Green news: Orlen Unipetrol to produce PP from waste vegetable oil; Elkem, Hydro and Altor to accelerate growth of Vianode’s sustainable battery materials
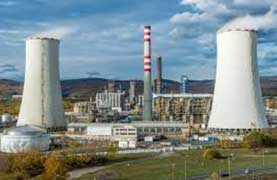
Polish refining and petrochemical group Orlen Unipetrol, in line with its investment of US$1.5 billion in developing sustainable projects and digitalisation and in line with its strategy to have recycled and renewable sources to contribute over 15% of its petrochemical products by 2030, is looking at waste vegetable oil recycling at its Litvínov refinery and using this to produce PP. After initial tests, it has now launched operating tests of adding a bio material – hydrogenated vegetable oil (HVO) – to the production process at the steam cracker.
The first tests of the use of HVO in the production process were carried out at the steam cracker in Litvínov in 2020 and 2021.
“We received the internationally recognised certification in November last year. We carried out another production, now fully certified test, at the end of the year. Thus, we produced the first dose of the certified PP. This so-called bio-circular material has the same quality as the material made of a fossil raw material. We can use this method to produce PP, PE, ethylene, and benzene,” explains Martin Růžička, Director of development, technologies and efficiency of the Orlen Unipetrol Group.
The produced PP will be used in subsequent research and tests with selected customers who will provide their valuable observations. The customers must also pass the certification to ensure that the entire process is compliant with the defined legislative standards. Thus, the final product produced from bio-circular Orlen Unipetrol petrochemicals will be a certified bio-circular product.
Besides HVO processing, the group is also testing the chemical recycling using the principles of pyrolysis or thermal degradation under high temperatures. This is a highly effective technology for the repeated use of waste raw materials. The technology can exploit the initial waste and convert it to hydrocarbons, reintegrating them into petrochemical production. This method enables the more effective use of the existing waste and significantly reduces the carbon footprint.
In 2021, Orlen Unipetrol researchers commissioned a test pyrolysis plastic waste recycling unit.
Orlen Unipetrol wants the recycled and renewable sources to contribute to up to 20% of the manufacture of its petrochemical products by 2030. The key petrochemical products of the group are PE under the Liten brand that is referring to the city of Litvínov and PP under the Mosten brand referring to the cities of Most, i.e. the cities between which the production area of Orlen Unipetrol is located.
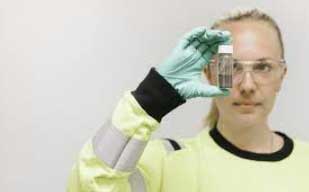
In other news, chemical firm Elkem, Hydro and Altor (Altor Fund V) are in a partnership with the intention to accelerate the growth of Vianode, a producer of sustainable battery materials. An investment decision for a potential first-phase plant at Herøya, Norway, is expected in the first half of 2022.
Vianode has developed a range of synthetic graphite products for batteries with unique performance characteristics and produced with significantly lower CO2 emissions than today's standard materials – supporting the ambitions of leading battery cell and automotive manufacturers. Today, an electric vehicle (EV) contains on average 40-70 kg of graphite, representing a vital component of the battery. Vianode's products are developed based on specialised know-how in high-temperature processes, closed production systems, lower energy consumption and access to renewable energy.
Founded in 2021, Vianode currently has around 50 employees. The company builds on Elkem's experience in advanced material solutions, its in-house R&D resources, as well as Vianode's industrial pilot plant in Kristiansand, Norway. After this transaction, Hydro and Altor will each have 30% ownership in Vianode, while Elkem will retain the remaining 40% ownership.
An investment decision for a potential first-phase plant for Vianode is expected during the first half of 2022. This plant will have approximately 100 employees and produce graphite for more than 20,000 EVs per year. A potential full-scale plant will produce graphite for more than 1 million/year EVs and is expected to increase the number of employees in Vianode to around 300, enabling more than 1,000 green jobs including external effects.
The total investments in the first-phase plant and preparations for a potential full-scale plant are estimated at around NOK2 billion. The plant development is pending clarifications related to framework conditions, including public support mechanisms and long-term access to competitive renewable energy and grid infrastructure.
"The market for battery materials is growing at an exponential rate and developing sustainable value chains is critical for the green transformation. Vianode aims to become a leading producer of sustainable battery materials, and this represents an attractive growth opportunity for Elkem. Hydro and Altor both add significant experience and expertise in developing large-scale industrial projects in the battery value chain. Through complementary skillsets, the partnership with Hydro and Altor will contribute to making Vianode a highly valuable contribution to the European battery value chain," says Elkem CEO, Helge Aasen.
"We are excited to partner up with Elkem and Altor to industrialise Vianode. We look forward to utilising our industry scaling capabilities including project execution for large industrial projects, our material and process competence and experience as well as our track record from serving the car OEM segments for decades. Vianode is a good fit for our strategic direction of growing in renewable energy and new-energy solutions," says Hilde Merete Aasheim, Hydro President/CEO.
The transaction is subject to formal approval by all parties and regulatory approvals, including competition authorities.
(IMA)Subscribe to Get the Latest Updates from IMA Please click here
©2022 Injection Moulding Asia. All rights reserved.