Medical Sector: Technology shifts that make a difference
Today’s medical plastics allow healthcare devices and products to combine patient benefit and safety while also meeting the industry’s sustainability goals, says Angelica Buan in this report.
First, do no harm to the environmen
Hospitals and healthcare institutions are central to healthcare systems. While this sector works tirelessly around the clock to save lives, it also contributes significantly to carbon emissions due to the amount of medical waste generated and energy consumed. According to the 2019 Healthcare’s Climate Footprint report, healthcare’s climate footprint is equivalent to 4.4% of global net emissions, comparable to annual greenhouse gas emissions from 514 coal-fired power plants.
Medical waste is a major issue, particularly in areas where solid waste management systems are inadequate. The pandemic has made the situation even worse. As per a study published in the journal Proceedings of the National Academy of Sciences, over 8 million tonnes of pandemic-related plastic waste has been generated globally, with over 25,000 tonnes entering the global ocean. It was also found that the amount of medical waste generated was significantly higher than that produced by individuals. Asia accounted for 73% of all plastics discharged, followed by Europe (11%), and the rest coming from other regions.
Ultimately, consumers and producers are urged to be more conscious of the environmental impact of personal protective equipment (PPE) and other plastic products, as well as the development of much more sustainable materials and new waste management technologies. After all, plastics are required for the development of more effective, safe, and accessible medical devices.
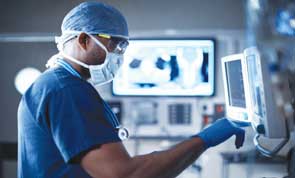
In response to this need, materials companies Solvay and Mitsubishi Chemical Advanced Materials (MCAM) recently collaborated to recycle medical equipment made with Solvay’s Udel high-performance polysulphone (PSU) thermoplastic at the end of its service life. The two companies – Solvay, with its One Planet sustainability roadmap, and MCAM, with its product sustainability Kaiteki vision, are currently investigating the implementation of logistics for the recovery, recycling, and reprocessing of PSU resin used in medical components, to be reused in original applications.
The project may be able to demonstrate that it is possible to recycle high- value Udel PSU parts used in the medical field, resulting in significant CO2 emissions savings throughout the production and supply chain.
The project entails combining MCAM’s expertise in washing and mechanically purifying the material with Solvay’s ability to evaluate the chemistry of the end-of-life polymer to establish a recycling strategy that will provide customers with materials that fully meet all specifications.
MCAM has previously collaborated with Solvay on the reclamation and recycling of other high-performance polymers, such as KetaSpire PEEK material.
Advanced materials to optimise device performance
Modern medical devices and intervention tools rely on advanced and functional materials to improve their capabilities and enable better patient compliance and outcomes. German materials supplier Covestro is one of these companies that is assisting in the ongoing development of medical plastics technologies.
Covestro’s Makrolon M6011 FR, a medical PC, and Makroblend M5005 FR, a medical PC/polyester blend, have been introduced by the company for medical device housings and hardware. The materials have a differentiated composition of properties that improve chemical resistance while employing next-generation flame retardants with the most stringent UL rating – UL 94 V-0. These materials are also said to demonstrate enhanced impact strength, rigidity, UV resistance, and improved flowability. Similarly, French chemicals firm Arkema has introduced a biobased and recyclable high rigidity advanced bio-circular PA11 medical polymer that is intended to replace metal and traditional polymers in demanding medical applications.
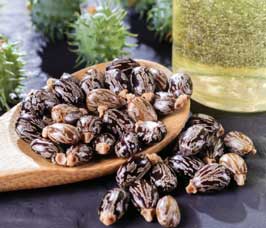
The new Rilsan MED grade, which is formulated with a high content (65%) of glass fibres, has a tensile modulus of 18.5GPa, making it suitable for the production of surgical tools.
The new polymer, derived from Arkema’s flagship amino 11, which is sourced from castor bean oil, is said to offer a combination of physical performance, lightweight, and sustainability. It also has favourable biocompatibility properties (which have been successfully assessed according to USP Class VI, ISO 10993-4, ISO 10993-5, and ISO 10993-10 standards), easy processability, lightweight, high resistance to aggressive chemical agents and repeated sterilisation cycles, and other properties.
(IMA)Subscribe to Get the Latest Updates from IMA Please click here
©2022 Injection Moulding Asia. All rights reserved.