Recycling: Covestro to build pilot plant for recycling of PC in Germany; Nexam Chemical receives patent for recycling PE
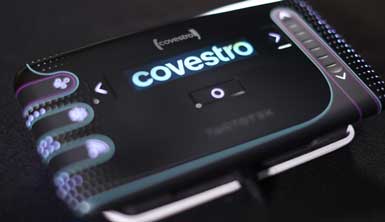
German materials firm Covestro that has developed a process for recycling polycarbonate, i.e. polychain plastics is now looking at the technical implementation of chemical recycling on a pilot scale in Leverkusen.
In this process, plastics are converted back into their monomers, a precursor of plastics, so that they can be fed back into the production process as alternative raw materials. On the way to industrial scale, the process is still being optimised and is undergoing further development stages.
"As a manufacturer of plastics such as polycarbonate, we naturally have a responsibility in dealing with these important materials, including at the end of their product life. Our advantage is: we know how our products are designed and can therefore conduct targeted research into recycling solutions," says Dr. Thorsten Dreier, Covestro's Chief Technology Officer. "The chemical recycling of polycarbonate is another example with which our colleagues in development show that closed cycles are possible in the future. We need to use end-of-life plastics as a resource and reuse them as alternative raw materials to close the loop."
The return of plastics through recycling replaces primary fossil raw materials in production. Comprehensive recycling thus contributes to climate neutrality and the protection of natural resources and the environment. Mechanical recycling of polycarbonate is already an important component of Covestro's recycling strategy. The mechanical recycling process is used whenever waste streams are sufficiently pure and the recycled polycarbonate meets the requirements profile of the future application.
Chemical recycling works in a complementary way to mechanical recycling - it converts plastic building blocks back into monomers, i.e. their individual building blocks. These can be separated and serve as raw materials for future plastic. Chemical recycling can therefore make larger waste streams that are unsuitable for mechanical processes in particular accessible for recycling; it allows the production of plastics that meet the highest quality requirements. Covestro is therefore actively developing chemical recycling.
The newly developed process, which was driven by an international team, is a specific chemolysis process adapted to polycarbonate. "Pre-sorted waste streams containing a product content of more than 50% polycarbonate can be recycled this way. This has been successfully demonstrated with various polycarbonate-containing plastic waste streams," explains Markus Dugal, Head of Process Technology at Covestro. "With the help of this chemolysis, the cycle can be closed to a direct precursor of polycarbonate. This makes the recycling process very sustainable."
The recycled product, a precursor of polycarbonate, can be mass-balanced and reused as a raw material for the production of polycarbonate without further processing.
Following successful development in the laboratory, the next stage of development, the technical implementation of a continuous process, has already started. A pilot plant, which is currently in the planning stage, will be used to gather the experience needed for further expansion to industrial scale. Millions of euros will be invested in this over the next few years. The pilot plant will be built in Leverkusen, Germany.
At the same time, Covestro says it is driving forward further processes for innovative recycling of polycarbonate in its research laboratories. These include chemolytic alternatives, recycling with enzymes that break down the plastic, and smart pyrolysis. Promising alternatives can also be tested with the pilot plant.
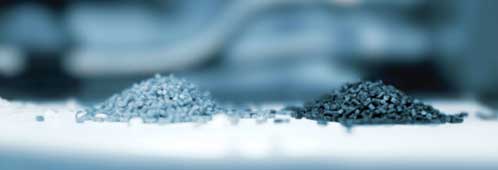
Meanwhile in other news, Swedish additives maker Nexam Chemical says it has been informed that the European Patent Office will approve a second important patent in Reactive Recycling technology. This complements the patent from July this year, concerning additives to recycle polypropylene (PP), with corresponding technology applied to polyethylene (PE). The patent covers a method that makes it possible to better recycle and thus increase the use of recycled PE. The method works extremely well for mechanical recycling and will reduce the use of virgin plastic in the manufacture of new products.
With the help of reactive chemistry, Nexam Chemical says it can now improve the process properties even of recycled PE, the most abundant plastic in the world.
PE is used in both packaging and technical products such as plastic bags, agricultural film, liquid containers, soft and hard food packaging, electrical cables and conduits.
"Nexam once again breaks new ground and broadens the field of use for Reactive Recycling and thus contributes to more sustainable solutions," said Christer Svanberg, Chief Technology Officer at Nexam Chemical and continues:
Nexam Chemical has developed a range of additives for rLDPE, rLLDPE and rHDPE. These include the Nexamite R301-305 additives that can be added to the extruder together with the PE to be mechanically recycled.
(IMA)Subscribe to Get the Latest Updates from IMA Please click here
©2023 Injection Moulding Asia. All rights reserved.