Also, download this story from the electronic issue here
With global demand for plastic pipes projected to rise 8.5% a year through 2017 to 11.2 billion m, it is no surprise that European extrusion machine makers are seeing a windfall in Asia.
Amut delivers compact line to Vietnam
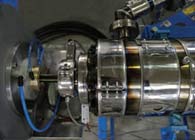
Italian manufacturer of pipe extrusion lines Amut has delivered an extrusion line for the production of PE100 pipes, with an external diameter of 1,000 mm, to Vietnam. A new compact extrusion die and an extruder with a capacity of 1,200 kg/hour have been specifically designed for this purpose. The die is provided with 16-spiral distributors to guarantee a wall thickness uniformity, while the extruder is based on bimetallic barrel and wear-proof coated screw.
Meanwhile, also in Asia, is a machine producing 63 mm-diameter HDPE pipes, based on an EA48 single-screw extruder for a capacity of 240 kg/hour.
Another line has been supplied to a Vietnamese customer to produce U-PVC pipes for electric conduits (diameters from 16-32 mm) based on a BA72 twin-screw extruder for a capacity up to 250 kg/hour, +/- 10%. A hot/cold mixing system for the production of powder PVC dry-blend completes the line. The heat mixer has a capacity of 200 l, while the horizontal cooling mixer has 500 l.
IPC made in China
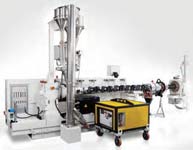
At KraussMaffei Berstorff’s open house early this year, at its Haiyan plant in China, it showcased a system that used the KME 90-36 B/R and the KM-RKW 36-630 IPC pipehead as its core components, along with a locally-produced internal pipe cooling (IPC) system. The line was shown producing 630-mm HDPE pipes.
In the growing PO pipe sector, there is great demand for productivity, efficiency and cost reduction among Chinese processors, says the German extrusion machine maker.
By means of a side channel compressor, the IPC system sucks ambient air at high speed against the haul-off direction through the centre of the pipe. As well as being cooled from the outside (using conventional processes with vacuum tanks and spray baths), the pipe is also cooled from the inside. This, thus, cuts the cooling zone by up to 40%.
The advantages include lower investment costs and footprint and no need for additional coolant as the system uses ambient air.
Tecnomatic delivers high output line for PE-RC pipes to Middle East
Italian company Tecnomatic has recently commissioned the Middle East’s first multi-layer line with a maximum pipe diameter size of 1,200 mm, and a capacity of up to 2,000 kg/hour. It was delivered to Muna Noor from Oman, which is part of Boubyan Petrochemical from Kuwait.

The company, which specialises in the production of 800 mm-PE pipes, has recently opened a new factory in Sohar to produce PP double wall corrugated sewer pipes of up to 1,200 mm, fittings and manholes and PE multilayer safety pipes.
With the new line, it is extending its product portfolio and introducing a new generation of pipes, produced under a technology license from Dutch firm Wavin Overseas, a part of the Mexichem Group.
Multi-layer pipe systems offer a practical solution to the installation and jointing of PE systems providing security, protection and durability. This new generation of pipes will be ideal for Oman’s poor and stony soils, which can produce high stresses in the pipe wall.
Material supplier Borouge’s BorSafe High Stress Crack Resistance (HSCR) PE100 is used for the multi-layer pipes. The material is ideal for rocky soil conditions where no imported pipe surround is available as they are equally resistant to Slow Crack Growth (SCG) caused by external surface damage and point loads. This material can therefore be used for pipes that are installed trenchless technology, ranging from the renovation of existing pipelines using insertions or pipe bursting techniques or for installing new pipes using high speed ploughing or horizontal directional drilling.
Tecnomatic’s extrusion line is equipped with three Vega extruders: two Vega 60.37 for the inner and outer layers and one Vega 90.37 for the middle layer. Features include low energy, thanks to an optimised screw design and AC motors, grooved feed zones, gearboxes, and industrial PC for process control with remote assistance.
Central to the line is the new Venus Multi 1,200 mm die head. Based on a three-spiral design, it ensures an optimal melt flow for a wide range of thickness ratios and represents a major milestone for the production of large diameter multi-layer pipes using HSCR materials. The die-head integrates compact dimension and low pressure build-up with consequent energy savings, Heating Cooling Systems (HCS) for constant internal temperature, even when high volumes of materials are involved. It allows for a production size range from 250-1,200 mm, producing three diameters per die-set up to 800 mm using the classic draw-down mode. For sizes above 800 mm, the swelling mode is preferred for better control of wall thickness distribution and pipe ovality. The die-sets comprise of two parts with a small end ring to define the gap of the die, permitting a rapid die change and regulation.
The die-head is complete with a hydraulic tilt function for an easy mounting operation and the Pipe Air Cooling (PAC) system, which provides intensive cooling of the inner pipe surface by sucking air in the opposite direction to extrusion. It, thus, ensures more uniform cooling 360 degrees around the pipe and through the thick wall, decreasing the differences in the pipe solidification rate and reducing the residual internal stresses. This also has the benefit of reducing the wall thickness eccentricity and ovality whilst providing a short line or higher output compared to a standard line without inner cooling.
The line is synchronised using gravimetrics on each extruder, working in connection with a 16 sensor ultrasonic system.
To cool down 250-1,200 mm-diameter pipes and for wall thicknesses up to 88.2 mm, the line is equipped with two 18 m-vacuum baths.
The downstream equipment includes a haul-off, with ten caterpillar tracks, each one controlled by an independent vector AC motor and a planetary saw with knife cutting and universal clamping device, for swarfless pipe delivery.
Profile Dies’s focus on drip irrigation pipe lines
Profile Dies has developed in the last two years new automated extrusion lines for the production of drip irrigation pipes with flat drippers, which reach a maximum speed of 150 m/minute and are able to insert up to 800 drippers/minute.
The 20-year old Italian firm also has extrusion lines for the production of round drip irrigation pipes with a production speed between 80 and 100 m/minute and inserting capacity up to 400 drippers/minute, to produce pipes with diameters from 16 to 20 mm.
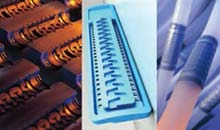
Still with a view to developing solutions for the irrigation field, Profile Dies has recently delivered a new extrusion line for the production of drip-tape. This irrigation system is extremely cheap and is suitable for both crops in open fields and gardens. It is easy to install and to remove after use, thanks to the low thickness of the pipe.
The technical specifications of the new line include: a maximum output of up to 200 m/minute; spacing (distance between holes) of between 10 and 15 cm and minimum wall thickness of 5-6 mils.
Sica showcases updated equipment at open house
Italian company Sica, which recently celebrated its 50th anniversary, showcased 15 machines at an open house in mid-July. On display there were the TRK/C 2500 swarfless cutting machine for PE pipes up to 2,500 mm. It also had the TRS 160W cutting machine for cutting and chamfering, without removal of material, for PVC, PP and PE pipes up to 160 mm.
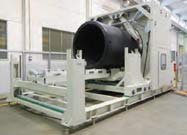
Other equipment on display included the Unibell1 200 JRE electric belling machine for PVC pipes up to 200 mm. It has an IR-SW short-wave oven and is characterised by the electromechanical movement of the forming carriage and the elimination of hydraulic drives. A screw jack, connected to a latest generation brushless motor with resolver, allows a precise mandrel positioning in a closed loop with a high mechanical efficiency (up to 70%) and low noise level. Without the need for oil cooling, this solution also allows a reduction of water use while oil leakages are avoided and ordinary maintenance is reduced.
Sica also showcased its Everbell4 200 PSP multi-belling machine for PP sewage pipes of up to 200 mm. It has been redesigned with new pipe heating in a single IR-SW oven, and both mandrel and flange electromechanical movement. This, the company says, allows for high speed with accurate positioning of the belling tools, easy process parameters setting from the operating panel, energy efficiency, low noise level, and system reliability. Since it sockets PP pipes, it is equipped with the Permanent Socket Profile feature.
(PRA)