Recycling: Covestro/Hasco join forces for recycling PC auto parts; Solvay/Ostium to recycle polymers in single-use surgical instruments
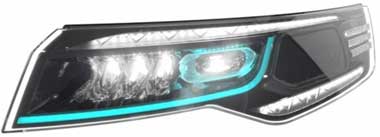
Covestro is cooperating with Chinese automotive lighting manufacturer HASCO Vision to recover used polycarbonate from the production of headlamps, which can be reused for new automotive components. The photo shows a headlamp designed by Covestro.
With the automotive industry driving itself towards a circular and climate neutral future, the use of alternative materials, including those containing recycled content, to replace fossil resources has become more and more commonplace. However, the quality and traceability of such recycled materials are still of a major concern.
In light of this, materials manufacturer Covestro has formed a partnership with China’s leading auto lighting supplier Hasco Vision to build a closed-loop recycling business model that would guarantee the plastics recycled from the manufacturing of automotive lamps are both of high quality and traceable.
A long-standing partner of Hasco Vision, Covestro has for many years been supplying the Chinese company with plastic material polycarbonates to manufacture automotive lamps.
Now, Covestro will also join hands with other partners in the recycling industry to retrieve used plastics from Hasco’s manufacturing sites before turning them into high-quality post-industrial recycled (PIR) polycarbonates and polycarbonate blends that Hasco can use to produce new automotive components.
Lily Wang, Head of the Engineering Plastics segment at Covestro, said, "This collaboration, which allows full transparency and traceability along the value chain, will ensure the supply of consistently high-quality PIR plastics to meet the growing demands for more sustainable materials and lower emissions in the automotive industry. We look forward to working with more customers on similar initiatives that close the carbon loop."
The closed-loop recycling of post-industrial plastics is an effective sustainability solution as such recycled materials have "virgin-like" quality, are easily traceable and help reduce the carbon footprint of vehicles compared with conventional fossil-based materials.
Covestro says it has for many years been focused on developing the recycling of plastics. In 2020, the company struck up a partnership with China’s leading beverage maker Nongfu Spring to recycle 19-l polycarbonate water barrels into materials that can be used in the electrical and electronics, home appliances and automotive industries.
In other news, Belgian chemical firm Solvay is partnering with French start-up Ostium in single-use surgical instruments material recycling. The joint project is designed to enable the mechanical recycling of end-of-life single-use surgical instruments moulded in glass-fibre reinforced Ixef polyarylamide (PARA) from Solvay’s portfolio of specialty polymers.
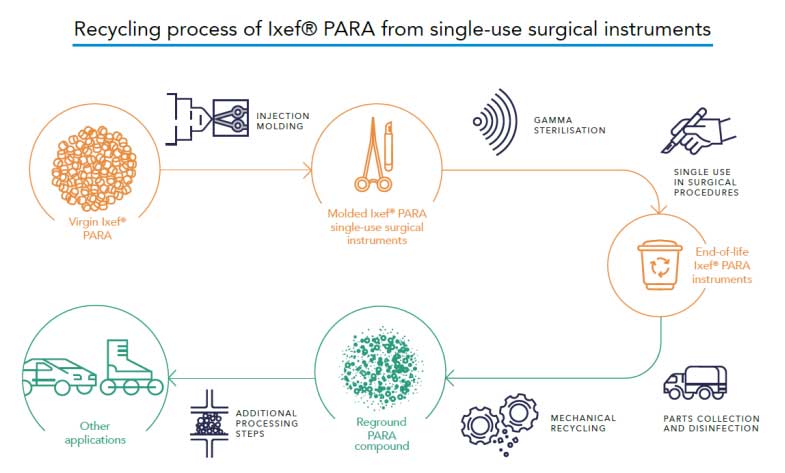
The initiative is the first for valuable polymers to be recycled and upcycled from used healthcare devices, proving that the medical safety provided by high-performance polymers such as Solvay’s Ixef PARA in single-use surgical instruments, can be reconciled with the need for greater sustainability and resource efficiency, says Solvay.
“Our customers in the healthcare industry must meet strict regulatory demands, while at the same time striving to minimise the carbon footprint of their products and support the reduction of hospitals and clinics' end-of-life waste,” says Claire Guerrero, Global Marketing Manager Sustainability at Solvay.
Ostium Group, a French start-up specialising in the design and manufacture of instruments for hip, knee, shoulder, and trauma orthopedic surgery, will supply hospitals with new custom surgical kits made with Ixef PARA and collect the contaminated instruments after use.
This will also promote the replacement of metal surgical instruments with lightweight polymer designs and help medical facilities reduce their time and cost for sterilisation, and disposal as well as lower their carbon footprint.
The partnership with a regionally recognised leader in the treatment and recycling of waste from healthcare activities with infectious risks, was key to developing a dedicated mechanical process to clean, sort, and grind the collected material, delivering high-quality polymer feedstock that can be used in the production of new polymers.
Finally, Solvay adds it is evaluating upcycling options and how to integrate back this recycled feedstock into new high-performance PARA compounds. Initial trials have shown that the recycle-based PARA compound provides a high level of performance, with up to 85% of flexural properties and no loss in surface appearance when compared with the virgin grade, with the additional advantage of a lower carbon footprint.
In view of regulations in place in the healthcare market with constraints on the use of recycled materials, Solvay says it is targeting open-loop downstream solutions in which the recycled material will find a second life in high-end markets such as automotive and sports and leisure equipment.
(IMA)Subscribe to Get the Latest Updates from IMA Please click here
©2022 Injection Moulding Asia. All rights reserved.