Green tie-ups: Borealis/Vipac offer sustainable BOPP packaging; Tupperware’s coffee cup goes eco
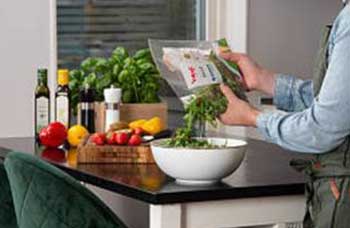
Austrian chemical firm Borealis and Vibac Group, specialising in biaxially oriented polypropylene (BOPP) applications, have developed new and more sustainable BOPP-based film for food applications. Vibac’s “V-Fresh” BOPP film is produced with a grade from the Bornewables portfolio of circular polyolefins derived entirely from waste and residue streams. Because it is designed for recycling (DfR), the packaging can be easily sorted in PP waste streams for mechanical recycling, thus helping increase the recycling quotas of flexible packaging formats.
PP is widely used in the flexible packaging industry thanks to its cost and resource efficiency. When used for food-safe packaging formats such as bags and pouches for e.g., salad, fresh products and cut vegetables, the protective properties of PP help extend the shelf life by retaining freshness and minimising unnecessary food waste. Film converters are also looking to improve the sustainability profile of their packaging film solutions.
To lower CO₂ emissions and help address the issue of climate change, converters can now rely on the grades in the Bornewables portfolio of circular polyolefins. Derived solely from waste and residue streams, Bornewables grades are drop-in solutions that offer the same performance properties as virgin PP, yet with a substantially lower carbon footprint. Converters can use the Bornewables on existing equipment without having to invest in new machinery. The newly developed, monomaterial BOPP film can be easily integrated into PP mechanical recycling streams, thus upping recycling quotas for flexible packaging formats.
“The combination of our BOPP film expertise with the polyolefins and recycling know-how provided by Borealis enables us to satisfy consumer demand for more climate-friendly packaging,” says Alberto De Paoli, Vibac General Director. “At the same time, we can still deliver the safety, freshness, and top-notch organoleptic qualities shoppers have come to expect.”
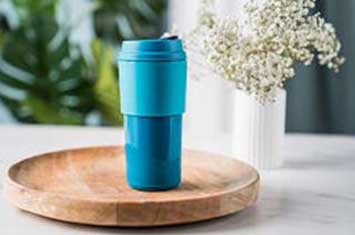
Meanwhile in yet another sustainable packaging example, Borealis has tied up with household brand name Tupperware to extend the Tupperware ECO+ product line to include a coffee to go cup made using renewable feedstock.
Based on the proprietary Borstar Nucleation Technology, Bornewables RG466MO is a sustainable PP random copolymer with organoleptic properties. Using this grade instead of virgin polyolefins enables Tupperware to further reduce the carbon footprint of its ECO+ product line.
Since its founding in 1946, Tupperware has offered functional and innovative kitchen and home products that offer an alternative to single-use items. As reuse pioneers, the company took additional steps towards greater sustainability by launching its ECO+ product portfolio in 2019. Tupperware has since been successively expanding the range of more environmentally conscious material solutions used in production to reduce the carbon footprint of its wares.
Tupperware has long used the PP random copolymer BorPure RG466MO in production. Because RG466MO is based on the proprietary Borstar Nucleation Technology, it offers faster cycle times and lower processing temperatures in the production process. As well, the stiffness/toughness balance enables the production of durable and robust items like the ECO+ coffee to go cup, which is now composed of 100% Bornewables RG466MO. Drinks can be safely stored and transported while maintaining temperature and taste in the reusable and attractive Coffee to go cup, which itself is fully recyclable at end of life.
Like all Bornewables grades, the commercially available Bornewables RG466MO is made using renewable feedstocks derived solely from waste and residue streams. ISCC PLUS certification according to the mass balance model ensures that sustainable content can be tracked and verified along the entire supply chain.
“The ECO+ Coffee to go cup, brings together the core components of our cascade model for plastics circularity: Reuse rather than single-use. Use of renewable rather than fossil-based feedstock,” explains Peter Voortmans, Borealis Global Commercial Director Consumer Products. “And at end of life, we recycle the Coffee to go cup rather than throwing away a valuable material resource. This is a prime example of how we are working with our partners to re-invent essentials for more sustainable living.”
“Extending our ECO+ product line to include more products manufactured with renewable feedstock shows our commitment to reducing waste at every step of the product life cycle,” says Sophie Wolters, Vice President of Product & Category Management at Tupperware.
(IMA)Subscribe to Get the Latest Updates from IMA Please click here
©2022 Injection Moulding Asia. All rights reserved.