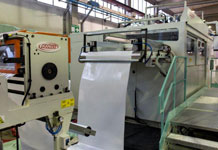
Italian machine maker Amut recently supplied to Poly Er, one of the biggest Russian thermoformers, the first in-line thermoforming machine producing disposable plates (in HIPS + GPPS material) with a weight of 3 g, which is able to save money as well as allow for quality.
Following the specific needs of the customer, Amut says it included a sophisticated control system and complete coordination and management of the production process from the raw material up to the finished product. The machine produces:
- 52,500 plates/hour with 3 g weight, 165 mm diameter and 135 micron thickness
- 34,500 plates/hour with 5 g weight, 203 mm diameter and 146 micron thickness
Both productions have very low tolerances for the medium weight of the material and for the plate: from +/- 0.1 g to +/- 0.2 g.
Despite being very thin, the sheet is said to be in "absolutely" stable conditions in production thus assuring lack of flaws on the finished product.
The line includes a raw materials loading and dosing system for the main extruder (four components) and for the co-extruder (two components). The thermoforming skeleton grinding is closed-loop made and is able to treat thin material (apparent specific weight lower than 0.2 kg/dmq).
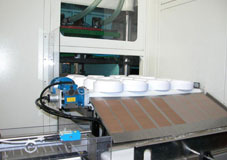
Furthermore, the grinder is equipped with a very fine tension gauge system. The extrusion unit is composed of a single screw main extruder EA100 with plasticising capacity of 600 kg/hour and an under vacuum venting system complete with closed-loop water control and of a single screw co-extruder EA60 for external layers and suitable for different productions.
A high level of precision of die regulation parameters allows to maintain the thin thickness and the low weight and to avoid sheet edge fragility. The die flow box has required as well an accurate design. It is possible to obtain the following sheet structure without stopping the machine: A/B, B/A, A/B/A.
The calender, complete with thickness gauge system, assures a gradual and uniform cooling and consequently an optimisation of sheet internal tensions. Additionally, there is a haul-off with tension control and a pressurised water diathermic unit with 3 circuits. The stack control at the entry of the thermoforming machine is carried out by means of both measurement optical system and a dandy roll.
Based on PA 1000 model, the thermoforming unit has been especially optimised to treat HIPS material and to avoid the breakage of this very fragile structure through special transport system, heating oven, machine movement, thermoregulation and thermodynamic loop performances.
A special packing unit is able to pack from 12 to 100 pieces, more plates with equal quantity of material. An integrated stacker system, where the intervention of the operator is minimum, is also supplied.
(PRA)