Expansions: PPG to expand auto OEM coatings in Germany; Sibur licenses ethylene-hexene tech to Technip Energies
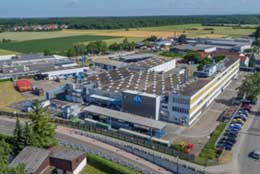
Chemical firm PPG says it will invest over US$10 million to expand production of automotive OEM coatings at its site in Weingarten, Germany. PPG is constructing a 10,000 sq ft addition to its existing facility with a capacity to produce more than 5,000 tonnes/year of waterborne basecoats. The expansion is expected to be complete in the second quarter of 2022.
According to PPG, waterborne technology replaces the solvents found in traditional basecoats with distilled water, providing less odour and improved air quality in the work environment. This project is part of a series of investments PPG is making in its automotive OEM coatings production in Europe, including expanding basecoat production at its site in Valladolid, Spain, as well as the recently announced expansion of its clearcoat production in Erlenbach, Germany. These investments will reportedly help PPG lower its operational carbon footprint in total by more than 1,000 tonnes/year of CO2 equivalent.
“This is an important investment to strengthen our production capabilities in Europe and to ensure that we are leveraging our industry-leading waterborne technology to drive downstream sustainability, helping our customers meet their sustainability goals,” says Roald Johannsen, PPG vice president, automotive OEM coatings, Europe, Middle East and Africa.
Johannsen adds, “These investments in capabilities to produce more sustainable products, together with our focus on coatings for the next generation of electric vehicles, will ensure that we continue to create value for our automotive customers in the future.”
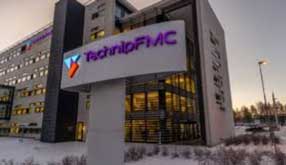
Meanwhile in other news, Russian petchem firm Sibur has partnered with global engineering company Technip Energies to licence its technology for producing 1-hexene, a co-monomer used to make LLDPE and HDPE. The technology, known as HEXSIB, was developed by NIOST – one of Sibur’s main R&D centres.
1-Hexene can be used to make LLDPE and HDPE and is an essential component of speciality PE grades that offer premium quality and boast much better properties than commodity grades. For example, 1-hexene helps reduce the amount of plastic used in each end product and lower the environmental footprint by providing the same barrier properties to a thinner film.
The partnership between Sibur and Technip Energies is expected to produce licence agreements with international polyolefin makers and seeks to integrate the former’s technology into complex design solutions to build new manufacturing capacities for advanced PE grades.
“The agreement with Technip allows to strengthen engineering platform of the Sibur's technology and gives the opportunity to promote it through Technip's partner network,” said Darya Borisova, a member of Sibur's management board and head of R&D. “Sibur is currently selecting a site within the group's range of facilities for production of hexene-1 with the HEXSIB technology to satisfy its own and market needs as the company expands its portfolio of high value grades and share of co-monomers”.
In terms of technical and economic parameters, Sibur says its technology is on par with global benchmarks. For example, the HEXSIB process requires milder conditions when it comes to temperature and pressure. Coupled with the use of less capital-intensive equipment, it ensures high energy efficiency and low feedstock consumption compared to alternatives. Furthermore, unlike some of the already available international technologies used to make a variety of co-monomers, HEXSIB produces polymer-grade hexene at a high selectivity, minimising the output of other olefins.
“We are very proud to promote this relevant and reliable technology,” says Stan Knez, Technip’s Senior Vice President, Process Technology. “It yields a quality product that can be used at existing polyethylene facilities.”
(IMA)Subscribe to Get the Latest Updates from IMA Please click here
©2022 Injection Moulding Asia. All rights reserved.