Green expansions: TotalEnergies ups production of rPP for auto sector; Covestro turns to biotechnology for biobased aniline
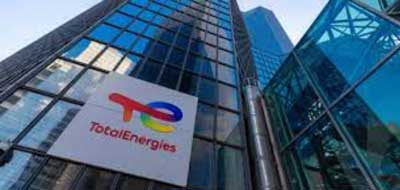
French petrochemical firm TotalEnergies is constructing a new production line of high-performance recycled polypropylene (rPP) for automotive in its polymer plant in Carling, France. With commissioning scheduled for 2024, the flexible line will produce 15,000 tonnes/year of polypropylene compounds containing up to 100% recycled plastic materials.
Since 2016, the Carling-Saint-Avold petrochemical platform is producing value-added compounds primarily intended for the automotive industry. The startup of a new line dedicated to hybrid compounds will consolidate the platform’s position of a leading polymers site in Europe, it adds.
Part of TotalEnergies’ recently launched RE:clic portfolio, and more precisely the RE:use polymers range obtained through a mechanical recycling process, these low-carbon materials meet the highest quality standards and technical requirements for automotive, it claims.
Recycling both post-consumer wastes and end-of-life automotive parts, the line will contribute to address the challenge of the circular economy in Europe.
"After the doubling of capacity at Synova, a subsidiary of TotalEnergies and the French leader in the production of recycled polypropylene, this investment further strengthens the Company’s leading position in high value-added recycled polymers. This new line will allow us to meet the growing demand from the automotive market for more efficient and sustainable polymers, in line with our ambition of producing 30% circular polymers by 2030,” said Nathalie Brunelle, Senior Vice President, Polymers at TotalEnergies.
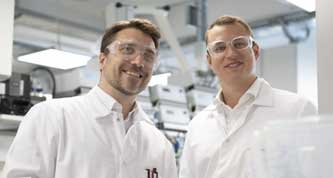
In other news, German materials firm Covestro says it is expanding its competencies in industrial biotechnology. The plastics manufacturer intends to make increasing use of microorganisms and enzymes to make its products and processes even more sustainable.
Specifically, Covestro says it is already using biotechnology to research and develop new ways to sustainably produce aniline, which is the raw material for the MDI precursor that is used to make insulating foam for buildings and refrigeration equipment. Until now, aniline has been obtained almost exclusively from fossil raw materials.
Covestro adds that it has developed a pioneering process to produce aniline from plant-based raw materials such as straw or sugar beet plants in an environmentally compatible way using microorganisms. Fully biobased aniline has already been obtained in this way and successfully processed into test products. Now the process, which has already won several awards, is to be further developed on a larger scale. The project is funded with public funds from the German Federal Ministry of Food and Agriculture.
Another precursor for coatings and adhesives (HMDA) can already be produced on a larger scale from plants and with the aid of biotechnology. Covestro and US-based biotech company Genomatica have succeeded in doing this through a partnership.
Furthermore, new recycling processes based on biotechnology are also to be developed. To this end, the biotechnology competence centre, which has been in operation for four years, has now been expanded to include a publicly funded research group. At the same time, Covestro is making progress in its efforts to produce the important chemical aniline entirely from plants for the first time with the help of microorganisms.
In order to better tap the potential of industrial (“white”) biotechnology for plastics production, the junior research group enzyme catalysis, or NEnzy for short, has now been established at Covestro. It will receive a total of EUR2.5 million in funding from the German Federal Ministry of Education and Research for five years and is cooperating closely with RWTH Aachen University in Germany.
The new group is working to recycle end-of-life products and plastic waste through enzymatic recycling. The researchers also want to use enzymes to treat wastewater in plastics production. Another focus is the targeted and complete decomposition of used plastic in nature.
The experts now also have more space and even better equipment – in a new laboratory that Covestro has built at its headquarters in Leverkusen. Here, biotechnological processes can be represented in a particularly realistic way in a wide range of sizes, from one milliliter to soon 100 liters of reaction volume.
(IMA)Subscribe to Get the Latest Updates from IMA Please click here
©2022 Injection Moulding Asia. All rights reserved.