Medical TPEs: akin to latex with non-allergenic and odour-free features

A new family of medical-grade thermoplastic elastomers (TPEs) for cast film provides the same elasticity, durability, and “feel” of latex without concerns regarding allergic reactions, odour, or residual curing agent. As thermoplastics, they make possible cost savings over latex and other thermoset rubbers, says compounder Teknor Apex Company.
The firm’s latex-free Medalist TPE film portfolio includes grades specifically designed for tourniquets and straps (Medalist MD-17340),
therapy bands and sheeting (Medalist MD-10233 and MD-13240), and dental dams (Medalist MD-10308). All are available worldwide as standard grades ready for use, though Teknor Apex is prepared to develop custom formulations to meet special requirements. Like other Medalist medical elastomers, the new compounds are made with FDA-compliant ingredients, are compliant with ISO 10993-5 and REACH SVHC, are free of phthalates, and are produced in ISO13485 facilities in the US and starting in January of 2017, in Singapore. Latex films are valued for their unique combination of elastic properties, including low ratio of force to elongation and low tensile set after elongation. The new Medalist compounds duplicate the elastic behaviour of latex while providing similar resilience and durability. They also exhibit similar haptics (tactile qualities) and draping behaviour, which is important in clinical settings.
While closely resembling latex in performance, the new Medalist compounds eliminate concerns about latex allergy symptoms, which can range from skin irritation to more severe manifestations. Also unlike latex, the TPEs are odour-free, and their processing does not involve use of curing agents that can be present in trace amounts in finished products.
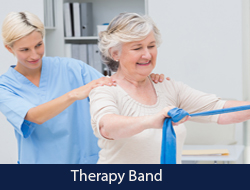
The company says its TPEs permit major cost savings over latex and other thermoset rubbers such as nitrile or neoprene. These are attributable to a lower per-pound cost, elimination of the curing step, and the inherently greater processing efficiency of thermoplastics.
The advantages of thermoplastic processing open new business possibilities for medical device companies, according to Ross van Royen, senior market manager of regulated products. “Rubber extrusion is complicated, in terms of both equipment and production methods. Because it is a lot easier and less expensive to set up a TPE extrusion process than one for rubber, companies may find it attractive to bring the manufacture of film products in-house rather than outsourcing it,” he adds.
(PRA)Copyright (c) 2016 www.plasticsandrubberasia.com. All rights reserved.