV T4 high-speed extruder that has an output of up to 1,400 kg/hour of PP sheet, is replacing a total of four to six previously used Chinese extrusion lines, thereby allowing for a reduction in space requirements and operation expenditure.
In addition to its high output, the new sheet extrusion line distinguishes itself with its sheet quality and high flexibility. It is able to produce sheet ranging from 350- 2,500 microns in thickness.
However, the unique selling point of this line is the new Multi-Touch roll stack, which has come on the market only recently. It is said to deliver improved sheet quality due to a unique roll configuration. First, a two-roll stack takes care of pre-calibrating the material coming out of the flat sheet die, then the sheet passes through the recalibration unit equipped with up to seven smaller rolls. Thus, consistent roll contact and consequently uniform cooling on both sides of the sheet is ensured, even at maximum line speeds.
According to Battenfeld-Cincinnati, the outcome is a significant improvement in sheet tolerances and production of stress-free sheet with optimal transparency, flatness and a uniform thickness profile.
WM’s multi-layer PP cup line
WM Wrapping Machinery from Stabio (Switzerland) has successfully tested a complete line for the production of two-colour disposable cups made of multi-layer PP. The plant is for a leading European manufacturer of disposables items, which also has another WM complete in-line system for the production of plates made of co-extruded polystyrene HIPS.
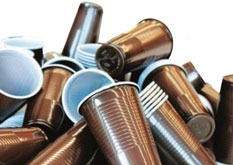
The INTEC FT 900/3 line consists of an automatic dosing and feeding unit, including an in-line system for managing and recycling waste. It also comes with a 120 mm-diameter main extruder and two 80-mm co-extruders. The total extrusion capacity is 1,096 kg/hour.
The flat die head of the extrusion feeds a vertical laminating calender with three rolls, creating a sheet with a width of 930 mm and a thickness ranging from 0.2-2 mm. The extruded sheet is then sent in line to the transport system with toothed chains of the FT900 thermoforming machine, which has a tilting lower platen and a servoassisted plugging unit. The forming tool can accommodate moulds with a maximum size of 880 x 520 mm and has a clamping force of 75,000 DaN. The tilting system of the movable lower platen is based on an innovative double Desmodromic system of cams and levers operated by a servomotor.
The 51-cavity mould allows for the production of cups with a finished border diameter of 73 mm and a height of 95 mm.
Once thermoformed and cut (an operation that occurs simultaneously in the same mould), the cups are removed from the bottom half-mould, which tilts at 75 degrees by a plate with aspirating spindles, and automatically transported to a collection cage that unloads the various rows of stacked cups on a conveyor belt and continuously feeds a rimming unit (a WM system) with three rotating screws.
This turns up the upper edge of the cups and then sends the rods to the accessory counting and packing units.
The waste or the residual perforated PP sheet, from which the cups are made, is ground using an in-line soundproofed grinding mill. The flakes are then, by means of a blower, sent to the dosing/mixing unit located above the extrusion unit. This creates a closed loop system, from the raw material to the finished product, with the direct in-line recycling of waste materials.
The INTEC 900/3 system can produce up to 120,000 cups/hour of 200 cc cups, minimising energy consumption and reducing necessary personnel.
(PRA)