Circular Economy: coming to a full circle with waste-to-resources
Also, download this story from the electronic issue here
Resources used in manufacturing are depleting at a rate faster than they are being replenished. Unless utilisation mind-set shifts to producing less to zero waste, this situation could become detrimental, says Angelica Buan in this report.
When recycling is not enough
Ever since industrialisation began, the production of goods has been using up resources, most of which would eventually end up in landfills at the product’s end of service life. It is only a matter of time that scarcity of resources becomes irreversible; and so changing the way resources are utilised can make a difference.
The concept of sustainability is an industry game changer. However, more often than not, the industry continues to move along the linearity of a “make, use and dispose” economy. Known as the linear economy, it underpins an end-of-life concept, which ultimately produces wastes. And within the context of sustainability, businesses mind no more than resource footprints and energy efficiency.
On the flipside is the circular economy (CE) model that embodies a restorative economy, whereby wastes are resources. The World Economic Forum (WEF) explicitly defines a circular economy that is beyond the popular notion of oft-said sustainability in lieu of recyclability, for example. It said that within the CE’s premise, “products are designed and optimised for a cycle of disassembly and reuse”. This, thus, distinguishes CE from mere recycling or disposal, “where large amounts of embedded energy and labour are lost.”
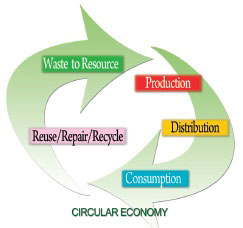
Since CE is “restorative by intention and design”, all other components associated with it must not hinder recovery or restoration of resources, such that renewable energy must be used and toxic chemicals must be cancelled out.
Adopting this model has manifold benefits, one being the opportunity to innovate materials with restorative design.
UK-based charity Ellen MacArthur Foundation (EMF) projects that CE will open up a trillion dollar business opportunity for businesses that adopt it, while the European Commission (EC) takes stock of using resources efficiently as a harbinger for new growth and job opportunities.
Along the context of the Europe 2020 Strategy, resource efficiency across the value chains can reduce material input needs by 17% to as much as 20% by 2030, and could represent an overall savings potential of EUR630 billion/ year for the European industry.
The CE is gradually gaining foothold across manufacturing sectors worldwide. The EC is formulating strategies for Europe to make the region’s economy more competitively resource-efficient. It has hosted a stakeholders’ conference specifically to discuss CE-relevant policies. The body is also targeting to release its revised proposal late this year, after an initial proposal was shelved last year, reflecting policy options that more than highlight waste management, intelligent product design, sustainable consumption and use of raw materials.
As the EC puts it, “resources must be managed more efficiently throughout their life cycle.”
Staying in the loop
Adopting CE also calls for staying on its axis. A new assessment tool is offered by EMF and materials information technology specialist Granta Design, following the release of the Circularity Indicators Project findings. The web-based tool can be utilised by businesses to monitor where they are at in the CE loop.
According to EMF, while businesses have already acknowledged the significance of adopting the CE model, they require a standard metrics to keep track of their performance in transitioning from a linear to a circular economy.
The EC’s Life-funded two-year research initiative Circularity Indicators Project yielded a set of indicators that assess how well a product or company performs in the context of a circular economy. The developed indicators consist of a main indicator, the Material Circularity Indicator (MCI). It measures how restorative the material flows of a product or company are, including the amount of virgin material recycled and recovered materials used; and complementary indicators that allow additional impacts and risks to be taken into account.
The indicators can be used by product designers, but might also be used for several other purposes, including internal reporting, procurement decisions and the evaluation or rating of companies, according to EMF.
The assessment system also facilitates the use of optional complementary risk and impact indicators, and company level indicators. The complementary risk and impact indicators can be used alongside the MCI to offer insights into potential risk in relation to business priorities and how changing circularity impacts other areas of business interest. Company level indicators are an aggregation of the MCIs for all product types within that business.
The MCI and accompanying indicators, according to their proponents, are a set of unique tools that can be utilised in the design, reporting and evaluation phases of a product or collection of products. The company-level indicators and potential extensions might also be used in research, rating and evaluation of companies, policy-making or education.
Plastics industry takes a stand
Plastics manufacturing takes up 4% of the global output of oil from fossil fuel, a depleting resource. The British Plastics Federation (BPF), in its 2008 the statistical review for the oil market, estimated the oil reserves, at the prevailing production rates, to be around 1.24 trillion barrels or to last for only about four decades.
Hence, the plastics industry is expected to benefit from CE, and thus, it is fast-tracking its adoption.
The packaging sector, a leading user for plastics, is also a leading waste producer. It is also becoming a major stream in solid wastes due to its quantity. Plastic waste is the third major constitute at municipal and industrial waste in cities, after food and paper wastes, according to a 2009 assessment report by the United Nations Environment Programme (UNEP).
The bulk of plastics turning to wastes have increased over time. According to the US Environment Protection Agency (EPA), in 2013 alone, the US generated about 14 million tonnes of waste plastics, made up of containers and packaging, with only 9% of the total plastic waste generated that period recovered for recycling.
Globally, the market for plastics packaging is forecast by Transparency Market Research to reach US$370.25 billion by 2020. Just imagine how much of this packaging will potentially end up as waste!
Targeting an increase in recovery rates, UK-based plastics organisation Plastics 2020, comprising BPF, Packaging and Films Association (PAFA), and Plastics Europe, together with the Wastes and Action Programme (WRAP), has recently launched a recycling action plan. The Plastics Industry Recycling Action Plan (PIRAP) enables the plastic packaging supply chain to involve itself in the UK’s target of 57% recycling of plastic packaging by 2017, recycling being a vital component sustainability, according to BPF.
PIRAP also highlights the areas that need to be enhanced to develop end markets for plastics recyclate, such as increasing collection rates, adopting best-in-class collection methods, and optimising sorting infrastructure and design, to cite a few.
Meanwhile, Belgium-based plastics association Plastics Recyclers Europe (PRE) finds that the current developments in the PET packaging market may ruin recycling streams.
PRE cited that the milk packaging, home and personal care markets are planning to shift from using HDPE to PET based on costs, marketing and sustainability.
And because, aesthetically, these markets require colourful packaging, PRE says, the switch could result in additional production of more than 300,000 tonnes of coloured, and black and white PET.
PRE said that currently, the PET recycling markets are unable to undertake recycling these additional colours, citing further that these coloured packaging require extra sorting at the recycling plants.
Pigments like titanium dioxide, may also contaminate the recycler’s end product. The resulting recycled PET (rPET) could also pose problems with food contact. This could lead to rPET losing its appeal in the market, PRE explains.
The group suggested potential solutions such as using full body sleeves that are detectable by near infra-red sorting systems. Most importantly, producers are urged to not break the circular functioning of these recycling streams.
Managing e-waste responsibly
The growth of information technology is also stirring concern on the increasing output of high-tech trash. With the advent of advanced material components in electronic goods that are engineered to be reused, recycled or upgraded, the potential for them being disposed is high, giving rise to electronic waste or e-waste.
In a report by Consumer Electronics Association (CEA), the consumer electronics industry recycled an estimated 281,000 tonnes of electronics in 2013, an increase of 15,875 tonnes from 2012.
E-waste scraps may also pose hazardous risks during recycling or disposal, with safety practices recommended.
Texas-headquartered PC maker Dell has recently banned the export of defective computers and parts (except for plastics or unleaded glass that can be reprocessed) to developing countries, amidst situations of inadequate facilities, and environmental and work-safety regulations. In countries where e-wastes are shipped, people become exposed to toxic chemicals that are present in electronic parts, when dismantled or burned. Dell’s move, according to environmental groups, is a step in improving e-waste practices among electronics companies.
Dell’s “Legacy of Good Plan” is a take-off point for responsible e-waste management.
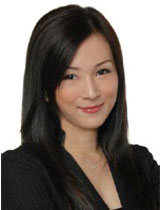
In an email interview with PRA, Crystynna Ewe, Asia-Pacific & Japan Director of Global Take Back at Dell, said that the company has embarked on sustainability initiatives to convert waste to resources. “From the beginning, Dell has viewed waste as inefficient. That set us on a path toward making sustainability a part of all that we do,” she said, adding that the company is currently the world’s largest technology recycler with take-back programmes in 78 countries.
“Since 2008, Dell has recovered around 645,000 tonnes of used electronics. Through our innovative sustainable packaging alternatives, like wheat-straw, we have avoided 14,000 tonnes of packaging since 2009, while helping support local farmers and reduce pollution in places like China. We’ve used nearly 10,000 tonnes of post-consumer recycled plastics in our products,” Ewe stated. In view of its 2020 goal, Ewe said that the firm has reached 44% progress toward its target of using 22,700 tonnes of recycled-content in its products.
In 2014, Dell had used more than 4.5 million kg of recycled-content plastics in its monitors and OptiPlex desktops, sourced from used water bottles and CD cases, according to Ewe.
“Building on this approach, we have also begun an industry standard closed-loop programme, using plastics recovered from electronics collected through our recycling efforts to make new computers. The plastics are from recycled computers recovered via the Dell Reconnect recycling partnership with Goodwill Industries International (an American nonprofit organisation). These plastics are shipped to our manufacturing partners who mix the recycled plastics with some virgin materials. To date, Dell has shipped 18 new product models (desktops, All-in-One, displays) using the closed loop recycled plastics with plans to add more in the future,” Ewe said.
The company has also teamed up with the United Nations Industrial Development Organisation (UNIDO) to implement e-waste management models in developing countries in Africa, Asia and Latin America, by developing up-scale facilities complying with international standards for e-waste recycling.
As part of its circular approach to curb e-waste, the firm also uses sustainable materials for its packaging.
“Our carbon-negative Air Carbon Plastic is made from air and greenhouse gases, unlike almost all other plastics, which are developed from oil. We’re turning carbon, that would otherwise be part of the air we breathe, into plastic packaging that will hold our Latitude series notebooks,” said Ewe.
Dell collaborates with California-based biotechnology company Newlight Technologies that has developed an enzyme that efficiently converts carbon from air into long-chain polymers that can be used as substitutes for oil-based plastics, according to Ewe.
“Our vision is to scale up use of this plastic globally across the packaging and product portfolio. Through this innovation, we will reduce our use of oil, empower a sustainable start-up and help our customers be more green,” she said.
Ewe also says, “The days of the linear economy are numbered. Leading companies are already rethinking their business models to engage a circular approach that puts a premium on getting the most out of resources.”
According to Ewe, Dell is making this shift by way of transforming the way it designs its products and services, looking at the whole system for efficiencies and extended, sustainable use.
In fact, managing e-waste through the circular approach is the way forward.
(PRA)Copyright (c) 2015 www.plasticsandrubberasia.com. All rights reserved.