Clariant: Invests further in new China FR facility for E/E sector; launches catalysts for purifying pyrolysis oil from mixed plastic waste
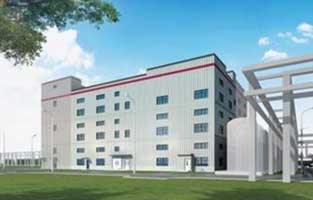
Swiss chemical firm Clariant will create a second production line at its new CHF60 million facility for Exolit OP halogen-free flame retardants (FRs) currently under construction in Daya Bay, China. This additional CHF40 million investment will further expand access to sustainable fire protection solutions and related technical expertise to support the significant growth of engineering plastics applications in E-mobility and electrical & electronic segments.
The new Daya Bay flame retardant plant will supplement the capacity of Clariant’s two Exolit OP plants in Knapsack, Germany and is beneficial to the global customer base. Despite the external challenges of Covid, logistical and supply chain issues, Clariant is still targeting its original timeline, i.e. commencing production in Daya Bay around mid-2023, with the second line due to come on stream within 2024.
Clariant adds it will produce its global range of patent-protected organophosphorus flame retardants on site. The team at the Shanghai One Clariant Campus will support customers in the joint development and in-application testing of flame retarded solutions.
Both new flame retardant production lines will share infrastructure and built-up capabilities in place at Clariant’s Daya Bay site. Local resources are being used for the facility, with a focus on safety, says Clariant.
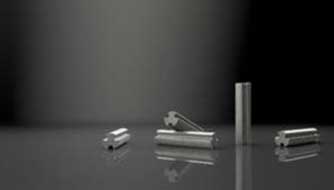
Meanwhile in related news, Clariant says it has launched a portfolio of flexible, custom solutions for the emerging market of chemical plastics recycling.
The new HDMax catalysts and Clarit adsorbents are designed for the purification of pyrolysis oil made from hard-to-recycle mixed plastic waste. Tailored to remove a wide range of contaminants that are continuously changing in the feed, the new products provide the flexibility producers need, regardless of process configuration. Clariant’s solution also includes operational assistance from startup to process optimization, which continues throughout the lifetime of the product.
As a result, producers benefit from highly efficient impurity removal to achieve pyrolysis oil that is compatible with ethylene plants.
Pyrolysis oils are made from a chemical recycling process that breaks polymers down into basic building blocks to be used for new feedstock streams. Since the process helps to reduce the environmental burden created by plastic waste that would otherwise be incinerated or landfilled, it enables a circular value chain for the production of base chemicals.
Jens Cuntze, President of Catalysts at Clariant, said, “The development of more sustainable catalyst technologies is crucial as we support our customers’ move toward a more circular economy with alternative feedstock sources. Our portfolio reflects not only our flexibility and commitment to our customers, but also our pledge to deliver innovation-driven sustainability.”
Nina Karpynec, Head of Marketing, Innovation, and Sustainability, Business Unit Adsorbents & Additives at Clariant, added, “Clariant is well-positioned for the decontamination of pyrolysis oil, drawing upon over 100 years of expertise in the purification of edible oils and of feedstock for renewable fuels. The company has a long history of producing adsorbents for a variety of feedstocks and contaminants, especially with heavy and broad distillation ranges.”
(IMA)Subscribe to Get the Latest Updates from IMA Please click here
©2022 Injection Moulding Asia. All rights reserved.