Green tie-ups: BASF/Sulzer to collaborate in renewable fuels/chemically recycled plastics; Ineos supplies Covestro with green acetone/phenol for PCs
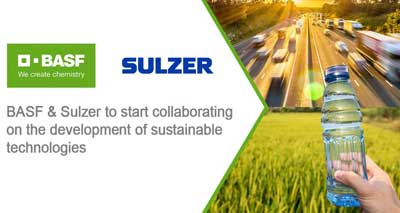
German materials firm BASF and Sulzer Chemtech (GTC Technology) have signed a Memorandum of Understanding (MoU) with the goal of advancing technologies for renewable fuels and chemically recycled plastics that will further expand the partners’ portfolio of sustainable solutions. The companies agreed to enter a strategic partnership to reduce the carbon intensity of renewable diesel and aviation fuel. They will also drive the development of a cost-effective chemical processing solutions to improve the conversion of plastic waste into new plastics. The collaboration combines complementary areas of expertise, integrating Sulzer Chemtech’s capabilities in licensed processing technologies and mass transfer equipment with BASF’s adsorbents and catalysts.
Sulzer Chemtech, an established licensor for process technologies for renewable fuels and chemical recycling of plastics, is leading efforts to harness resources that can help global producers achieve their net-zero ambitions. BASF Process Catalysts is driving multiple initiatives aimed at turning plastic waste into a secondary raw material, for example with its newly developed PuriCycle portfolio, as well as providing adsorbent and catalytic materials to produce clean and renewable fuels.
“Global plastic pollution and mobility are challenges that we can help to solve by joining forces with partners,” said Detlef Ruff, Senior Vice President, Process Catalysts at BASF. “This is why we at BASF are involved in key strategic collaborations aimed at protecting our planet's resources and transforming the way we do business. We are excited to work with Sulzer Chemtech and use our combined strengths to address plastic pollution and drive the adoption of more sustainable fuels.”
Torsten Wintergerste, President at Sulzer Chemtech, concludes: “Our process technology development team is continuously looking at new ways to support more sustainable, circular practices. The MoU with BASF allows us to broaden the scope of our portfolio and will lead to improved value offerings in both renewable fuels and the plastics recycling value chain. We look forward to working together to deliver advanced technologies that help our customers accelerate their path to net zero carbon emissions.”
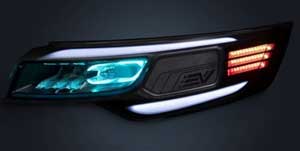
In other news, Germany-based Covestro will now be supplied with the two mass-balanced raw materials phenol and acetone from materials supplier Ineos’ Invirdis product range, produced using bio-attributed cumene by Ineos. Covestro will use it as a drop-in solution for polycarbonate products in automotive parts, housings for electronic devices, light guides and lenses, medical devices, and many other applications.
Lily Wang, global head of the Engineering Plastics segment, emphasises the further benefits for customers: "We offer them a drop-in solution that they can quickly and easily integrate into existing production processes without requiring any technical changes. The products show the same good quality as their fossil-based counterparts."
As part of the CQ family of circular solutions, Covestro offers them under the names Makrolon RE, Bayblend RE, Makroblend RE, and Apec RE. With its new CQ concept, Covestro says it highlights the alternative raw material basis in products and thus gives a clear indication to customers who are looking for such products.
The phenol and acetone are produced from bio-attributed cumene at Ineos’ Gladbeck and Antwerp sites – without competing with the food supply. Both sites are certified according to the internationally recognised ISCC PLUS as well as the RSB standard. The raw materials have a lower carbon footprint than petroleum-based products.
Gordon Adams, Business Director of Ineos Phenol, said, "This new product range provides our customers with drop-in product options that meet their stringent quality and performance requirements. At the same time, we’re moving the industry toward a more climate-friendly economy for phenol and acetone without compromising its unique product attributes."
(IMA)Subscribe to Get the Latest Updates from IMA Please click here
©2022 Injection Moulding Asia. All rights reserved.