Building the world’s infrastructure with composites
Also, download this story from the electronic issue here
Fibre-reinforced composites are breathing life into modern innovations in buildings, says Angelica Buan in this article.
As the saying goes, there is always a first time for everything. In technology applications, the first time is almost always a beta stage, when hits and misses are encountered. But it is also the phase when the “Aha moment” is witnessed.
Claims of “firsts” have marked important industrial milestones, such as the birth of Bakelite, the grandfather of reinforced plastic composites in the early 1900s, that has since ushered the use of better performing materials for wider applications. The development of fibre-reinforced composites (FRCs) has set the motion for more application segments to be tapped; and established more technologies with properties that outperform those of conventional materials.
Today, FRCs are used as strategic materials in industries that demand weight reduction and high strength components. Transparency and Market Research in its FRC market analysis projects an increasing use of FRCs, from automotive to construction industries. FRC’s versatility and durability are expected to boost their market demand further.
Hence, it is not surprising that some of the world’s industry breakthroughs feature FRCs as key elements.
Pilot reusable house a model for circular economy
Not an ordinary four-walled structure, the ICEhouse (where ICE stands for
Innovation for the Circular Economy) is an architectural masterpiece for
sustainability. Architect William McDonough, working with
partners and Saudi Arabia-headquartered chemicals giant
Sabic unveiled the ICEhouse at the 2016 World Economic
Forum (WEF) held in Davos, Switzerland, recently.
The structure is made of aluminium (the structural frame), polymer, aerogel, and PA6. It utilises several forms of Sabic's Lexan polycarbonate sheet and systems, including high-insulating, nanogel-filled Lexan Thermoclear multiwall sheet for thecladding. The Lexan multiwall sheet typically delivers a combination of high thermal insulation and climate-control performance to enhance energy conservation, as well as light transmission for enhanced aesthetics and comfort, says the firm. The nanogel-filled Lexan multiwall sheet used on the translucent walls and ceilings of the ICEhouse offers energy savings of up to 50% compared to monolayer glass, says Sabic.
At this year’s edition of WEF, held in January, the ICEhouse was rebuilt, thus showcasing its structural design that enables fast assembly and disassembly on-site, and reuse in another location.
Also playing a key part in the ICEhouse’s design is the WonderFrame: a flexible structural system that can be erected quickly and that is made of locally available materials wherever WonderFrames are deployed. The patentpending structure consists of elements connected using simple tools, says Sabic.
The version assembled at Davos used aluminium for the frame material, but research is ongoing for using other feedstock as well such as plastics and bamboo.
First non-steel lift with a roomier design
Singapore Lift Company (SLC), a joint venture between Far East Organisation, Woh Hup and Pronus (HK), recently unveiled the world’s first composite lift. Made of lightweight composite materials and not steel, the cabin is said to weigh 150 kg or ten times lighter than similar-capacity lift that weighs 1,500 kg. Installation of the lift known as 8, which is mostly assembled offsite, is also comparably easier. Thus, it can be installed in a day, compared to the usual five work-days required for conventional lifts, plus no special labour skills are needed to install and maintain the lift and materials required are fewer, says SLC.
Alister Bennett, Managing Director of SLC, furthers
that the composite lift does not require complicated shaft
designs and the
substantial amount
of structural support
in the form of
concrete walls and/
or steel supports
to bolt on brackets
for the guide rails
and landing doors,
which are standard
requirements
in current lift
construction.
The composite materials used include carbon fibre-reinforced polymers (CFRPs), glass fibrereinforced polymers (GFRPs) and bioderived polymers. The non-steel innovation provides a solution to limited cabin space with the simplified structural design. The 8-cabin has been enlarged to be able to take on larger load. Noticeable, too, are the minimised overheads and pits commonly found in conventional steel-made lifts, points out SLC.
Currently, the lift, which can be used for the physicallychallenged, for home use or as a passenger lift, has been approved by Liftinstituut, one of Europe's certification organisations for lift and escalator systems. Certification from the Singapore Building and Construction Authority (BCA) is also underway, SLC informs. The company intends to make the lift commercially available later this year.
China’s first Disney resort is safely clad in FRP
The Shanghai Disneyland, a joint venture between The Walt Disney Companyand Shanghai Shendi Group features themed-lands that have been built with fire retardant composite materials to ensure safety while having fun.
One of the six themed lands, Tomorrowland, covering an area of over 2,300 sq m, is constructed from fire retardant (FR) gelcoated composite-moulded parts in several hundred different shaped and sized components.
All of the FRP components used for Tomorrowland were manufactured by Shanghai-headquartered composites fabricator E-Grow using a fire-approved laminate system comprising UK chemicals company Scott Bader’s aluminium trihydrate (ATH)-filled urethane acrylate resin, with a fire-retardant gelcoat.
Various sizes and shaped gelcoated FRP parts were produced by E-Grow including facades, passenger sections of a roller-coaster, parts of a character ride, a theatre, outdoor dining furniture and exterior cladding on the concourse and surrounding facilities. E-Grow says it used a unique, patented wax mould process to produce these parts.
The company assures that all FRP used in the park had to meet the Chinese B1 “reaction to fire” classification for fully assembled composite parts, as stipulated and tested by the Chinese National Inspection and Testing Centre for Building and Engineering Materials.
To ensure that the fire specifications were met, E–Grow says it used Scott Bader’s Crestapol 1212 acrylate loaded with 170 phr ATH as the backup resin. Also added were woven roving glass fibre reinforcements. It also met the requirement that all gelcoat be both fire-resistant and match the paint system so that should there be any damage to the paint surface the part would maintain its appearance. To meet these requirements, E-Grow used eight custom colours of Crystic Gelcoat 967 fire retardant pre-accelerated, thixotropic Iso-NPG polyester airless spray gelcoat. Scott Bader says the latter is used for the production of GFRP parts in the building and transportation industry in areas where fire resistance is a key requirement.
Sailing breakthrough with composites
French speciality chemicals company Arkema has made a
splash in sustainable boat construction with its Mini 6.50
monohull made entirely from recyclable thermoplastic
composite. Launched at JEC 2016 composites show last
year, the 6.5-m prototype’s recyclable hull and bridge are
constructed with Arkema’s carbon-reinforced Elium resin.
The prototype is the result of the Open Innovation
project involving Arkema and the Lalou Multi teams led by
French navigator Lalou Roucayrol. Designed to race across
the Atlantic Ocean, the boat is set to sail this year and is
now being optimised.
Meanwhile, Lexus, a division of Japanese car maker Toyota, has recently introduced its 42-ft open sport yacht for six to eight people. It is said to feature advanced styling, composite material construction and twin highperformance Lexus V8 engines. The upper deck and outer hull are seamlessly bonded around the inner structure; with each piece comprising a single massive hand-laid composite of two-part polyurethane (PU) epoxy resin reinforced with hand-laid woven carbon fibre cloth.
The yacht’s CFRP construction has made it nearly 1,000 kg lighter, compared to a similar yacht made from fibreglass-reinforced plastic. The underwater hull design is fashioned in a stepped design to reduce resistance or drag and improve handling balance at high speeds.
Powered by twin 5.0-l V8 gasoline engines, based on the 2UR-GSE high-performance engine of the Lexus RC F coupe, the GS F sport sedan and the new LC 500 grand tourer, the yacht, is a bespoke, one-off project and there is no intention to put it into production, says Lexus.
Lightest composite strands for seismic-proofing structures
In 2016, Japan was struck by more than 6,000 earthquakes, according to the Japan Meteorological Agency. Being earthquake-prone country, it has become standard to employ seismic isolation technologies in Japanese homes, buildings, and other structures. Technologies, such as vibration dampers and rubber bearing bases, are some of the widely used earthquake-resistance measures.
Existing structures are retrofitted with these technologies, but more often than not, spoil the buildings’ aesthetics.
A novel seismic technology has been developed by fabric specialist Komatsu Seiren. It is not only lightweight, weighing 12 kg per 160 m length, so “light” that a roll can be hand-carried, it is also flexible and soft to touch and at the same time not aesthetically intrusive.
The world’s pioneering composite seismic reinforcement called Cabkoma Strand Rod is a thermoplastic carbon fibre composite. It uses carbon fibre as the interlining, while its outer layer is covered with synthetic and inorganic fibres. It is finished by impregnation with a thermoplastic resin.
The rod has high tensile strength and strong structural body, while being the lightest seismic reinforcement in the world.
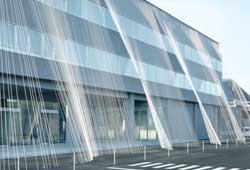
The company worked with Japanese architect Kengo Kuma to drape a curtain of composite rods on the building exterior of its three-storey headquarters, the Komatsu Seiren Fabric Laboratory (Fa-bo) located in Nomi-city, Ishikawa.
The composite strands are riveted from the roof to the ground to allow the Fo-ba building to move together during a tremor.
Pioneering carbon fibre tower in Asia
Kuala Lumpur-based telecommunications infrastructure services company Edotco Group claims the badge for deploying Asia’s first carbon fibre telecoms tower. The ground-based tower was installed in August last year at Taman Tasik Prima, Puchong, in Malaysia.
The carbon fibre structures, according to Edotco, weigh 70% less than conventional steel structures, hence reducing the foundation requirements by half, while providing high strength to weight ratio. A smaller footprint also requires fewer materials.
The carbon fibre has high rigidity with tensile strength ten times than steel, allowing the structure to better withstand harsher forces of nature (especially wind conditions). Installation time is 40-50% faster, Edotco said. Moreover, due to its high durability and corrosiveresistance, maintenance cost over the lifespan of the structure is lower. This therefore translates to about 20% lower total cost of ownership (TCO).
The company is aiming to lower TCO further by 40% as it becomes more experienced in the deployment of carbon fibre towers that will lessen customisation requirements. Edotco adds that the aesthetically pleasing tower is also a “green solution” as it emits less carbon dioxide during its production process.
The company also installed a first ever rooftop carbon fibre tower in Bangladesh last year. The installation is expected to precede future deployments to enhance connectivity initiatives in Bangladesh in support of its digital roadmap to 2021.
(PRA)Copyright (c) 2017 www.plasticsandrubberasia.com. All rights reserved.