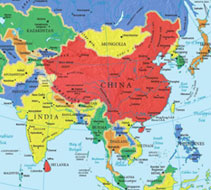
Asia’s growing middle class and increasing urbanisation have buoyed the region’s chemical demand, particularly for olefins, according to analysis from IHS, but not all countries are equal in their demand growth.
According to IHS, the rise in disposable income for Asia’s middle and upper classes is increasing consumption of durable and non-durable goods made from chemicals and polymers. The growth of households with income greater than US$5,000 -- a threshold considered middle class in the region and often associated with urbanisation -- is greater than the general population growth and fastest in countries such as China, Indonesia, and Thailand.
“Across this income threshold is the time when people buy their first refrigerators, televisions, and other appliances,” said Tony Potter, Vice-President of Asia Pacific for IHS Chemical. “Ultimately, they buy their first car. In doing so, they essentially become new customers of the petrochemical industry. In China, an estimated 28 million people have been crossing this threshold each year, with a further 23 million in India. Throughout the whole of Asia, there are approximately 70 million new chemical industry customers added each year.”
Asian olefins to outpace US shale gas output
New crackers based on shale-related ethane in North America or low-cost feedstocks in the Middle East grab headlines, Potter said, but Asia is set to add more olefins capacity by 2020 than these two regions combined. “Asia is the engine of global demand for olefins. At IHS Chemical, we forecast global incremental demand growth for ethylene and propylene combined will exceed 10 million tonnes/year during the next five years, with Asia accounting for 60% of demand growth.”
However, not all Asian countries are experiencing equal growth in chemical production. China will be responsible for much of the investment. Potter said that IHS Chemical expects 53 olefin projects to start up in China by the end of 2018. Many are coal-to-olefins (CTO) or methanol-to-olefins (MTO) projects, but there are also a substantial number of on-purpose propylene projects.
The coal-based units are based both inland, where coal is available at lower mine-mouth prices, and in coastal provinces, where coal prices are higher because of transportation costs and exposure to the international coal market. Several CTO/MTO plants are already operating, but IHS says the CTO/MTO rush will be concentrated in 2015 to 2017 and tail off thereafter. IHS believes the coal-based builds, likely constrained by water availability and environmental concerns are finite.
Said Potter, “Capital costs are substantial, but once the units are built, operating costs will be sufficiently low to position these Chinese units in the lower-cost half of the global supply curve.”
The situation varies elsewhere in Asia. India has much potential for growth, but olefin investments have not kept up with demand and derivative imports have been growing. Elsewhere in Asia, cracker investments are difficult to justify in the absence of advantaged feedstocks. Malaysia, Indonesia, and Vietnam, driven by growing domestic deficits of base chemicals and polymers, are all studying projects for start-up during 2018 to 2022. According to Potter, the story is different farther north: in Japan and Taiwan, where the olefins industry is consolidating and reductions in capacity are expected.
Propylene capacity addition in Asia during 2013 to 2018 will amount to 23 million tonnes/year, 85% of which will be in China. Said Potter, “Due to this dominance in new capacity occurring in China, it might be tempting to conclude that the rest of the world does not need to invest in new propylene units, but that would be misguided. In reality, it is more likely that much of the Asian new-build capacity will run intermittently or at low operating rates. Much of the coal and all the naphtha-based propylene is tied to ethylene production, with relatively limited control over the ethylene-propylene production ratio.”
Discretionary propylene production, he said, is from coal-to-propylene/methanol-to-propylene, propane dehydrogenation (PDH), and metathesis units. “The dependence on imported propane in a region that historically has had the highest propane prices in the world,” said Potter, “results in less-than-compelling economics, suggesting that the new PDH units will act as swing capacity.”
China to lead Asian PP capacity supply
Meanwhile, China will lead new global PP capacity increases over the next five years, as its goal of self-sufficiency drives 7.48 million tonnes/year of additions, of which 97.6% will come from new plants and the remainder from the expansion of existing facilities, says a new report from UK-based research and consulting firm GlobalData.
Global PP capacity increased at a Compound Annual Growth Rate (CAGR) of 5.2% from 2003, reaching 65 million tonnes/year in 2013, and is expected to continue rising to 86 million tonnes/year by 2018, at a slightly higher CAGR of 5.8%, according to GlobalData.
Its report also states that China and Russia will be the leading contributors to future PP capacity increases, and will account for a combined 45% of global additions over the next five years.
Carmine Rositano, GlobalData’s Managing Analyst covering Downstream Oil & Gas, says: “A demand-side push is driving additional capacity in China, forcing it to produce more domestic PP.”
GlobalData forecasts that the country will account for 62.4% and 35.5% of planned Asian and global capacity additions by 2018, respectively.
Russia will be the second largest contributor to growth, mainly due to the country’s recent diversification into the petrochemicals sector, which has seen substantial investment in bulk polymer industries, such as PE and PP.
Rositano explains: “Until 2012, Russia’s PP capacity was only 0.65 million tonnes/year, but this increased to 1.33 million tonnes/year in 2013 and is further expected to reach approximately 3.48 million tonnes/year by 2018, with all additions coming from new plants.”
GlobalData also states that Venezuela and India will be the respective third and fourth largest contributors to capacity increases over the next five years, with both countries investing in the PP sector to cater to the domestic market and replace imports.
(PRA)