Green materials: Lanxess adds on sustainable options for polyols, oxidation products; Asahi Kasei/Microwave Chemical launch demo project for chemical recycling of PA66

German specialty chemicals company Lanxess says it has added more sustainability in its portfolio of polyols and oxidation products (POP): The Advanced Industrial Intermediates (AII) business unit now offers more sustainable solutions for around 80% of its POP portfolio. Seven of the nine products, including the chemicals trimethylolpropane (TMP), adipic acid (ADA), 1,6-hexanediol (HDO) and phthalic anhydride (PSA), have already successfully completed Lanxess’s internal Scopeblue certification. The remaining ones are to follow soon.
With the Scopeblue brand label, Lanxess marks products that either exhibit a sustainable raw material content of more than 50% or offer a carbon footprint of less than half of that of their conventional counterparts. To demonstrate the use of sustainable raw materials along the entire value chain, Lanxess has had its production facilities in Krefeld-Uerdingen certified by TÜV Nord to the internationally recognised ISCC PLUS sustainability standard.
The new sustainable TMP Scopeblue contains around 54% n-butyraldehyde produced from biogas and offers the same properties as the conventional variant.
Maria Guixà, Global Marketing Manager TCM (Trimethylolpropane, Calcium Formate and Maleic Anhydride) at Lanxess, says “As our product has a very broad application portfolio we see great potential here. Among others, TMP is used for the production of coatings, resins, UV-curable coatings as well as for polyurethane applications.”
The Scopeblue variants of adipic acid and 1,6-hexanediol, for example, are produced from bio-based or bio-circular cyclohexane. As a result, they have a significantly improved carbon footprint compared with conventionally manufactured products.
“As early as 2021, we were able to offer a certified carbon footprint for our portfolio for the first time and generate added value for our customers through this transparency,” says David Berhorst, Head of Marketing AHP (adipic acid, 1,6-hexanediol, phthalic anhydride) at Lanxess.
Thanks to the two nitrous oxide reduction facilities in the adipic acid plant, which decompose the nitrous oxide generated in the production process, Lanxess has already been able to manufacture these basic chemicals with significantly lower emissions than is usual in the market.
Raw materials offer the greatest leverage for further improving the carbon footprint of POP products. This is also emphasised by Eric Hendricks, Sustainability Manager at the Business Line POP. The company is therefore working on replacing more raw materials with “green” variants.
“There is not yet an alternative for everything,” says Hendricks. “We are working on solutions here with partners along the entire value chain to position ourselves clearly and early on the supply side as well.”
The main demand for the sustainable POP products currently comes from Europe. But Lanxess also sees potential in the Asian and American markets – because competitors there do not yet have any green alternatives in their portfolios.
Meanwhile in other news, Asahi Kasei and Microwave Chemical have launched a joint demonstration project with the objective of commercialising a chemical recycling process for PA66 using microwave technology. The process utilises microwaves to depolymerise PA66 and directly obtain the monomers hexamethylenediamine (HMD) and adipic acid (ADA), which is expected to be accomplished at high yield with low energy consumption. The monomers obtained can then be used to manufacture new PA66. In the demonstration, scraps from manufacturing and post-use waste material of PA66 for airbags and automobile parts are depolymerised.
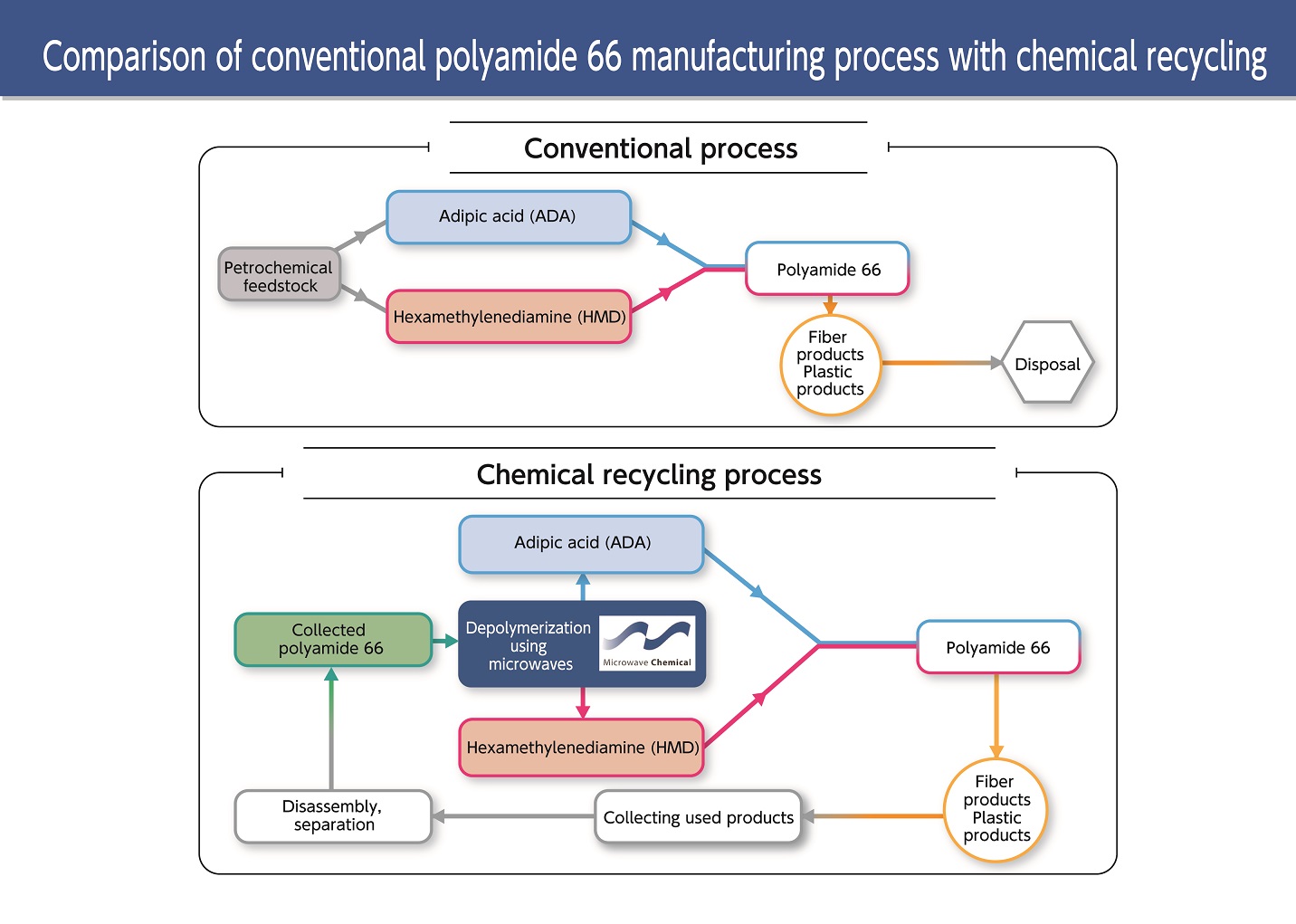
Asahi Kasei produces fossil fuel–derived hexamethylenediamine (HMD) and adipic acid (ADA) as intermediates to manufacture Leona PA66, an engineering plastic featuring outstanding heat resistance and rigidity. PA66 is used in various applications, including plastic parts for automotive and electronic products, and yarn for airbag fabric, and its demand is expected to increase worldwide.
As the world moves toward carbon neutrality, attention is increasingly focused on manufacturing processes for reducing greenhouse gas (GHG) emissions from chemical products derived from fossil fuels. Microwave Chemical is promoting technological and business development to achieve carbon neutrality in the industrial sector focused on process development using microwaves, which can directly and selectively heat target substances with high energy efficiency. For chemical recycling, Microwave Chemical is advancing its proprietary PlaWave technology platform for decomposing plastic using microwaves.
Through development combining Asahi Kasei's experience in manufacturing HMD and ADA for more than half a century together with Microwave Chemical's achievements in the industrialisation of microwave technology, the two companies aim to commercialise a manufacturing process for PA66 that can reduce GHG emissions compared to the conventional manufacturing process.
Laboratory-scale studies that began in fiscal 2021 have confirmed the high-yield depolymerisation of PA66 using microwaves, as well as the principle of the separation and purification process after depolymerisation.
Bench-scale equipment will now be assembled at Microwave Chemical’s Osaka Factory by the end of fiscal 2023, and a small-scale demonstration trial using this equipment will be performed in fiscal 2024 to collect basic process data for commercialisation.

Microwave Chemical’s PlaWave technology platform for decomposing plastic using microwaves can depolymerise PA66 with low energy and obtain HMD and ADA monomers in high yield.
The manufacturing process for PA66 using HMD and ADA obtained by depolymerisation with this technology is expected to reduce GHG emissions compared to the conventional PA66 manufacturing process, while further reduction of GHG emissions may be achieved by the use of renewable energy for the power required to generate the microwaves.
By verifying the process from depolymerisation to separation and purification in an integrated manner, this demonstration project aims to enable resource circulation of PA66 for further reduction of GHG emissions.
Moving forward, based on the results of the small-scale demonstration trial, a decision on the possibility of commercialisation will be made by fiscal 2025 following detailed analysis. Concurrently with the small-scale demonstration trial, construction of a business model that involves the entire value chain in the chemical recycling of PA66 will be advanced, aiming to achieve a circular economy together with stakeholders in the PA66 value chain.
Microwave Chemical is working to increase the scale of equipment and to make PlaWave more generally applicable in order to achieve the practical application of the chemical recycling of polymethyl methacrylate (PMMA, also called acrylic resin), automotive shredder residue (ASR), plastic containers and packaging, flexible polyurethane foam, etc.
(IMA)Subscribe to Get the Latest Updates from IMA Please click here
©2023 Injection Moulding Asia. All rights reserved.