Electronics: Making fire retardants safer and cleaner
Fire safety, amid a rapidly evolving technological landscape, is a crucial concern. It hinges on the efficacy of flame retardants (FRs) used in plastics for the electronics sector. Yet, recent research highlights that the perceived safety of FRs may be overstated, raising concerns about the impact on both the environment and human health. How are manufacturers addressing these emerging challenges, asks Angelica Buan in this report.
Recent years have witnessed remarkable progress in flame retardants (FRs) – substances added to materials like plastics, textiles, and coatings to curb fire spread. With technology’s growing integration in our lives, the demand for effective and environmentally friendly FRs has surged. Striking the right balance between innovation and safety is paramount.
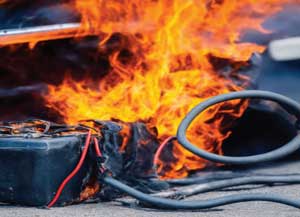
FRs have been in use since the 1970s, but concerns have surfaced regarding potential health risks tied to their exposure. Ongoing research highlights that while these chemicals can be advantageous in specific applications, they might pose harm to both humans and animals. Negative effects include disruptions in endocrine systems, immune function, reproduction, cancer susceptibility, and impacts on fetal and child development.
Different types of FRs exist, including brominated and chlorinated variants often used alongside antimony. Examples include polybrominated diphenyl ethers (PBDEs) and hexabromocyclododecane (HBCDD). Organophosphorous and inorganic alternatives, like tris (2-chloroethyl) phosphate and aluminium hydroxide, are also prevalent. Some FRs, like PBDEs, can be hazardous. Harmful chemicals can also be present in plastic waste, raising environmental and health alarms.
Advancing technology has led to more intricate devices producing heightened heat during operation, amplifying fire risks. Thus, FRs play a vital role in mitigating these hazards, particularly in electrical and electronics (E&E) sector. Modern FRs not only strive to prevent fires but also minimise their ecological and health impacts.
Halogenated flame retardants, materials of concern
Halogenated FRs are commonly used but problematic due to health and environmental concerns. Some have been banned or phased out, but there are still untested types likely to pose similar risks, according to the Green Science Policy Institute, which works with the industry and NGOs to limit the use of FRs for safer furniture, electronics, and building insulation.
Halogen-free FRs, positioned as safer alternatives, gained a market worth of US$2 billion in 2022. This sector is projected to grow from US$2.2 billion in 2023 to US$3.4 billion by 2032, with a CAGR of 5.65% through 2030, according to Market Research Future.
Thus, Boston-based company CAI Performance Additives has developed a halogen-free FR for PC films/sheets. This additive, ST-SR487, allows for UL94 V-0 certification in 0.25-mm-thick PC film, offering a safer alternative to halogen-based solutions containing bromine, iodine, or chlorine. It also resists yellowing, weathering, and provides hydrolysis protection for water-contact products.
Additives for fire-safe plastics
The increasing demand for FR solutions in plastics and composites across industries like electronics, construction, and automotive, coupled with stricter fire safety standards, is driving the need for sustainable FR chemicals.
The increased usage of polymers in the automotive industry, as well as the growing concern about environmental protection from harmful compounds used in E&E, all contribute to this trend. German chemicals company BASF and specialty biocide supplier Thor have teamed up to provide comprehensive nonhalogenated FR additive solutions.
Both companies are active members of the Phosphorus, Inorganic, and Nitrogen Flame Retardants Association (PINFA), a sector group within the European Chemical Industry Council (CEFIC) and representing the manufacturers and users of non-halogenated phosphorus, inorganic and nitrogen FRs, emphasising non-halogenated options.
The companies’ combined expertise in FR additives demonstrates the synergistic benefits of integrating BASF’s halogenfree Flamestab, with Thor’s phosphonates Aflammit technology.
Prolonging device lifespan with anti-corrosion materials
BASF has expanded its range of polyphthalamide (PPA) offerings with FR grades that offer a blend of high thermal stability, electrical insulation, and low water absorption. These PPA grades feature high electrical RTI values (Relative Thermal Index) above 140°C and are halogen-free, according to EN 50642 standards, preventing corrosion and failure of electrical parts in humid conditions.
These non-halogenated PPAs, derived from materials like PA9T, PA66/6T, PA6T/66, and PA6T/6, also allow for improved colourability and colour stability. This expansion by BASF offers a tailored portfolio for E&E applications, creating new possibilities for uses like power or data transmission connectors in vehicles, appliances, consumer electronics, as well as e-mobility components, miniature circuit breakers, switchgear, and sensors.
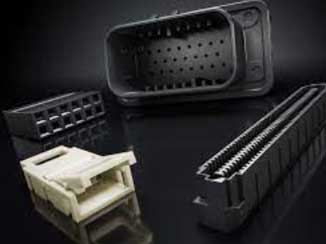
As well, BASF emphasises that its materials respond to new trends, such as halide-free heat stabilisers, to prevent contact corrosion in sensitive components exposed to heat and moisture, ensuring the longevity and proper functioning of E&E devices.
BASF’s product range includes the easily processable Ultramid One J 60X1 V30, a PA66/6T obtained from Belgian firm Solvay. Paired with the PPA pioneer Ultramid TKR 4340G6 (PA6T/6), it is said to boasts the highest electrical RTI value of 160°C alongside straightforward processability.
Another standout is PA9T Ultramid Advanced N3U41G6, with an electrical RTI of 150°C and minimal water absorption, crucial for Surface Mount Technology (SMT) processing. Meanwhile, Ultramid Advanced T2340G6, a PA6T/66, showcases improved flowability and an electrical RTI of 150°C, making it well-suited for wire-to-board and board-to-board connectors.
Cleaner flame-retardant resins from bio-circular sources
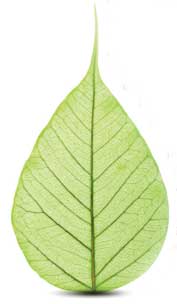
Meanwhile, chemical firm Sabic is offering biobased versions of its Noryl resin line, with a range that includes several variations, such as Flexible Noryl, Noryl GTX, and Noryl PPX. These resins are developed using polyphenylene ether (PPE) blended with other materials like HIPS, PP, PA, or TPE, along with additives and fillers.
The biobased, non-brominated/ non-chlorinated FR resin, Noryl NH5120BIO4, is targeted at applications like enclosures and housings; HVAC components, and PV/solar junction boxes. With a UL flame rating of V1 at 1.5 mm with no intentionally added per and polyfluorinated substances (PFAS), these resins provide a balance of heat resistance, flow, hydrolytic and dimensional stability, and creep performance, while retaining good mechanical properties in harsh outdoor environments.
Elsewhere, German materials firm Covestro now also offers a PC with a 90% recycled content of plastic from post-consumer waste (PCR) that can be used in consumer electronics, among other applications. The carbon footprint of the new Makrolon PCR PC resin is 70% lower than that of a comparable fossil-based virgin plastic and is part of the CQ portfolio of circular solutions at Covestro. The company plans to initially offer this grade in the Asia-Pacific region.
The PCR grade is manufactured with halogenfree FRs that meet performance requirements without increasing environmental impact. It also meets the highest V-0 rating of Underwriters Laboratories’ UL 94 flammability standards.
Covestro’s Bayblend FR3010 R75 PC blend is used, for example, in the ear cups of Danish brand Jabra’s latest Evolve2 headset series for audio equipment and video conferencing systems. This type is made of 75% recycled material and has a 50% lower carbon footprint.
(IMA)Subscribe to Get the Latest Updates from IMA Please click here
©2023 Injection Moulding Asia. All rights reserved.